The typical expense of a data breach for a software company is commonly estimated to be around $3.86 million.
But what can be done to mitigate this risk and protect valuable customer data? Look no further than the 6 key data protection standards that software firms should adhere to.
These standards are crucial for ensuring the security of sensitive information and maintaining compliance with data protection regulations.
But what exactly are these standards, and how can they benefit software firms? Let’s explore the essential data protection standards that every software firm should prioritize.
Key Takeaways
- ISO 27000 Series offers comprehensive information security standards that encompass risk management and security controls, ensuring adherence to data protection standards.
- NIST SP 800-53 provides comprehensive security controls and privacy guidelines that can be customized based on specific needs and risk profiles, enhancing information security and privacy policy.
- The SOC Series issued by AICPA encompasses standards for financial and non-financial reporting controls, focusing on cybersecurity risk management, supply chain, disaster recovery, and business continuity plans.
- GDPR compliance requires measures for consent, data minimization, accuracy checks, storage limitation, integrity, confidentiality, and accountability, ensuring robust security measures for the handling of personal data.
ISO 27000 Series
The ISO 27000 Series offers comprehensive information security standards that are essential for organizations of all types and sizes to establish effective information security measures. These standards, including ISO 27018, ISO 27031, ISO 27037, ISO 27040, and ISO 27799, cover various aspects such as risk management and security controls.
For software firms dealing with personal data, compliance with the ISO 27000 series is crucial. It not only ensures adherence to data protection standards but also demonstrates a commitment to information security management. In today’s regulatory landscape, where stringent regulations such as GDPR govern the handling of personal data, software firms must prioritize compliance with recognized security standards like those in the ISO 27000 series.
Adhering to these standards not only mitigates the risk of data breaches but also enhances customer trust and confidence. By implementing the guidelines outlined in the ISO 27000 series, software firms can establish robust information security measures, ensuring both regulatory compliance and the protection of sensitive data.
NIST SP 800-53
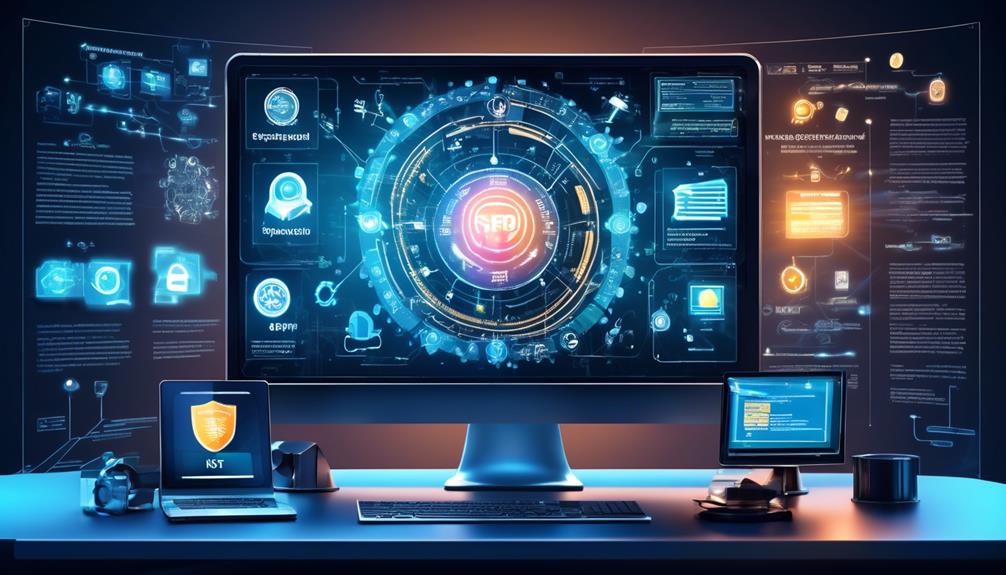
Compliance with the ISO 27000 series lays a strong foundation for information security. Now, exploring NIST SP 800-53’s security controls and privacy guidelines further fortifies our approach to safeguarding sensitive data.
NIST SP 800-53 offers a robust framework for cybersecurity risk management practices and compliance regulations, specifically tailored for software firms. Here’s why it’s crucial for us:
- Comprehensive Security Controls:
NIST SP 800-53 provides a comprehensive set of security controls and safeguards, addressing various aspects of information security such as access control, risk assessment, and incident response. This enables us to establish a strong defense against potential threats to our systems and sensitive data.
- Adaptability and Customization:
The standard’s flexibility allows us to customize security controls based on our specific needs and risk profiles. This adaptability is essential for software firms dealing with diverse types of personal information and needing to adhere to GDPR compliance.
- Widespread Recognition and Applicability:
NIST SP 800-53 is widely recognized and utilized not only in federal agencies but also by private sector organizations. Its widespread applicability makes it a valuable asset for enhancing our information security and privacy policy, ensuring that personal information is adequately protected.
SOC Series
Our software firm has found the SOC Series to be an invaluable resource for ensuring the reliability and security of our systems and the privacy of the data we process.
The SOC Series, issued by the American Institute of Certified Public Accountants (AICPA), encompasses standards for financial reporting, non-financial reporting controls, cybersecurity risk management, and supply chain. It provides a framework that offers a comprehensive approach to security controls for federal and non-federal information systems.
The series focuses on developing and implementing disaster recovery and business continuity plans, which are crucial for ensuring the availability and processing integrity of our systems.
As software developers, the SOC Series has been instrumental in helping us navigate the complex landscape of compliance requirements. It includes the Committee of Sponsoring Organizations’ Control Objectives for Information and Related Technology (COBIT) framework, which assists in aligning our IT governance and control practices.
Additionally, it offers guidance on the General Data Protection Regulation (GDPR) with the ‘Guide to GDPR Compliance Checklist,’ ensuring that our systems are designed to safeguard the privacy of personal data.
GDPR

We need to ensure that our software development processes align with GDPR compliance and data handling requirements.
This means implementing measures for:
- Consent
- Data minimization
- Accuracy checks
- Storage limitation
- Integrity
- Confidentiality
- Accountability.
It’s crucial to understand the liability considerations related to:
- EU citizen use
- Website subscription functions
- Comment sections
- User logins through third-party apps.
GDPR Compliance
As software firms, we prioritize adherence to GDPR, the EU’s data privacy and security law, in order to ensure the protection of personal data collected from individuals in the EU.
GDPR compliance entails several key requirements:
- Explicit Consent: We implement explicit consent mechanisms to ensure that individuals provide clear and unambiguous consent for the processing of their personal data.
- Data Minimization: We adhere to the standards of data minimization, ensuring that we only collect and process the personal data that’s absolutely necessary for the specified purpose.
- Confidentiality Measures: We implement robust security measures to ensure the confidentiality and integrity of the personal data we handle, in line with GDPR’s requirements.
Data Handling Requirements
In complying with GDPR data handling requirements, software firms must ensure that personal and sensitive information is processed lawfully, fairly, and transparently, with explicit consent and user control over their data. This entails adhering to specific privacy controls dictated by the General Data Protection Regulation, as well as other data protection laws.
It involves implementing secure security standards and regulations, such as those outlined in security frameworks and security requirements for protecting personal and sensitive data. Software firms catering to financial services businesses must also ensure compliance with additional regulations, such as PCI DSS, in order to meet the stringent data handling requirements.
HITRUST Common Security Framework
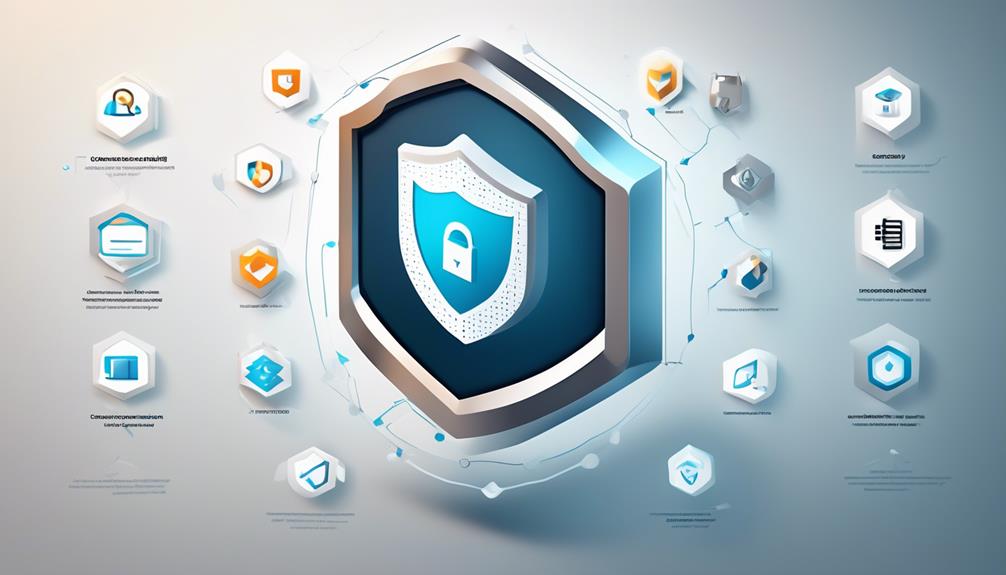
The HITRUST Common Security Framework (CSF) provides a comprehensive set of security controls and privacy principles tailored to address the specific regulatory and security challenges within the healthcare industry.
This framework offers a risk-based approach to managing security and privacy-related risks, harmonizing the requirements of multiple standards and regulations. Its robust assessment framework enables organizations to demonstrate compliance with various industry regulations, such as HIPAA, HITECH, and GDPR, through a single assessment process.
Additionally, HITRUST CSF includes various control categories like access control, risk management, and incident management, ensuring comprehensive protection of sensitive data.
Compliance with HITRUST CSF is increasingly becoming a requirement for healthcare organizations, as it offers a standardized and certifiable approach to information security and privacy management, instilling trust in stakeholders.
Embracing the HITRUST CSF not only ensures compliance with industry standards but also demonstrates a commitment to cybersecurity best practices, particularly in safeguarding protected health information and implementing robust security measures to mitigate risks and enhance overall data security and compliance.
COBIT
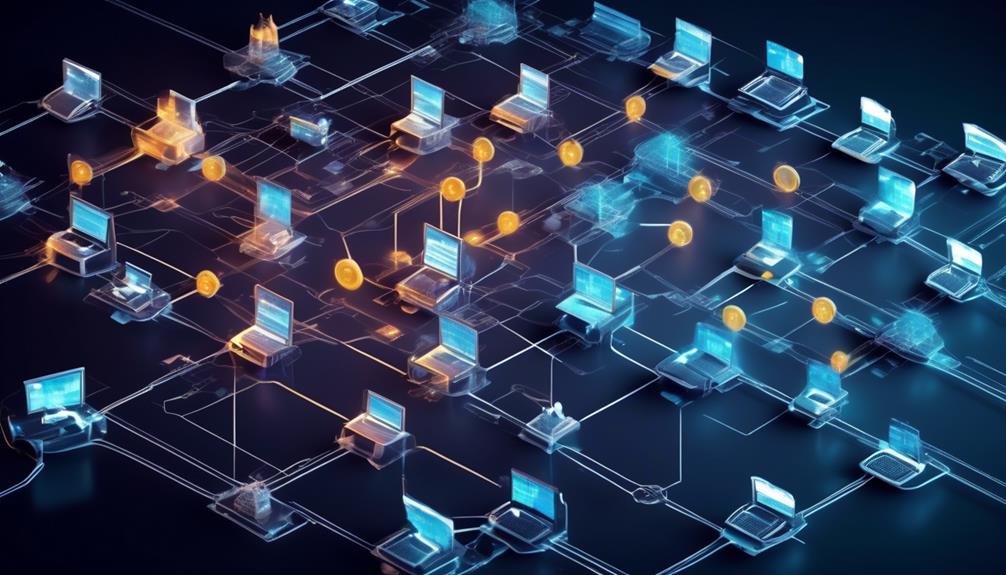
We’ve reached the point in our discussion where we need to address the COBIT framework and its compliance requirements.
COBIT, which stands for Control Objectives for Information and Related Technologies, offers comprehensive guidelines for IT governance and management. It’s essential for software firms to understand and implement these standards to ensure alignment with business goals and the effective management of risks.
COBIT Framework
Regularly updated to reflect evolving best practices in IT governance and management, the COBIT Framework (COBIT) provides a comprehensive set of principles and tools to align IT with business goals and ensure effective governance and management of enterprise IT.
When considering data protection standards for software firms, the COBIT framework plays a crucial role in promoting information security and cybersecurity best practices. Specifically, it assists software firms in securing their information systems by offering guidance on incident response, aligning with NIST SP 800-61 for incident handling, and ensuring compliance with data protection regulations such as those concerning EU citizens.
Moreover, COBIT aids in enhancing application security, thereby fortifying software firms’ defenses against potential cyber threats and vulnerabilities.
Compliance Requirements
When assessing compliance requirements within the COBIT framework, we prioritize aligning our IT systems with regulatory standards to ensure effective governance and management of enterprise IT. Adhering to COBIT compliance requirements is crucial for software firms, especially when handling sensitive data.
It helps establish control objectives and best practices for IT processes, risk management, and regulatory compliance. By implementing effective security measures and monitoring compliance, software firms can ensure information security and build trust with customers.
Moreover, compliance with frameworks and security standards, such as PCI DSS, is essential, particularly for software firms serving financial services companies. Meeting these compliance requirements not only safeguards data but also mitigates legal consequences, demonstrating a commitment to security compliance.
Frequently Asked Questions
What Are the SecurITy Standards in IT Industry?
We follow robust security standards in the IT industry. ISO, NIST, and PCI DSS are crucial. Compliance with GDPR and CCPA is essential for handling personal data.
Data security is vital for protecting customer information and maintaining trust. When selecting security standards, we consider location, industry-specific laws, and business nature.
ISO 27000 Series, NIST SP 1800 Series, and PCI DSS are important standards. These measures ensure data protection and build customer confidence.
What Are the 7 GDPR Requirements?
We’ve found that the 7 GDPR requirements are crucial for compliance. They include:
- Obtaining consent for data processing
- Informing individuals about their data rights
- Implementing measures to protect personal data
This ensures a solid foundation for data security and privacy. It’s like building a sturdy fortress around sensitive information, safeguarding it from potential threats.
Understanding and adhering to these requirements is vital for any organization handling personal data.
What Is GDPR in Software?
GDPR in software refers to compliance with the EU’s data privacy and security law for organizations collecting data from individuals in the EU.
It requires software firms to adhere to principles of lawful, fair, and transparent data processing, ensuring minimal data collection, accuracy, and purpose limitations.
Emphasizing integrity and confidentiality, GDPR mandates security measures, encryption, and access controls.
Additionally, accountability is crucial, requiring documentation of data processing activities and compliance demonstration.
What Are the Data Protection Standards?
Data protection standards are essential for safeguarding sensitive information from unauthorized access or disclosure. They include ISO, NIST, and PCI DSS, crucial for complying with regulations like GDPR and CCPA.
Compliance maintains trust and avoids fines. When choosing standards, organizations consider industry-specific laws and their risk profile.
Key standards like ISO 27000 Series and NIST SP 1800 Series are vital for maintaining trust with clients and investors.
Conclusion
In conclusion, implementing these 6 key data protection standards for software firms is crucial for ensuring the secure handling of sensitive information. It is also important for protecting against data breaches and maintaining legal compliance.
Compliance with these standards builds customer trust and safeguards the reputation of software firms. By adhering to these standards, software firms can demonstrate their commitment to protecting customer data and maintaining a high level of security.
Therefore, it is essential for software firms to stay secure, stay compliant, and stay ahead with these key data protection standards!
Randy serves as our Software Quality Assurance Expert, bringing to the table a rich tapestry of industry experiences gathered over 15 years with various renowned tech companies. His deep understanding of the intricate aspects and the evolving challenges in SQA is unparalleled. At EarnQA, Randy’s contributions extend well beyond developing courses; he is a mentor to students and a leader of webinars, sharing valuable insights and hands-on experiences that greatly enhance our educational programs.