When quality assurance and efficiency combine forces, Lean QA methodologies present a promising opportunity. Implementing these tactics can result in process improvements, heightened productivity, and enhanced performance.
But how exactly can Lean QA practices revolutionize the traditional QA approach and lead to better efficiency? Let’s explore the potential benefits and practical strategies that make Lean QA an enticing proposition for organizations striving to optimize their QA processes and deliver superior results.
Key Takeaways
- Emphasizing continuous improvement and waste reduction is crucial in Lean QA practices
- Efficient resource utilization, including strategic allocation and leveraging automation, leads to cost-effective and high-quality product delivery
- Effective team utilization, through skills alignment, cross-training, and workload balancing, enhances overall efficiency in Lean QA practices
- Cultivating a continuous learning culture and iterative process improvement is essential for achieving continuous improvement and waste reduction in Lean QA practices
Understanding Lean QA Principles
Understanding Lean QA Principles is essential for optimizing efficiency and effectiveness in the software development process. Lean principles emphasize the importance of continuous improvement and waste reduction, which are crucial for enhancing productivity and quality. By embracing Lean QA Principles, teams can streamline their processes, identify and eliminate non-value-adding activities, and focus on delivering value to the customer. This means that every aspect of the software development lifecycle is evaluated to ensure that resources are utilized efficiently and effectively.
Incorporating Lean QA Principles involves a strategic approach to identifying areas of improvement and implementing changes that lead to better outcomes. It requires a thorough analysis of existing processes, a commitment to ongoing refinement, and a focus on delivering high-quality products. By adopting Lean principles, teams can create a culture of continuous improvement, where everyone is empowered to identify inefficiencies and contribute to waste reduction efforts.
In mastering Lean QA Principles, teams can achieve significant improvements in efficiency and effectiveness, ultimately delivering greater value to their customers while optimizing their own processes.
Identifying Process Inefficiencies
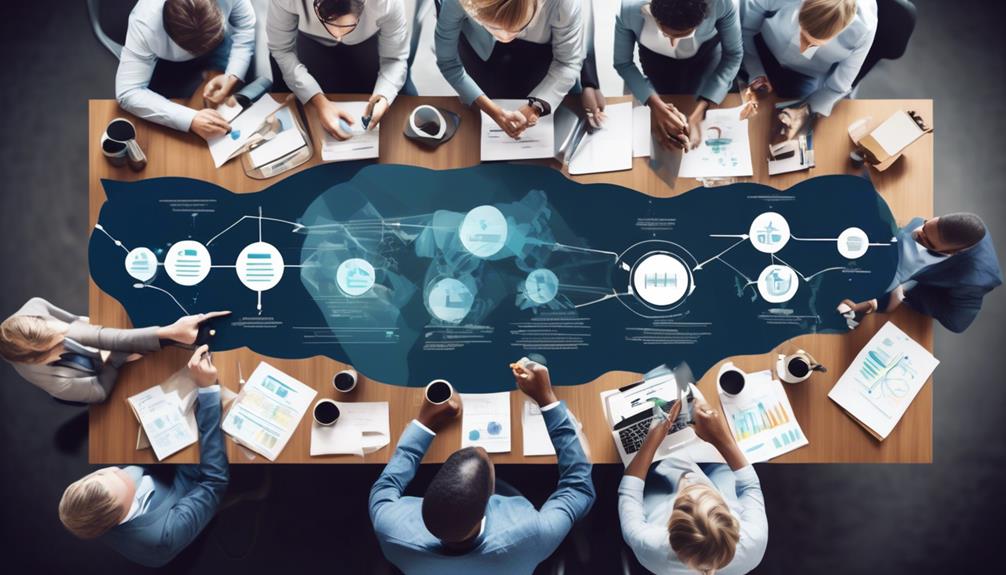
Embracing Lean QA Principles empowers teams to meticulously assess their processes, enabling the identification of inefficiencies that hinder productivity and quality in software development. By leveraging lean principles, teams can effectively identify and eliminate waste activities, thus promoting process efficiency and enhancing customer value.
Key techniques and strategies for identifying process inefficiencies include:
- Visual Management: Implementing visual management techniques, such as Kanban boards, enhances collaboration and provides a clear overview of tasks, making it easier to identify process inefficiencies.
- Waste Reduction: Lean principles emphasize waste reduction, enabling teams to scrutinize processes and eliminate non-value-added activities that impede efficiency.
- Continuous Improvement: By continuously assessing and identifying process inefficiencies, teams can drive ongoing improvements, ensuring the elimination of waste and enhanced operations.
- Value Stream Mapping: Analyzing the value stream through lean principles allows teams to identify and eliminate inefficiencies, creating a streamlined and efficient workflow.
- Root Cause Analysis: Applying lean principles involves conducting thorough root cause analysis to identify the underlying factors contributing to process inefficiencies, enabling targeted improvement efforts.
Through the application of lean principles and continuous improvement, teams can systematically identify and address process inefficiencies, leading to cost-effective quality assurance and heightened operational efficiency.
Eliminating Non-Value Adding Activities
Identifying and eliminating non-value adding activities is a pivotal aspect of optimizing work processes and enhancing operational efficiency in quality assurance and software development. By applying lean principles and continuous improvement, organizations can eliminate waste and streamline their value stream, leading to improved customer satisfaction and cost-effective quality assurance. The process of eliminating non-value adding activities involves conducting value stream mapping to identify areas of waste and inefficiency. Once these activities are identified, organizations can then focus on eliminating them to create a more efficient and effective workflow. This not only leads to quicker delivery and better product quality but also ensures that resources are utilized in the most productive manner. The table below provides a snapshot of the benefits of eliminating non-value adding activities in quality assurance and software development.
Benefits of Eliminating Non-Value Adding Activities |
---|
Streamlines work processes |
Reduces waste in quality assurance and operational processes |
Enhances customer satisfaction through quicker delivery and better product quality |
Ensures cost-effective quality assurance |
Supports lean principles and continuous improvement cycle |
Optimizing Resource Utilization
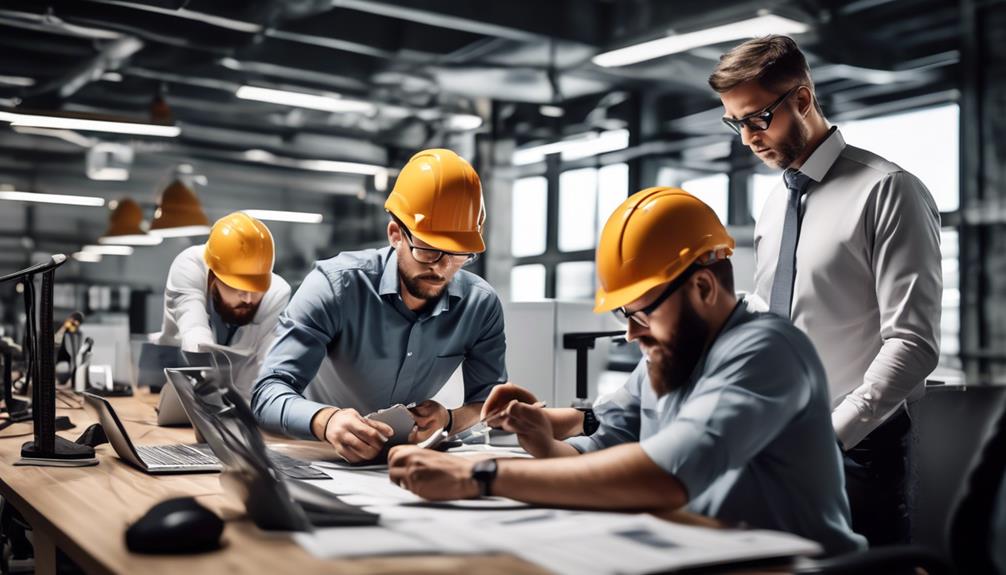
As we move into the topic of optimizing resource utilization, it’s crucial to consider our resource allocation strategy, eliminating waste, and ensuring efficient team utilization.
By strategically allocating resources, we can eliminate unnecessary waste and ensure that each team member’s skills are utilized effectively.
This approach not only streamlines our processes but also contributes to cost-effective and high-quality product delivery.
Resource Allocation Strategy
To achieve optimal resource utilization in Lean QA practices, a systematic and strategic approach to resource allocation is essential for streamlining operations and minimizing waste. By implementing Lean principles and continuous improvement, organizations can effectively allocate resources to enhance efficiency and quality in their QA processes.
This involves identifying and eliminating waste in resource allocation, ensuring that the right resources are allocated at the right time for the right tasks. Key strategies for resource allocation include prioritizing tasks based on their impact, leveraging automation and tools to optimize resource usage, cross-training team members to increase flexibility, and regularly reviewing and adjusting resource allocation based on performance metrics.
Through these strategies, organizations can maximize efficiency and quality while minimizing waste in their QA practices.
Eliminating Waste
Lean QA practices strive to optimize resource utilization by eliminating waste and streamlining operations through continuous improvement and strategic resource allocation strategies.
Waste reduction is a fundamental aspect of Lean principles, aiming to enhance efficiency and productivity. By eliminating unnecessary processes and inefficient resource allocation, teams can declutter the system and enhance quality while reducing costs.
Lean management empowers teams to continuously improve processes and make strategic decisions for efficient resource utilization. Continuous improvement through Lean principles leads to streamlined operations and efficient resource allocation.
Embracing Lean QA practices enables organizations to eliminate waste, optimize resource utilization, and ultimately achieve higher levels of efficiency and productivity.
It’s crucial to implement processes to enhance resource utilization and eliminate waste in order to achieve the full potential of Lean QA practices.
Efficient Team Utilization
Utilizing our team’s skills and capacities efficiently is a crucial component of optimizing resource utilization within Lean QA practices. By ensuring efficient team utilization, we can adhere to lean principles, drive continuous improvement, and reduce waste in our processes, ultimately enhancing overall efficiency.
- Skill Alignment: Align team members’ skills with tasks to maximize productivity and quality.
- Cross-Training: Cross-train team members to build flexibility and fill skill gaps.
- Workload Balancing: Distribute work evenly to prevent overburdening and underutilization.
- Feedback Mechanisms: Implement feedback loops to identify and address inefficiencies promptly.
- Task Automation: Automate repetitive tasks to free up time for higher-value activities.
Efficient team utilization not only supports lean principles but also fosters a culture of continuous improvement, waste reduction, and heightened efficiency across our QA processes.
Implementing Continuous Improvement
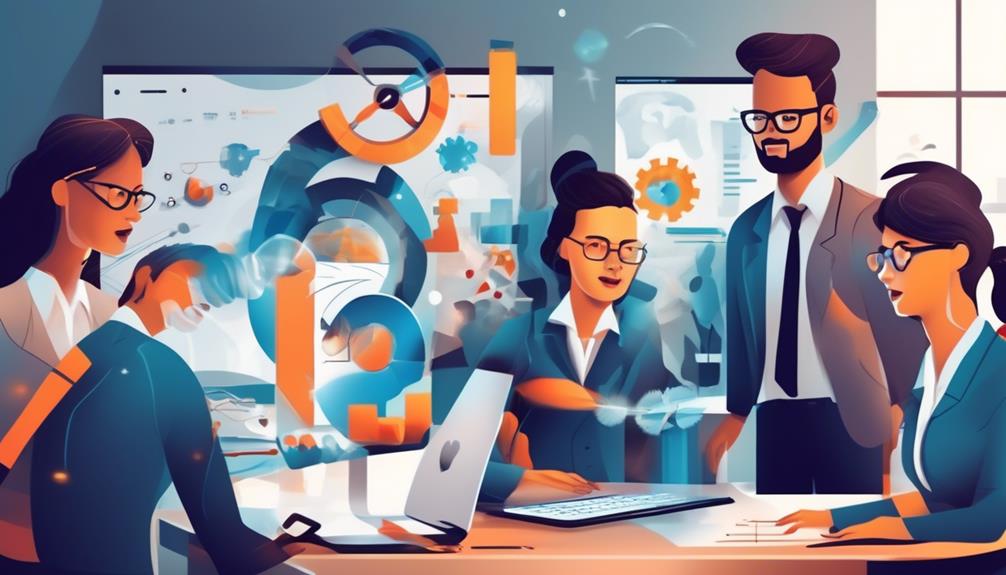
As we move into the topic of implementing continuous improvement, it’s essential to consider the points of continuous learning culture and iterative process improvement. These aspects play a crucial role in fostering a mindset of ongoing refinement and development within our quality assurance practices.
Continuous Learning Culture
To foster a culture of continuous learning and growth within an organization, it’s essential to embrace a mindset that values ongoing improvement and adaptation in response to evolving environments and market demands. Embracing lean principles and implementing continuous improvement are vital for enhancing operational efficiency and ensuring customer satisfaction.
In this environment, a continuous learning culture can be cultivated by encouraging employees to seek out new knowledge and skills, fostering an environment where mistakes are viewed as learning opportunities, and emphasizing the importance of ongoing education and development.
By doing so, organizations can promote learning and innovation, enabling them to remain competitive and agile in an ever-changing business landscape.
- Encourage employees to seek out new knowledge and skills
- Foster an environment where mistakes are viewed as learning opportunities
- Emphasize the importance of ongoing education and development
- Promote learning and innovation
- Remain competitive and agile
Iterative Process Improvement
In our pursuit of a culture of continuous learning and growth, we now focus on the iterative process improvement, a method that involves continuously refining and enhancing processes over time to ensure operational efficiency and customer satisfaction. Iterative Process Improvement is rooted in lean principles and is vital for achieving continuous improvement and waste reduction. By identifying, implementing, and measuring changes, we can streamline work processes, enhance efficiency, and improve productivity. This cycle of evaluating processes for effectiveness and making ongoing quality impacts ensures that customer value is maximized and waste is eliminated. The following table highlights the key aspects of iterative process improvement:
Key Aspects | |||
---|---|---|---|
Continuous Improvement | Waste Reduction | Lean Principles | Customer Value |
Evaluating | Implementing | Measuring | Enhancing |
Impact of Cycles on Quality
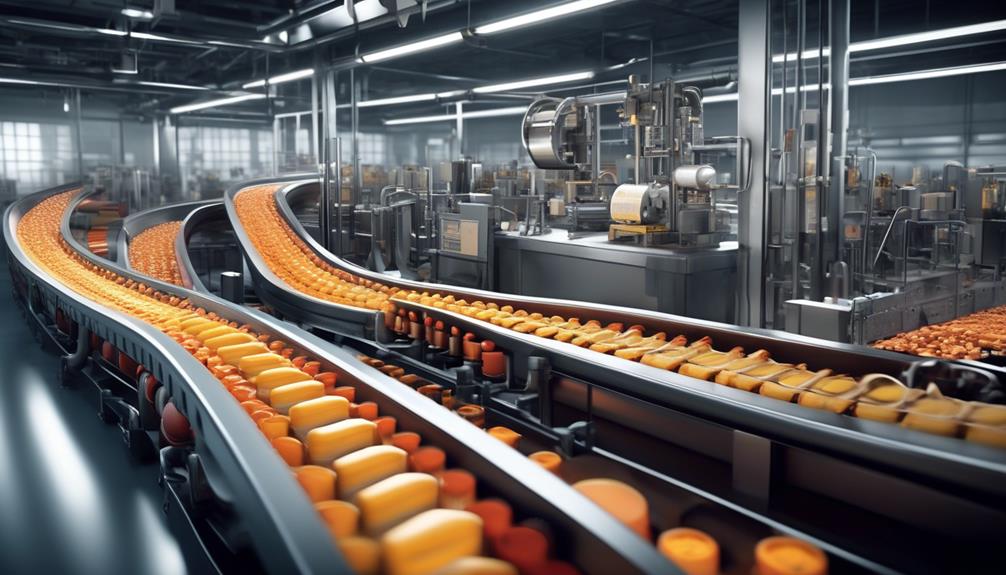
Continuous improvement cycles in lean practices result in ongoing enhancements in quality and efficiency, leading to streamlined work processes and improved customer satisfaction. Implementing and evaluating continuous improvement cycles is essential for eliminating waste and improving operations.
By adhering to lean principles, organizations can ensure high-quality product delivery through the implementation and evaluation of continuous improvement cycles. This approach results in a significant boost in customer satisfaction as products and services are continually refined to meet or exceed customer expectations.
Additionally, continuous improvement cycles lead to streamlined work processes, improved teamwork, and morale, as employees see the direct impact of their efforts on the quality of the final output. This strategic approach to quality management ensures that the process remains dynamic and responsive to changing customer needs and market demands.
As a result, organizations can maintain a competitive edge and build long-term customer loyalty.
Enhancing Customer Satisfaction
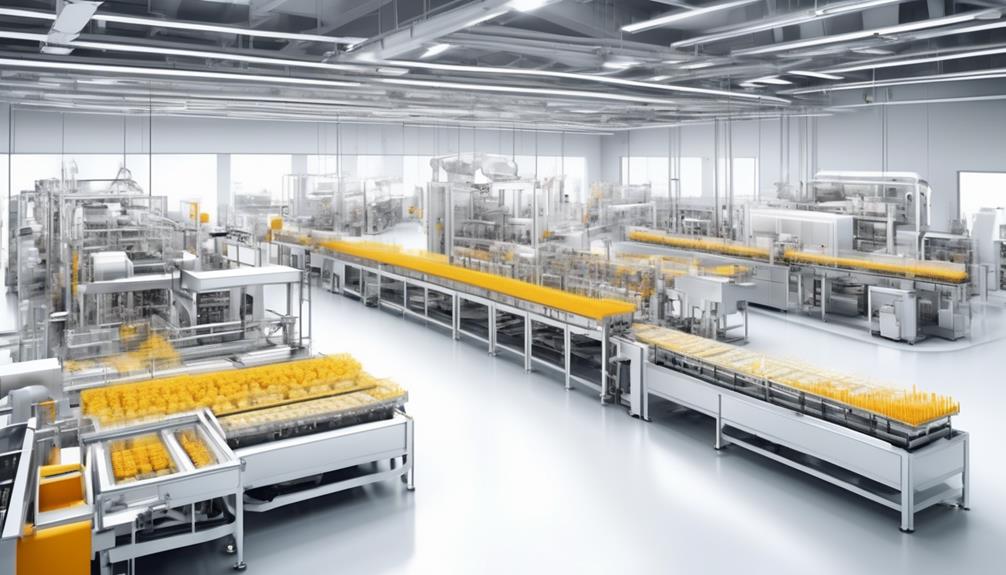
Enhancing customer satisfaction is a natural outcome of the continuous improvement cycles and waste reduction achieved through lean principles, resulting in quicker delivery, better product quality, and increased consistency.
Lean management fosters a customer-centric approach, focusing on delivering value to customers. By tailoring offerings based on customer feedback, lean practices ensure that products and services meet and exceed customer expectations. This customer-centric approach not only enhances satisfaction but also builds long-term loyalty.
Incorporating continuous improvement and waste reduction into the production process enables organizations to consistently deliver high-quality products that align with customer needs. Lean principles emphasize the importance of using customer feedback to drive product enhancements, ensuring that the overall experience is continually refined.
Furthermore, the emphasis on waste reduction directly impacts customer satisfaction by streamlining processes and eliminating inefficiencies that can lead to delays or inconsistencies in product delivery. This results in a more reliable and predictable experience for customers, contributing to their overall satisfaction with the products and services provided.
Streamlining Work Processes
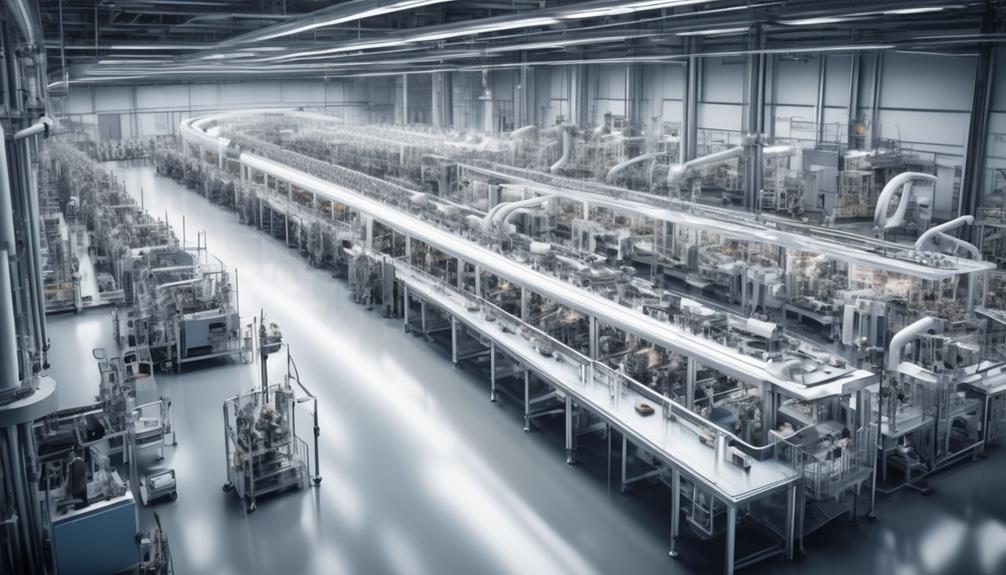
We can enhance efficiency by:
- Eliminating unnecessary steps and simplifying the allocation of tasks within our work processes.
- Optimizing processes to reduce the time and effort required to complete tasks, allowing us to focus on more critical activities.
Standardizing and automating processes can also help to:
- Improve consistency.
- Reduce the likelihood of errors.
Efficiency Through Elimination
Streamlining work processes is essential for maximizing efficiency and eliminating waste in QA practices. By embracing lean principles, continuous improvement is achievable through the elimination of non-value-added activities.
This approach leads to standardized and automated tasks, saving time and reducing errors. Standardized processes also improve consistency and quality assurance, contributing to streamlined work processes.
The time-saving aspect of streamlined work processes allows for more focus on critical tasks, ultimately enhancing overall efficiency.
By eliminating waste and non-essential activities, lean QA practices pave the way for a more efficient and effective workflow, creating a foundation for continuous improvement.
- Embracing lean principles
- Continuous improvement through waste reduction
- Standardized and automated tasks
- Enhanced consistency and quality assurance
- More focus on critical tasks
Simplifying Task Allocation
By focusing on simplifying task allocation, we can effectively streamline work processes and enhance overall efficiency. Lean principles emphasize waste reduction and continuous improvement, making it crucial to eliminate unnecessary tasks and allocate work efficiently.
This involves standardizing processes and automating repetitive tasks to reduce errors and save time. Standardization not only improves consistency and quality assurance but also allows for the allocation of more meaningful tasks, ultimately enhancing work process efficiency.
Embracing Lean principles also fosters teamwork and boosts morale by promoting operational transparency, defining clear roles and responsibilities, and encouraging a problem-solving approach.
Process Optimization Techniques
To enhance work process efficiency, we can now focus on implementing process optimization techniques that streamline tasks and eliminate waste, building upon the foundation of simplifying task allocation.
By applying lean principles and continuous improvement methodologies such as the Toyota Production System, we can achieve significant waste reduction and improved productivity.
Process optimization techniques involve standardizing and automating tasks to reduce errors and save time, allowing for a more efficient allocation of resources. This standardization also enhances consistency and quality assurance in work processes, contributing to overall efficiency.
Through the elimination of waste in work processes, organizations can achieve higher levels of productivity and effectiveness, ultimately leading to better outcomes.
- Standardizing tasks and reducing errors through process automation
- Achieving time-saving benefits for more important tasks
- Improving consistency and quality assurance through standardized processes
- Applying lean principles and continuous improvement methodologies
- Eliminating waste in work processes
Fostering Team Collaboration
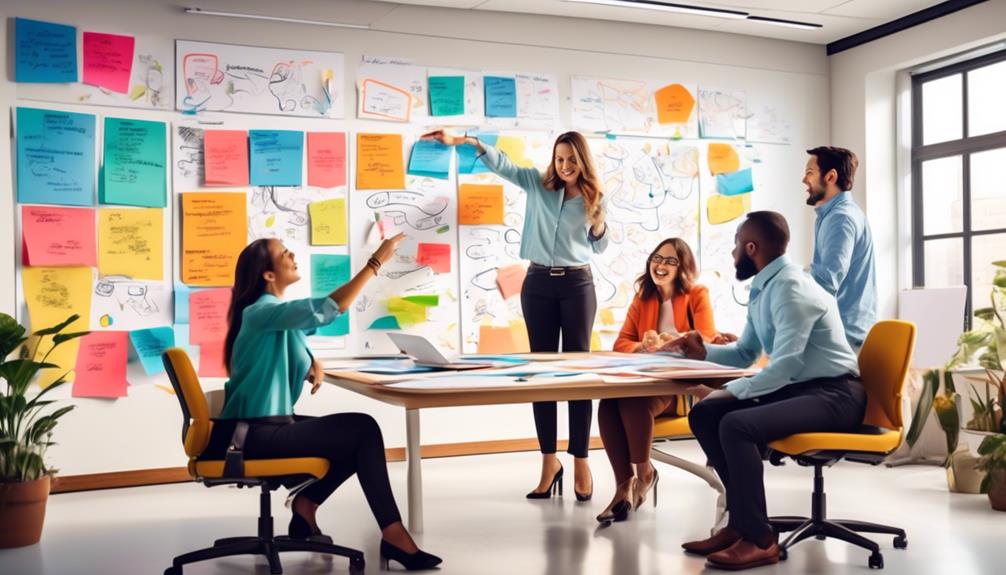
Encouraging open communication and idea sharing among team members fosters a collaborative environment that promotes innovation and efficiency. By fostering a culture of transparent communication, team members can freely exchange thoughts and insights, leading to a collective pool of ideas for continuous improvement.
Establishing clear roles and responsibilities further promotes collaboration and accountability, ensuring that everyone understands their contribution to the team’s objectives.
Embracing a problem-solving approach also fosters teamwork and morale, as team members feel empowered to address challenges collectively.
Implementing lean principles helps in promoting a shared leadership and accountability culture within the team, where everyone takes ownership of the process and outcomes.
Visual management techniques, such as Kanban boards, can enhance collaboration by providing transparency and clarity on the status of work, fostering incremental enhancements through continuous improvement.
This collaborative environment not only strengthens team dynamics but also drives efficiency and innovation, making it a crucial aspect of embracing lean QA practices.
Ensuring High-Quality Deliverables
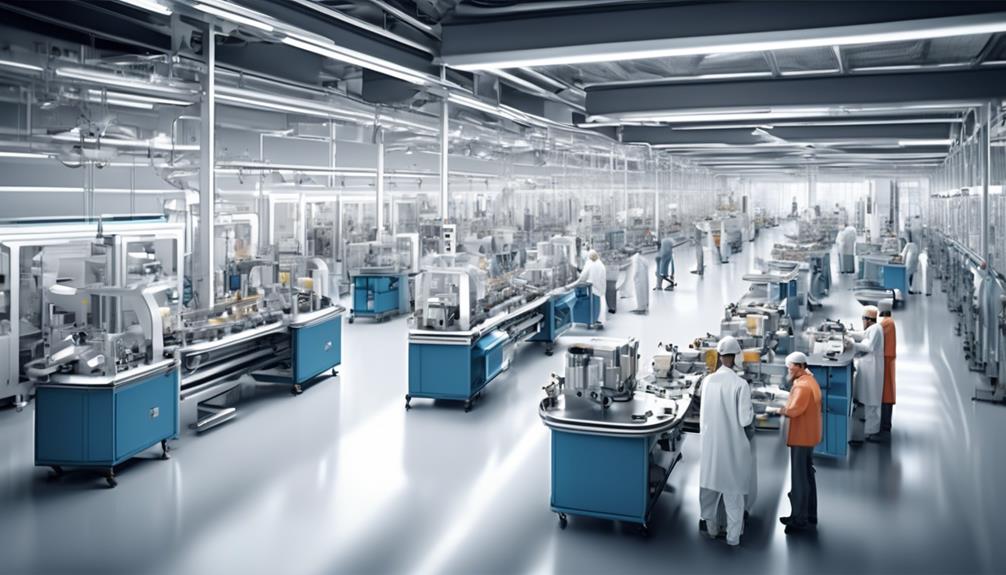
Transitioning from fostering team collaboration, we focus on ensuring high-quality deliverables through lean QA practices, which are instrumental in boosting efficiency and streamlining work processes to improve product quality.
- Lean QA practices ensure high-quality deliverables by boosting efficiency in operations.
- Waste reduction through Lean QA aids in streamlining work processes and improving product quality.
- The continuous improvement cycle of Lean QA leads to increased customer satisfaction and consistent delivery of quality products.
- Lean QA practices promote cost-effective quality assurance through efficient resource allocation and streamlined processes.
- Aligning business and QA objectives with Lean principles fosters a customer-centric approach and enhances the focus on delivering high-quality products.
Cost-Effective QA Strategies
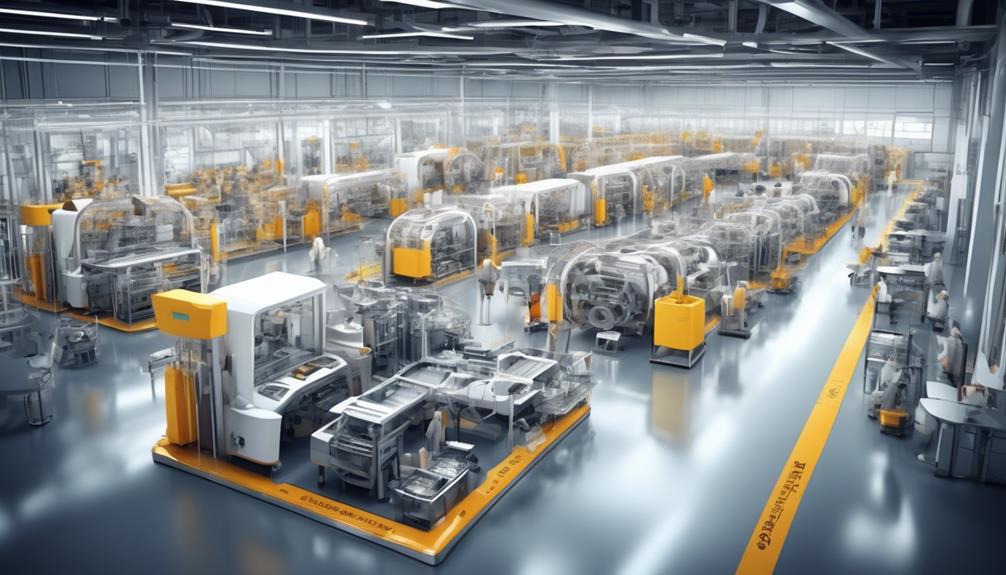
Embracing lean principles allows us to implement cost-effective QA strategies that optimize budget utilization and enhance overall efficiency. By integrating the principles of lean into our QA processes, we can effectively reduce waste and unnecessary costs.
This entails streamlining processes to minimize expenses while maintaining high-quality standards. In today’s competitive business landscape, it’s crucial to allocate resources efficiently to maximize ROI. Lean QA practices emphasize continuous improvement, which not only enhances the quality of deliverables but also reduces costs over time.
Through a strategic approach to QA, we can identify and eliminate non-value adding activities, thus reducing overall expenses. By prioritizing waste reduction and efficient resource allocation, we can achieve a cost-effective QA strategy that aligns with the principles of lean.
This approach not only ensures high-quality deliverables but also contributes to the overall financial health of the organization. As we strive for excellence in QA, embracing cost-effective lean strategies becomes imperative for sustained success in a competitive market.
Aligning Business and QA Goals
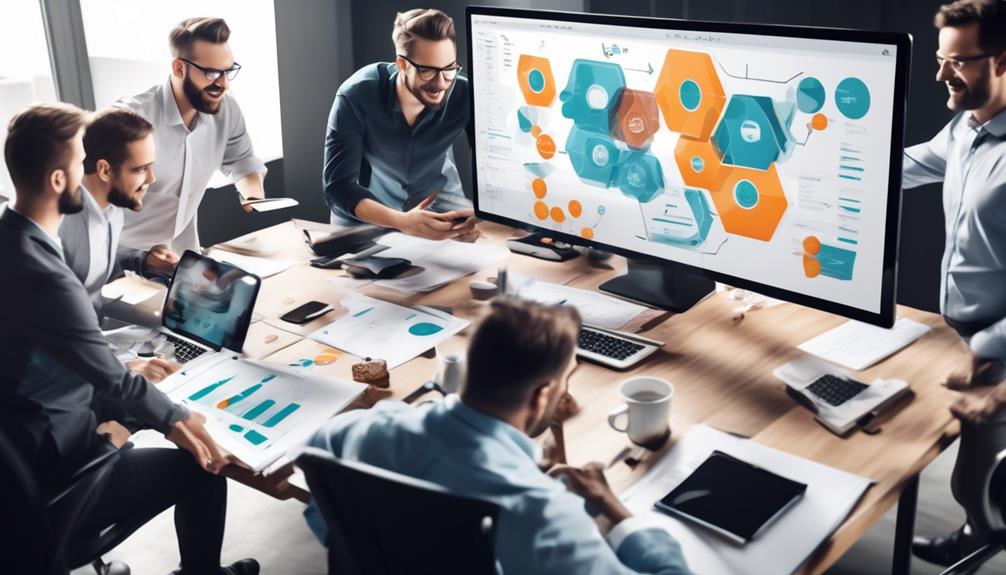
Collaborating closely with business stakeholders, we ensure a shared focus on delivering value to our customers. Aligning business and QA goals is essential for optimizing processes and achieving continuous improvement.
By integrating Lean principles, we can streamline processes and reduce waste, ultimately enhancing efficiency and customer satisfaction. This alignment fosters a culture of continuous improvement, where both business and QA teams work together to identify areas for optimization and prioritize customer value.
Clear communication and shared goals between these teams are fundamental for successful implementation of Lean principles and process optimization. Through this collaboration, we can ensure that business strategies are aligned with QA objectives, resulting in a harmonized approach focused on customer satisfaction and product quality.
Integration of Lean principles
Streamlined processes
Continuous improvement
Waste reduction
Process optimization
Frequently Asked Questions
What Is the Primary Purpose of the Lean Method of Quality Improvement?
The primary purpose of the lean method of quality improvement is to eliminate wasteful utilization of time, effort, or finances.
Lean management aims to generate value for customers by examining each stage of a business process. It helps identify and eliminate waste activities in IT operations, leading to a streamlined and effective quality assurance process.
Lean principles foster a culture of collaboration and innovation, empowering teams to make decisions and take ownership for continuous improvement.
What Does It Mean to Use Lean in Quality Assurance?
Using Lean in quality assurance means:
- Identifying and eliminating waste activities
- Fostering continuous improvement
- Enhancing efficiency and teamwork
It leads to:
- Consistent delivery of high-quality products and services
- Ultimately boosting customer satisfaction
Lean principles significantly improve:
- Efficiency and productivity
- Streamlining work processes
- Reducing costs
Embracing Lean in quality assurance is crucial for:
- Achieving optimal performance and effectiveness
- Delivering top-notch products and services.
What Are the Benefits of the Lean Approach?
Benefits of the lean approach include:
- Enhanced efficiency
- Waste reduction
- Continuous improvement
- Increased customer satisfaction
- Streamlined work processes
These advantages stem from a focus on:
- Eliminating non-value-adding activities
- Optimizing resources
- Fostering a culture of continuous improvement
By embracing lean QA practices, we can achieve:
- Operational excellence
- Deliver higher quality products
- Meet customer needs more effectively
This positions our organization for sustained success in a competitive market.
What Is the Use of Lean Systems to Improve Quality?
Using lean systems to improve quality involves streamlining processes, reducing waste, and focusing on continuous improvement. By implementing lean QA practices, we can identify and eliminate inefficiencies, leading to higher quality products and services.
This approach emphasizes customer value and empowers teams to deliver better results with fewer resources. Lean systems also promote a culture of collaboration, innovation, and adaptability, ultimately enhancing overall efficiency and effectiveness.
Conclusion
In conclusion, embracing Lean QA practices is essential for achieving better efficiency in our work processes.
Just like a well-oiled machine, Lean QA principles help us identify inefficiencies, eliminate waste, optimize resources, and continuously improve our quality assurance practices.
By aligning our business and QA goals, we can deliver high-quality products, improve teamwork, and ultimately increase customer satisfaction.
It’s the key to streamlining our operations and staying competitive in the market.
Randy serves as our Software Quality Assurance Expert, bringing to the table a rich tapestry of industry experiences gathered over 15 years with various renowned tech companies. His deep understanding of the intricate aspects and the evolving challenges in SQA is unparalleled. At EarnQA, Randy’s contributions extend well beyond developing courses; he is a mentor to students and a leader of webinars, sharing valuable insights and hands-on experiences that greatly enhance our educational programs.