We have all encountered the challenges and delays that often come with QA processes, which can seem overly complex. But don’t worry, there are three effective strategies that can streamline our QA methods and greatly improve our efficiency.
These strategies have been proven to not only streamline QA workflows but also drive significant improvements in product quality. So, how exactly can we achieve this?
Let’s explore the game-changing lean strategies that are reshaping the landscape of QA efficiency.
Key Takeaways
- Analyzing QA processes to identify non-value-added activities
- Implementing lean principles and tools to reduce errors and waste
- Visualizing limitations and errors through value stream mapping
- Empowering employees with Quality at the Source (QATS) to detect defects and inefficiencies
Identifying Waste in QA Processes
We rigorously analyze our QA processes to pinpoint and eliminate any non-value-added activities, ensuring maximum efficiency and quality in our operations.
By leveraging lean principles, we focus on identifying waste in our QA processes to streamline operations and reduce errors. Implementing tools such as 5S methodology, JIT, Kanban systems, Poka-yoke, and Root Cause Analysis, we actively work towards eliminating waste and boosting efficiency.
Value stream mapping plays a crucial role in visualizing limitations and identifying errors, allowing us to make informed decisions to improve processes.
Moreover, empowering our employees with Quality at the Source (QATS) enables us to detect defects and inefficiencies during production, contributing to our overall quality management efforts.
Embracing a culture of continuous improvement through Kaizen, we make small incremental changes to enhance efficiency and quality.
Our commitment to identifying and eliminating waste in our QA processes is integral to our mission of delivering high-quality products and services while continuously improving our operations.
Implementing Continuous Improvement in QA
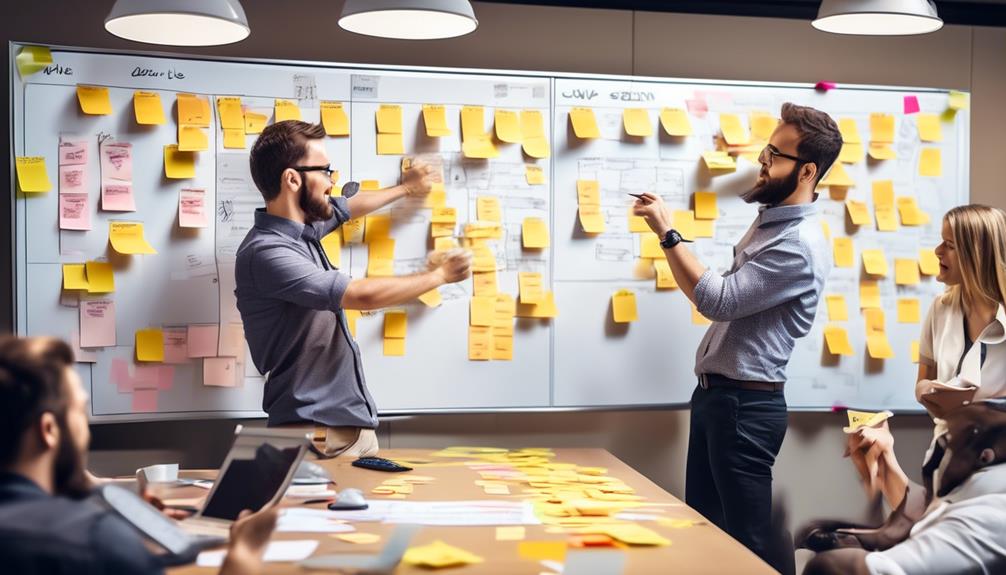
Implementing continuous improvement in QA involves fostering a culture of ongoing learning and enhancement within the quality assurance processes. By leveraging lean manufacturing principles and tools, Quality Assurance (QA) teams can identify and eliminate waste, reducing errors and inefficiencies in the production process. This approach not only aims to improve quality but also to enhance customer satisfaction.
Continuous improvement in QA entails empowering employees to detect defects and process issues during quality assurance activities. By implementing lean management techniques, such as Kaizen principles, small incremental changes can be made in QA processes, promoting a culture of ongoing improvement and efficiency. This approach is vital for reducing product defects, improving teamwork, and ultimately delivering high-quality products.
Through the implementation of lean strategies, QA teams can streamline work processes, leading to a reduction in waste and an increase in overall efficiency. As a result, the organization can achieve higher customer satisfaction levels and improved product quality.
Optimizing QA Workflow With Visual Management
Fostering a culture of ongoing learning and enhancement within the quality assurance processes, the implementation of visual management tools such as Kanban boards and dashboards provides real-time visibility into QA workflow and status. By utilizing lean principles, we can optimize the QA workflow through visual management techniques, leading to improved efficiency and quality in the manufacturing process.
Here’s how visual management can enhance QA workflow:
- Use value stream mapping to visualize and analyze the QA process, identifying bottlenecks and opportunities for improvement.
- Create visual work instructions and standardized procedures to ensure consistency and reduce errors in QA tasks.
- Utilize visual performance metrics and charts to track QA team productivity, defect rates, and process efficiency.
- Establish visual cues and signals in the work environment to facilitate quick identification of quality issues and promote immediate corrective action.
These visual management tools not only enable continuous flow within the QA process but also allow for quick problem-solving and decision-making, ultimately leading to improved product quality and customer satisfaction.
Frequently Asked Questions
What Is the Lean Process in Qa?
The lean process in QA involves applying lean management principles to quality assurance activities. We streamline processes, eliminate waste, and focus on continuous improvement to deliver high-quality products or services.
By reducing non-value-added activities and standardizing tasks, we enhance efficiency and minimize errors. This approach emphasizes customer satisfaction, competitive advantage, and cost savings.
What Is the Lean Approach to Quality Improvement?
We implement lean principles to improve quality by reducing waste and non-value-added activities. This involves streamlining processes, standardizing tasks, and continuously improving operations.
Lean techniques, such as 5S methodology and Root Cause Analysis, help identify and eliminate inefficiencies.
This approach fosters a culture of quality and drives customer satisfaction.
Through lean, we achieve operational excellence and competitive advantage, ensuring that our products and services meet the highest standards.
How Can Lean Production Improve Quality?
Lean production improves quality by:
- eliminating waste
- streamlining processes
- fostering continuous improvement
It enables us to:
- identify and address inefficiencies
- result in higher-quality products and services
By focusing on:
- value-added activities
- minimizing non-value-added tasks
We can enhance:
- product quality
- customer satisfaction
Lean principles also empower us to:
- respond quickly to process changes
- ensuring that quality remains a top priority throughout production.
How Does Lean Principles Contribute to Quality Control?
Lean principles contribute to quality control by identifying and eliminating waste, streamlining processes, and continuously improving product quality. This results in improved efficiency, cost savings, and enhanced customer satisfaction.
Conclusion
In conclusion, by implementing lean strategies like value stream mapping, Kaizen process improvement, and customer-focused optimization, we can trim the fat from our QA processes, fine-tune our efficiency, and deliver top-notch quality products.
Just as a sculptor chips away at a block of marble to reveal a masterpiece, we can chip away at waste and inefficiency to unveil the true potential of our QA efforts.
It’s all about precision, refinement, and continuous improvement.
Randy serves as our Software Quality Assurance Expert, bringing to the table a rich tapestry of industry experiences gathered over 15 years with various renowned tech companies. His deep understanding of the intricate aspects and the evolving challenges in SQA is unparalleled. At EarnQA, Randy’s contributions extend well beyond developing courses; he is a mentor to students and a leader of webinars, sharing valuable insights and hands-on experiences that greatly enhance our educational programs.