How can a manufacturing company ensure compliance with ISO 9001 standards?
Well, the answer lies in a comprehensive checklist that covers all the essential aspects of quality management systems.
From understanding the ISO 9001 requirements to engaging stakeholders for commitment, each step plays a crucial role in ensuring compliance and driving business success.
But what are the specific details that make up this essential checklist?
Let’s explore the key components that can help manufacturing organizations navigate the path to ISO 9001 compliance and operational excellence.
Key Takeaways
- Understanding ISO 9001 requirements and creating a comprehensive checklist is crucial for ensuring compliance in manufacturing.
- Regular audits and reviews using the checklist help maintain comprehensive compliance and foster a culture of quality.
- Compliance monitoring and implementing corrective actions based on checklist findings drive ongoing improvement in the manufacturing process.
- Engaging stakeholders for commitment and continuous improvement is essential in maintaining compliance and achieving quality management objectives.
Understanding ISO 9001 Requirements
Understanding ISO 9001 requirements involves a meticulous examination of its ten clauses, aligning documentation, policies, processes, and performance metrics to ensure a robust quality management system. Each clause represents a critical aspect of the QMS, such as leadership commitment, resource management, and continual improvement. To meet ISO 9001 requirements, organizations must establish clear objectives, implement effective processes, and monitor performance against defined metrics.
Creating a comprehensive ISO 9001 checklist is essential for ensuring compliance. The checklist should systematically cover all ten clauses, providing detailed guidance on the requirements of each. It should be user-friendly, enabling easy navigation and understanding for all stakeholders involved in QMS. Regular internal or external audits using the checklist help identify areas for improvement and track the progress of corrective actions. Additionally, involving key stakeholders in the checklist process fosters a culture of quality and continuous improvement.
Understanding ISO 9001 requirements and diligently applying them through an effective checklist is fundamental to achieving and maintaining a robust QMS. It not only ensures compliance with the standard but also drives organizational excellence and customer satisfaction.
Creating a Comprehensive Checklist
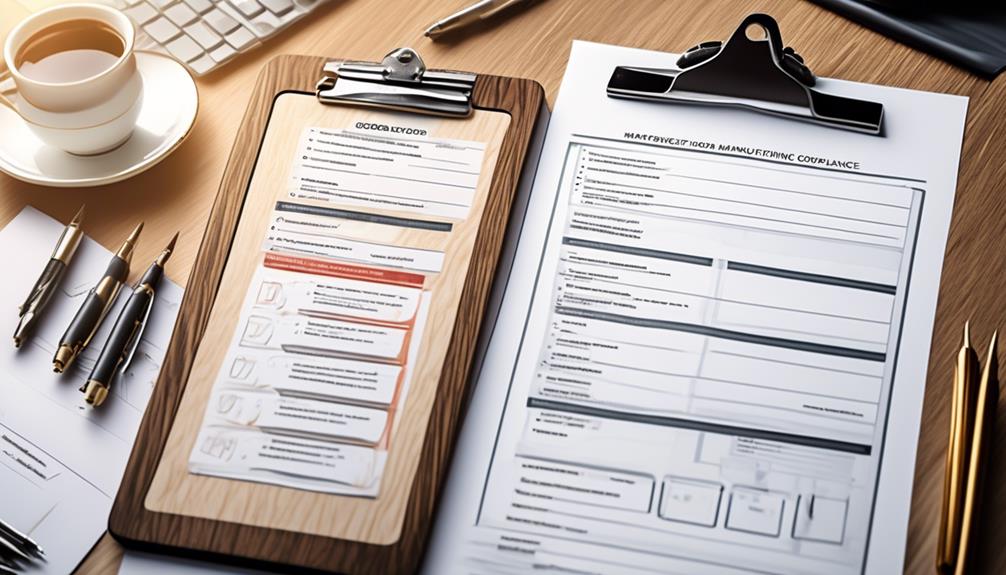
Let’s begin by outlining the essential elements of a comprehensive checklist to ensure manufacturing compliance.
We’ll cover the key compliance points that need to be included in the checklist, as well as the essential audit items that will help assess adherence to ISO 9001 requirements.
Our focus will be on creating a user-friendly and easily accessible checklist that aligns with the documentation, policies, procedures, roles, and responsibilities outlined in ISO 9001.
Checklist Essentials
using the checklist as a reference
- Use the checklist to track the progress of corrective actions
- Measure the performance of the quality management system
- Identify areas for further improvement.
Key Compliance Points
In order to establish a comprehensive checklist for manufacturing compliance, we must now focus on the key compliance points, ensuring that every aspect of each ISO 9001 clause is thoroughly covered and aligned with standard requirements.
Our checklist should encompass all elements of ISO 9001, including quality management, resource management, product realization, and measurement and improvement. Regular review and updates are essential to ensure ongoing compliance with ISO 9001 standards.
The checklist also serves as a reference for conducting internal or external audits, tracking the progress of corrective actions, measuring QMS performance, and identifying areas for improvement.
It’s crucial to engage stakeholders, involving quality managers, executives, and team members in the checklist process to maximize buy-in and commitment.
Essential Audit Items
After carefully analyzing the ISO 9001 requirements, we’ve identified essential audit items that must be included to create a comprehensive checklist for manufacturing compliance. When developing the checklist, it’s crucial to cover all aspects of each ISO 9001 clause, including documentation, policies, procedures, roles, and responsibilities.
Utilize tools such as spreadsheets, databases, or specialized software to ensure the checklist is user-friendly and accessible. Regular internal or external audits should be conducted using the ISO 9001 checklist as a reference to ensure all relevant aspects are covered.
Additionally, the checklist should be used to track the progress of corrective actions, measure QMS performance, and identify areas for improvement. Engaging stakeholders, including quality managers, executives, and operations, in the checklist process is essential to maximize buy-in and commitment.
Conducting Regular Audits and Reviews
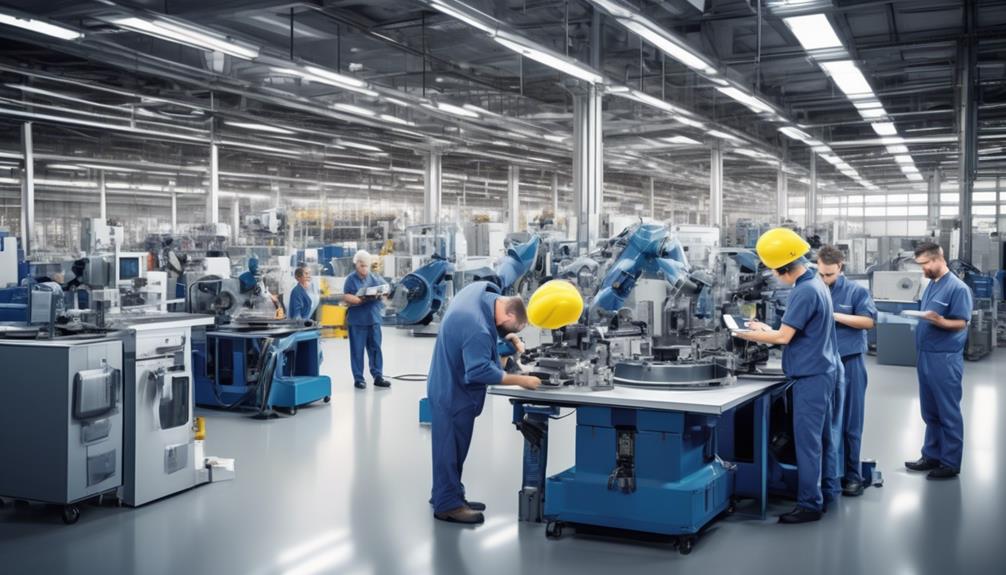
We regularly conduct internal and external audits to ensure compliance with the ISO 9001 standard.
During these audits, we utilize the ISO 9001 checklist as a reference to cover all relevant aspects and identify any gaps or areas for improvement.
Our review process involves updating the checklist based on audit findings and recommendations, ensuring ongoing compliance with the standard.
Audit Frequency
To ensure comprehensive compliance with ISO 9001 standards, a regular schedule of internal or external audits using the ISO 9001 checklist is essential. This ensures that all relevant aspects are covered and any gaps or areas for improvement are identified.
The audit findings serve as valuable input for updating the Internal Audit Checklist and making necessary improvements. Regular review of the checklist guarantees ongoing compliance with the ISO 9001 standard, reflecting a commitment to continual improvement.
This systematic approach not only ensures compliance but also fosters a culture of quality and excellence within the manufacturing process.
Review Process
Regularly conducting internal and external audits using the ISO 9001 checklist ensures comprehensive coverage of all relevant aspects and facilitates the identification of gaps and areas for improvement. The review process is essential for maintaining manufacturing compliance. We regularly update the ISO 9001 checklist based on audit findings and recommendations to ensure ongoing alignment with the standard. Here’s an emotional table to illustrate the importance of the review process:
Benefits of Review Process | Emotions Evoked |
---|---|
Ensures ongoing compliance | Confidence |
Identifies areas for improvement | Determination |
Facilitates comprehensive coverage | Assurance |
Promotes continual improvement | Optimism |
Enhances overall manufacturing | Satisfaction |
Regular reviews are crucial for ensuring that the ISO 9001 standards are consistently met, and for driving continual improvement in our manufacturing processes.
Compliance Monitoring
Conduct regular internal or external audits using the ISO 9001 checklist to ensure compliance with manufacturing standards. This proactive approach is essential for maintaining adherence to ISO 9001 requirements. By conducting regular audits, manufacturers can identify areas for improvement and ensure ongoing compliance. Utilizing the checklist as a reference during audits ensures that all pertinent aspects are thoroughly covered.
Audit findings serve as a valuable tool for pinpointing gaps and opportunities for enhancement. Furthermore, updating the checklist based on audit recommendations and findings is crucial for continuous improvement. Regular reviews of the checklist are necessary to guarantee ongoing compliance with ISO 9001 standards.
- Regularly conduct internal or external audits using the ISO 9001 checklist to ensure compliance.
- Use the checklist as a reference during audits to cover all relevant aspects.
- Identify gaps and areas for improvement through audit findings.
- Update the checklist based on audit recommendations and findings.
Implementing Corrective Actions
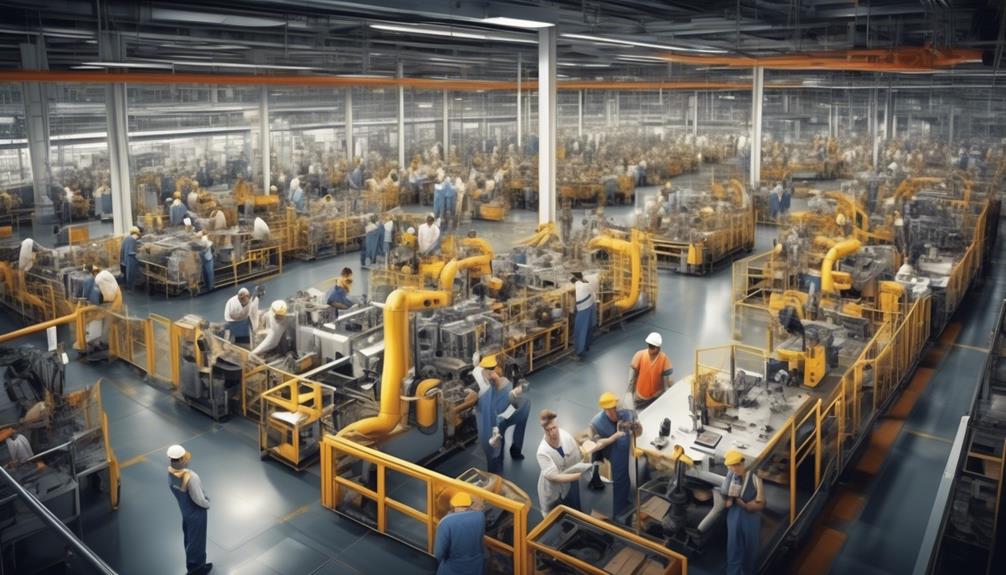
Upon identifying corrective actions based on ISO 9001 checklist findings, it’s imperative to ensure their effectiveness and sustainability for continuous quality improvement.
Implementing corrective actions is a crucial step in the quality management system (QMS) to address nonconformities and drive improvement. Once the corrective actions are determined, they must be promptly put into effect, with clear responsibilities assigned to individuals or teams.
Regular monitoring is essential to verify that the corrective actions are achieving their intended outcomes and that they’re sustainable over time. This involves measuring the performance of the QMS using the checklist to ensure that the corrective actions have resulted in the desired improvements.
Additionally, the checklist results can be used to identify further areas for enhancement, allowing for a systematic approach to continuous improvement.
Engaging Stakeholders for Commitment
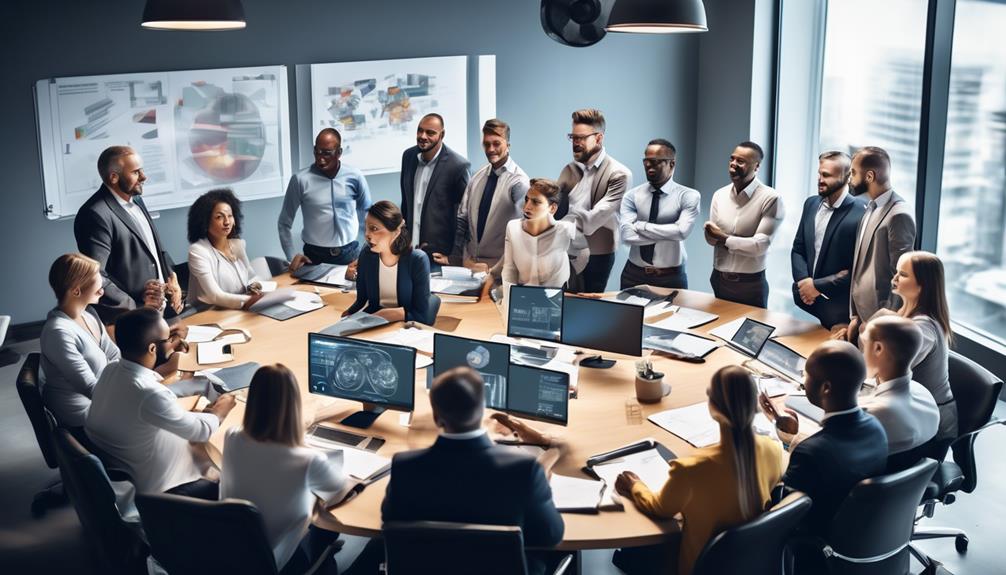
To ensure the successful implementation of ISO 9001 checklist processes, engaging stakeholders for commitment is essential to foster a culture of quality and continuous improvement.
It’s crucial to communicate the checklist with all stakeholders to seek their input for accuracy and usefulness. Involving quality managers, executives, operations, manufacturing, and other team members in the ISO 9001 checklist process maximizes buy-in and commitment to quality management objectives.
To foster a culture of quality and continuous improvement, regular communication and training sessions should be conducted to keep stakeholders informed and motivated.
Ensuring Continuous Quality Improvement
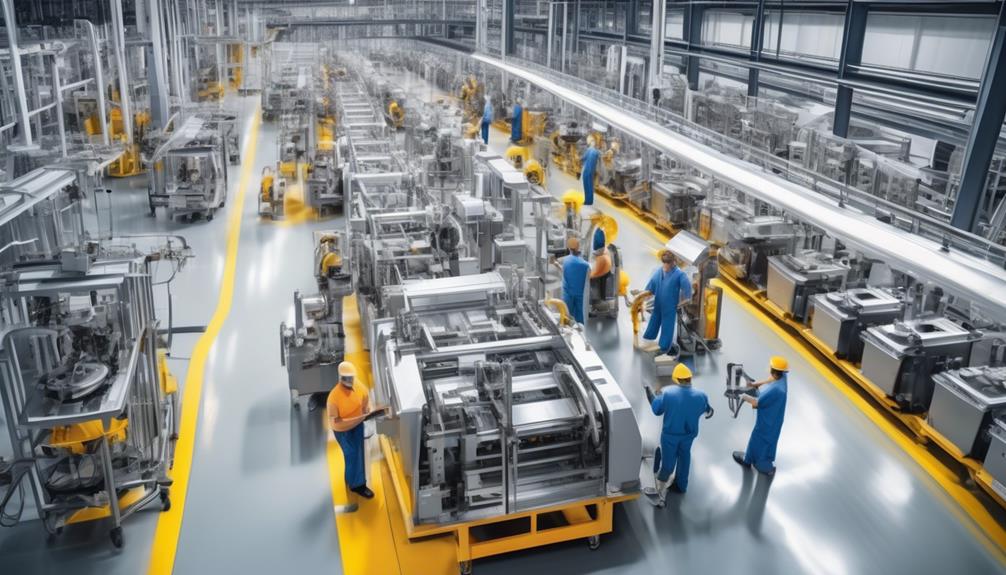
Implementing a robust quality management system (QMS) is essential for driving continuous quality improvement within manufacturing processes. As an ISO 9001 certified company, it’s imperative to prioritize continuous improvement.
Regular review and updating of the ISO 9001 checklist is vital to ensure ongoing compliance and improvement. This involves utilizing the checklist for both internal and external audits, allowing for the identification of areas for enhancement.
Additionally, measuring the performance of the QMS and tracking corrective actions using the ISO 9001 checklist are crucial for ensuring continuous improvement.
It’s essential to engage stakeholders for their buy-in and commitment to foster a culture of quality and continuous improvement. By involving all relevant parties, including employees and management, the organization can work together to achieve its quality objectives and drive continuous improvement throughout the manufacturing processes.
This systematic approach ensures that the company remains proactive in addressing areas for enhancement, ultimately leading to sustained quality improvements.
Frequently Asked Questions
How to Prepare Checklist for ISO 9001?
We prepare an ISO 9001 checklist by thoroughly reviewing each clause of the standard. Then, we create a user-friendly checklist covering all aspects of each clause using appropriate tools like spreadsheets or software.
We regularly conduct internal and external audits using the checklist to ensure compliance and identify areas for improvement. This process enables us to track corrective actions and measure the performance of our quality management system for continuous improvement.
What Are the 6 Mandatory Procedures for ISO 9001?
We ensure compliance by implementing the 6 mandatory ISO 9001 procedures:
- Document control: This procedure manages document creation, approval, and updates.
- Records control: This procedure identifies, stores, and preserves quality records.
- Internal audit: This procedure reviews the quality management system.
- Nonconforming product control: This procedure outlines procedures for handling products not meeting requirements.
- Corrective action: This procedure addresses nonconformities.
- Preventive action: This procedure eliminates potential causes.
What Are the 4 Levels of Documentation for ISO 9001?
We document ISO 9001 requirements at four levels.
Level 1 includes the quality manual and procedures.
Level 2 covers supporting procedures and work instructions.
Level 3 comprises records demonstrating QMS implementation.
Level 4 includes supporting documents and information.
Each level plays a vital role in demonstrating compliance and effective operation.
Understanding these levels helps ensure thorough documentation and effective quality management.
What Are the Essential Requirements of ISO 9001?
We see ISO 9001 as a compass, guiding us toward quality excellence. Essential requirements include customer focus, leadership commitment, risk management, and continuous improvement.
These form the foundation of the standard’s ten clauses, covering crucial aspects of quality management. We meticulously align documentation, policies, processes, and performance metrics with each clause, ensuring comprehensive compliance.
Regular internal and external audits, using our ISO 9001 checklist, help us maintain adherence and uncover areas for enhancement.
Conclusion
Just as a well-tuned machine requires regular maintenance to function at its best, so too does a manufacturing organization need to adhere to ISO 9001 standards to ensure quality and efficiency.
By following this essential checklist, we can ensure that our organization operates like a well-oiled machine, consistently delivering high-quality products and driving success.
Let’s stay committed to continuous improvement and compliance to achieve our goals.
Randy serves as our Software Quality Assurance Expert, bringing to the table a rich tapestry of industry experiences gathered over 15 years with various renowned tech companies. His deep understanding of the intricate aspects and the evolving challenges in SQA is unparalleled. At EarnQA, Randy’s contributions extend well beyond developing courses; he is a mentor to students and a leader of webinars, sharing valuable insights and hands-on experiences that greatly enhance our educational programs.