As we start the ISO Certification process for Quality Control, we face the challenge of setting specific objectives and defining the scope of our Quality Management System (QMS).
The road ahead requires a strategic approach to ensure compliance with ISO 9001 standards, from establishing quality policies and documenting procedures to effectively implementing and communicating the QMS to all employees.
However, the real test lies in the successful completion of internal and external audits, which will determine our organization's ability to obtain and sustain the coveted ISO 9001 certification.
Key Takeaways
- ISO Certification is a globally recognized standard that demonstrates an organization's commitment to quality, efficiency, and continuous improvement.
- Understanding ISO 9001 and 27001 standards is crucial for identifying quality control requirements.
- Establishing clear, measurable quality control objectives aligned with ISO certification requirements and industry regulations is essential.
- Documenting quality control processes, conducting regular internal audits, and preparing for the certification audit are necessary steps in achieving ISO certification.
Understanding ISO Certification
Understanding ISO Certification involves comprehending the globally recognized standard that demonstrates an organization's commitment to quality, efficiency, and continuous improvement. ISO, which stands for the International Organization for Standardization, sets forth rigorous criteria for organizations to follow in order to achieve certification. This process involves a thorough evaluation of the organization's quality management system to ensure that it meets the stringent requirements of the ISO standards. Quality lies at the core of ISO certification, emphasizing the importance of consistently delivering products and services that meet customer and regulatory requirements.
The certification journey demands a meticulous approach, requiring organizations to establish and maintain processes that prioritize quality and efficiency. Achieving ISO certification isn't merely about obtaining a badge of honor; it's about instilling a culture of continual improvement and adherence to global best practices. This commitment to quality not only enhances the organization's reputation but also fosters customer satisfaction and trust.
Identifying Quality Control Requirements
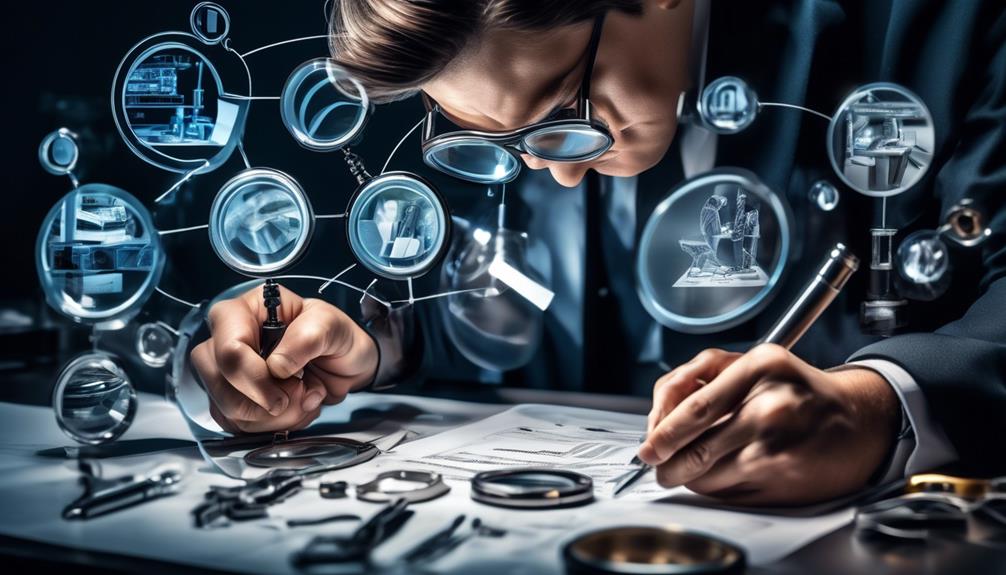
Identifying quality control requirements involves meticulously documenting the specific criteria and standards that align with ISO guidelines and industry regulations. Understanding ISO 9001 and 27001 standards is crucial for this process, as these form the foundation for quality control requirements within the ISO certification framework. Aligning quality control requirements with ISO standards and the organization's industry-specific regulations is paramount to ensure compliance and adherence to best practices.
To identify these requirements, a comprehensive analysis of internal processes, documentation, and existing quality management systems is necessary. This involves scrutinizing the organization's operations to ensure that all aspects align with the quality audit standards set by the ISO certification.
It's also crucial to involve relevant personnel and stakeholders in the identification and assessment of quality control requirements, as their insights and expertise are invaluable in ensuring that all relevant aspects are considered.
Establishing Quality Control Objectives
In aligning with ISO guidelines and industry regulations, our next focus turns to establishing clear and measurable quality control objectives that are intricately tied to the organization's overall goals and customer expectations. When establishing quality control objectives, it's crucial to ensure that they're in line with ISO certification requirements and Quality Management Systems. These objectives should reflect a commitment to continuous improvement, as this is a fundamental aspect of maintaining high-quality standards.
It's also essential to consider compliance with industry regulations and standards, ensuring that the quality control objectives aren't only aligned with ISO requirements but also with any other relevant regulatory frameworks.
To achieve this, effective communication of these objectives across the organization is paramount. This ensures that all stakeholders are aware of the quality control objectives and understand their significance in relation to the organization's overarching goals and customer satisfaction.
Selecting ISO Certification Approach
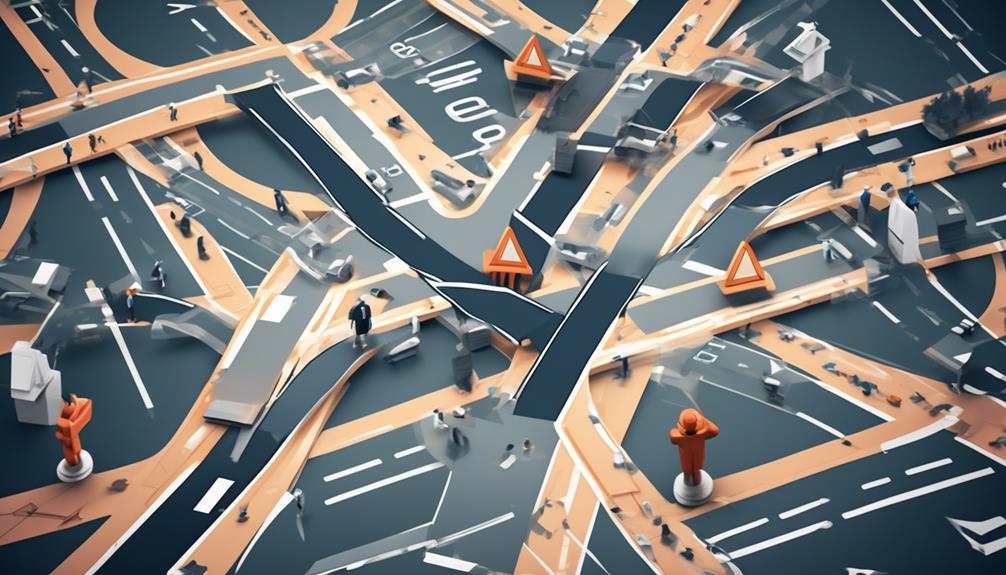
In assessing our organization's needs and aligning with our specific quality objectives, we meticulously evaluate the costs, current conformance levels, and resource requirements when selecting an ISO certification approach. It is crucial to consider the specific goals and benefits sought from ISO certification, as well as the costs of registration, audits, and implementation. Additionally, assessing the current level of conformance with ISO 9001 requirements is essential to understand the gap and necessary steps for compliance. Determining the resources and support needed for development and implementation of the chosen ISO certification approach is also a critical aspect of the decision-making process. Furthermore, choosing an implementation approach that aligns with the company's infrastructure and organizational culture is imperative for a successful ISO certification journey.
Considerations | Importance |
---|---|
Specific Goals | High |
Costs | High |
Conformance Levels | High |
Resources | High |
Implementation Approach | High |
Considering these factors will ensure that the selected ISO certification approach effectively supports our quality control journey.
Documenting Quality Control Processes
Upon embarking on the journey to document our quality control processes, we meticulously outline the procedures, policies, and key processes essential for initiating the ISO certification process. This involves a step-by-step approach focusing on the following:
- Identification of Key Processes: We identify and document the key processes within our organization that directly impact the quality of our products or services, as guided by ISO 9001 clauses.
- Development of Quality Manuals: We develop comprehensive quality manuals that outline the quality objectives, policies, and procedures to ensure compliance with ISO 9001 standards.
- Training Employees: Implementation involves training our employees on their roles and responsibilities as per the documented Quality Management System (QMS) in line with ISO 9001 standards.
- Internal Audits: We conduct regular internal audits to assess the conformity of the implemented QMS and identify areas for improvement, aligning with ISO 9001 clauses.
Through meticulous documentation of our quality control processes, we aim to establish a robust Quality Management System (QMS) that not only meets the rigorous standards of ISO certification but also enhances the overall quality of our products and services.
Implementing ISO Standards
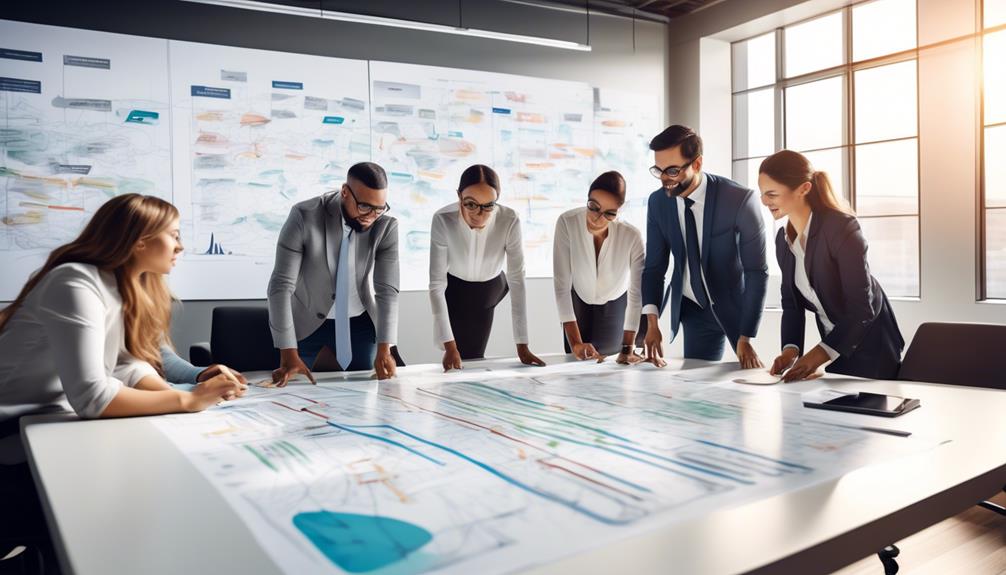
We will systematically implement ISO standards across our organization, ensuring meticulous adherence to the prescribed processes and requirements for certification.
Management commitment is essential for the successful implementation of ISO standards.
The first step involves establishing a clear understanding of the ISO requirements and integrating them into our Quality Management System (QMS). This may entail restructuring existing processes and procedures to align with the ISO standards.
We'll designate responsible individuals or teams to oversee the implementation process, ensuring that all relevant employees are trained on the new requirements.
Additionally, it's crucial to conduct internal audits to assess the effectiveness of the implemented ISO standards and identify areas for improvement.
Throughout the implementation phase, documentation plays a key role, as it provides evidence of conformity to the ISO standards.
Regular management reviews will be conducted to monitor progress and address any challenges encountered during the implementation.
Conducting Internal Quality Audits
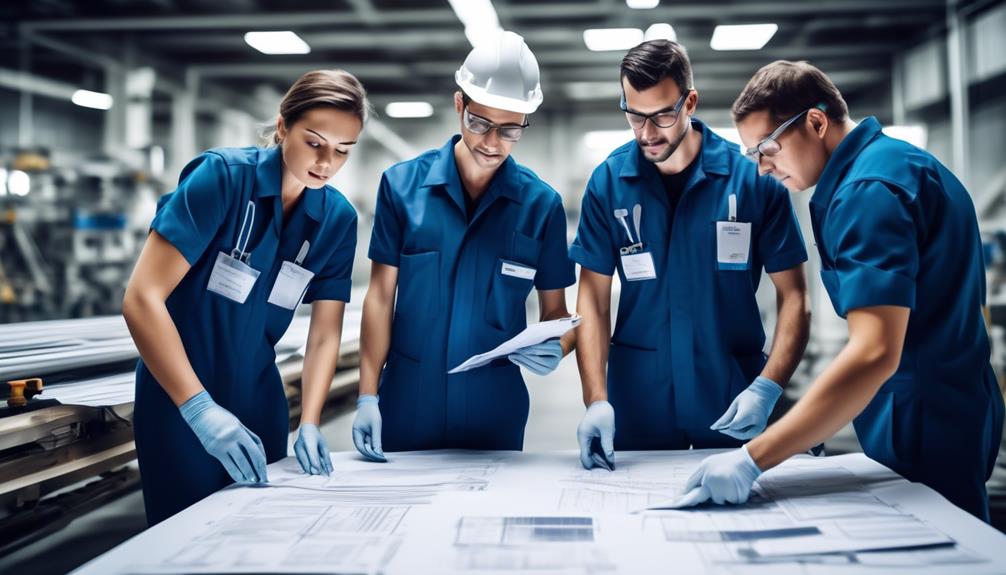
Our organization meticulously conducts internal quality audits to assess the conformity of our Quality Management System (QMS) and identify areas for improvement. This process is integral to our ISO certification and quality control journey, ensuring that we adhere to the ISO 9001 standards.
Here are four key aspects of our internal quality audits:
- Evaluation of Effectiveness: We use internal audits to evaluate the effectiveness of our processes and ensure that they align with our documented procedures. This helps us maintain consistency and excellence in our operations.
- Adherence to ISO Requirements: We schedule and carry out internal audits at planned intervals as per the requirements of ISO 9001. This structured approach ensures that we're continuously monitoring and improving our QMS.
- Identification of Nonconformities: Internal audits are crucial for identifying nonconformities and areas that require corrective action. This proactive approach helps us address issues before they impact our products or services.
- Preparation for External Certification Audit: By conducting internal audits, we prepare our organization for the external certification audit. This ensures that we're fully compliant with ISO 9001 standards, leading to a smoother certification process.
Through these internal quality audits, we constantly strive to enhance our QMS, ultimately leading to improved overall performance and customer satisfaction.
Preparing for Certification Audit
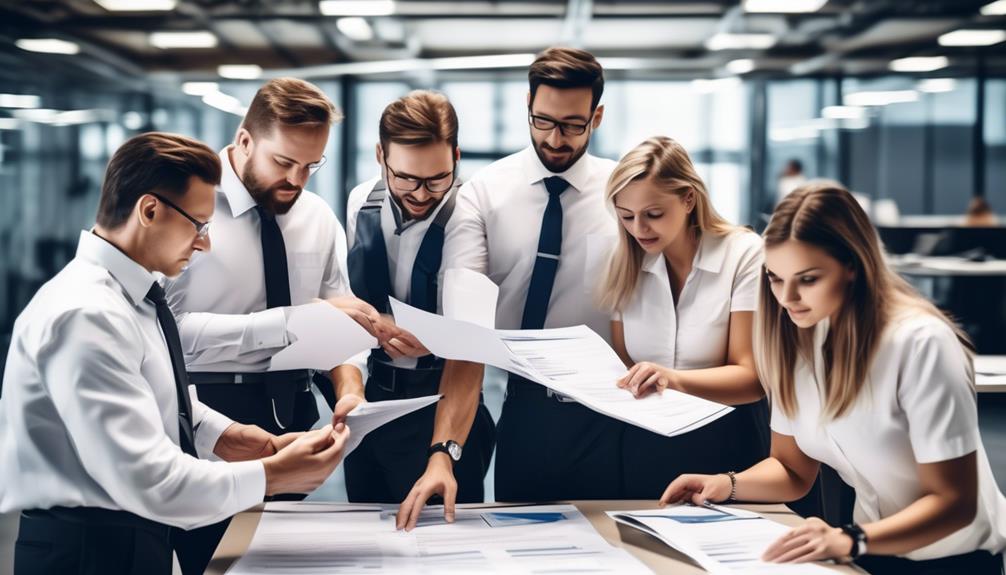
As we progress in our ISO certification and quality control journey, the meticulous preparation for the certification audit becomes a critical focus, ensuring that our Quality Management System (QMS) is thoroughly assessed and aligned with ISO 9001 standards. The certification process involves comprehensive documentation of processes, policies, and procedures related to quality management, followed by effective communication of these QMS policies and procedures to relevant personnel. Employee training on their roles, responsibilities, and QMS requirements is essential to ensure readiness for the audit. Additionally, conducting internal audits to assess conformity of the implemented QMS and identify areas for improvement is integral to the preparation process. We also need to coordinate with a reputable certification body accredited for ISO audits and schedule the certification audit. The table below outlines the key steps in preparing for the certification audit.
Preparation Steps for Certification Audit |
---|
Document processes, policies, and procedures related to quality management |
Communicate QMS policies and procedures to relevant personnel and provide training |
Conduct internal audits to assess conformity of the implemented QMS and identify areas for improvement |
Coordinate with a reputable certification body accredited for ISO audits and schedule the certification audit |
Engaging With ISO Registrar
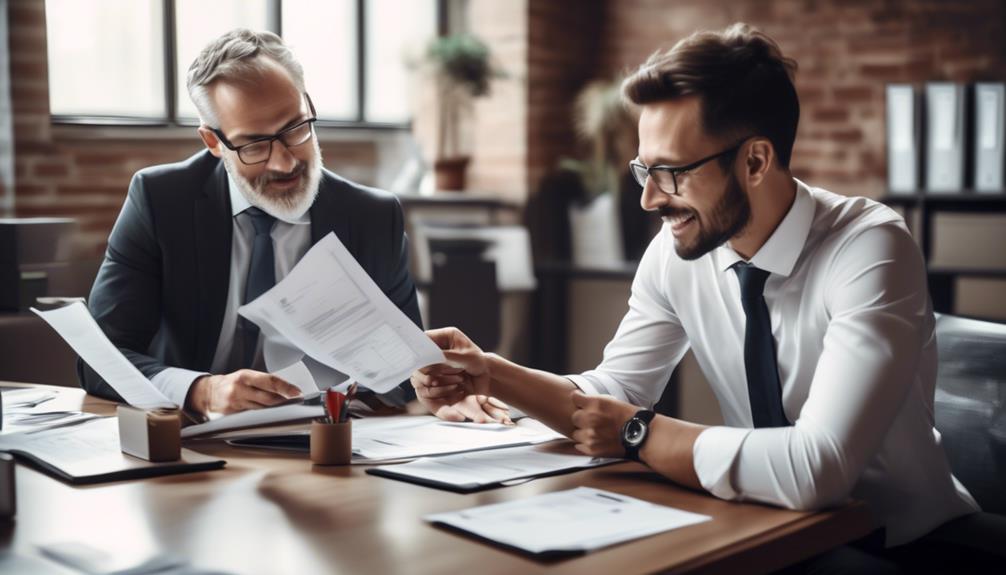
Upon initiating the process of engaging with an ISO registrar, meticulous research and selection of a reputable provider with accredited certification services is essential. This step sets the foundation for a successful partnership in the ISO certification journey.
Here's how we can effectively engage with an ISO registrar:
- Thorough Research: We need to invest time in researching and evaluating various ISO registrars. It's crucial to consider their accreditation, experience, industry expertise, and reputation within the quality control community.
- Collaborative Approach: Once we've selected an ISO registrar, close collaboration is key. We should engage in open dialogue to comprehend the certification process, standards, and specific requirements for our organization.
- Preparation for Audit: A meticulous preparation for the registrar's certification audit is vital. This involves ensuring that our quality management systems align with ISO standards and that all necessary documentation is in place.
- Continuous Communication and Improvement: Throughout the certification journey, maintaining transparent communication with the registrar is essential. We should leverage their expertise and feedback to continually enhance our quality control processes.
Engaging with an ISO registrar is a pivotal phase in the ISO certification process, and by following these steps, we can establish a productive and beneficial relationship with the registrar to achieve our quality control objectives.
Achieving ISO Certification
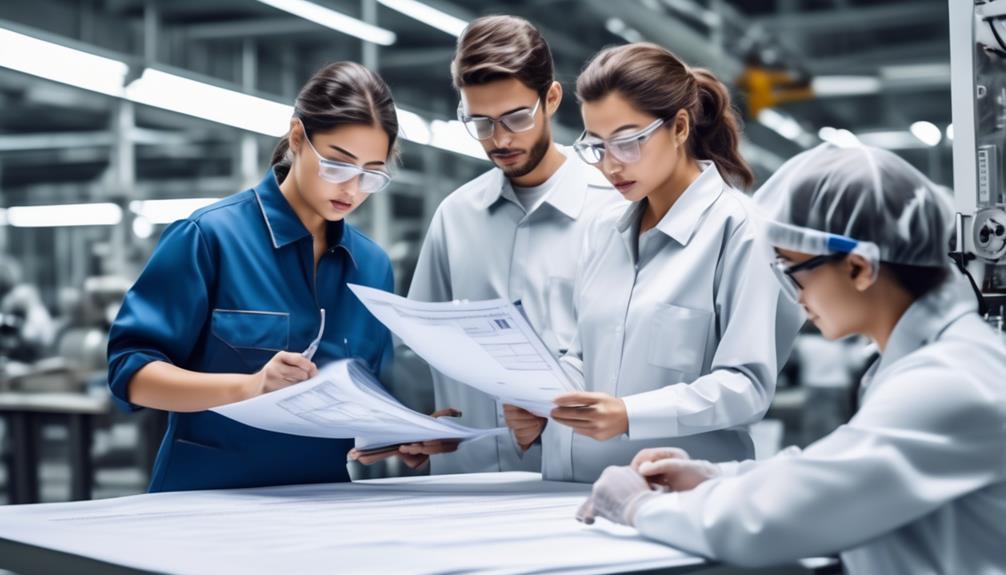
After engaging with an ISO registrar and laying the groundwork for our certification journey, the process of achieving ISO certification requires a comprehensive understanding of the systematic and well-planned processes involved. We must meticulously document our quality management system, ensuring that it aligns with the ISO standards. This involves creating and implementing quality control procedures, conducting internal audits, and addressing any non-conformities.
Additionally, we need to establish clear objectives and measurable targets to demonstrate our commitment to continuous improvement.
Achieving ISO certification also demands effective training and communication throughout the organization to ensure that all employees understand their roles in maintaining quality standards. It's crucial to engage employees at all levels, fostering a culture of quality consciousness and accountability.
Moreover, we must be prepared for a thorough external audit by the registrar to validate our compliance with ISO requirements.
Successfully navigating the ISO and achieving ISO certification won't only enhance our credibility in the market but also drive operational excellence. It's a testament to our commitment to delivering superior products and services while continuously improving our internal processes.
Continuous Quality Improvement
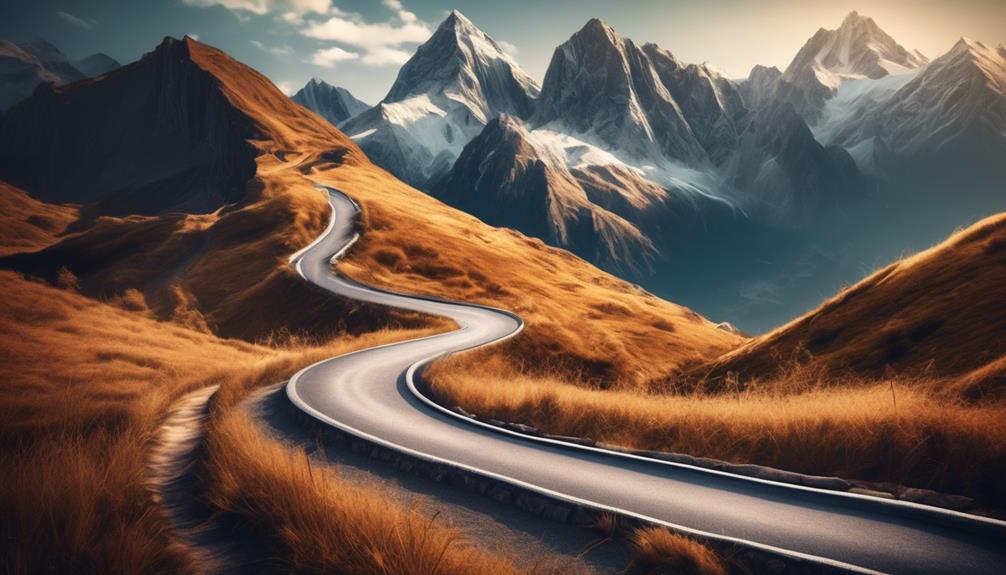
We'll now explore the essential points relating to continuous quality improvement.
We'll analyze process optimization techniques to refine and streamline our operations.
We'll also discuss quality management tools that facilitate effective quality control.
We'll discuss performance monitoring strategies to ensure consistent high standards.
Process Optimization Techniques
Process optimization techniques, such as Lean Six Sigma, Total Quality Management (TQM), and Kaizen, are integral to achieving continuous quality improvement by enhancing the efficiency and effectiveness of organizational processes. These techniques empower organizations to adapt to changing market demands, reduce costs, and deliver higher quality products and services, aligning with the rigorous standards of an ISO 9001 certification.
To navigate the ISO 9001 certificate journey towards a commitment to quality, here are some key process optimization techniques:
- Lean Six Sigma: A data-driven approach focusing on reducing defects and variation.
- Total Quality Management (TQM): An organization-wide strategy to continuously improve the quality of products and processes.
- Kaizen: Involves making small, incremental improvements to processes over time.
- Continuous Analysis: Regularly analyzing processes, collecting data, and making incremental changes to drive improvement.
Quality Management Tools
Quality management tools play a crucial role in facilitating continuous quality improvement within organizations. They aid in the identification, analysis, and resolution of quality-related issues in processes and products. These tools include Six Sigma, Lean Manufacturing, Total Quality Management (TQM), and Statistical Process Control (SPC).
These tools are essential for organizations striving to become ISO certified and maintain a culture of continuous improvement. By incorporating these tools, businesses can enhance efficiency, reduce waste, and improve customer satisfaction.
The application of quality management tools also leads to better decision-making and overall business performance. They are instrumental in preparing for quality audits and ensuring that the organization's processes and products meet the required quality standards.
Incorporating these tools into the organization's quality management system is crucial for achieving and sustaining excellence.
Performance Monitoring Strategies
Monitoring and evaluating the performance of processes, systems, and outcomes is a critical component of achieving continuous quality improvement within an organization's ISO certification journey.
To effectively implement performance monitoring strategies, we need to:
- Establish Clear Objectives: Clearly define the key performance indicators (KPIs) that align with the organization's quality objectives and ISO standards.
- Utilize Data-Driven Methods: Implement data collection and analysis methods to measure and track performance against established benchmarks.
- Regular Assessment: Conduct regular and systematic assessments to identify areas for improvement and ensure adherence to quality control standards.
- Foster a Culture of Continuous Improvement: Encourage a culture of ongoing learning, adaptation, and enhancement within the organization to drive continuous quality improvement.
Implementing these strategies won't only ensure compliance with ISO standards but also drive performance and quality improvements across the organization.
Ensuring Compliance With ISO Standards
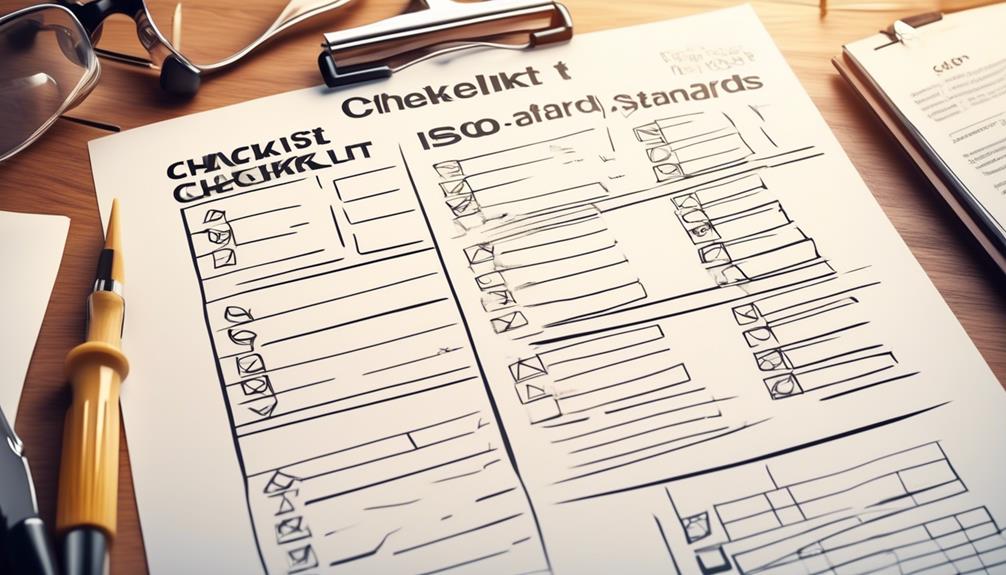
Ensuring Compliance With ISO Standards
Demonstrating commitment to quality, efficiency, and continuous improvement, ensuring compliance with ISO standards is a fundamental aspect of our quality control journey. Adhering to ISO standards not only enhances credibility, performance, and competitiveness in the global market but also ensures the quality, safety, and efficiency of our products, services, and systems. Compliance with ISO 9001 and 27001 standards serves as cornerstones of trust, ensuring consistent quality, information asset protection, and customer satisfaction in various industries.
To illustrate the meticulous approach required for compliance, we have provided a table below outlining the key steps involved in achieving and maintaining ISO certification. This table encapsulates the essential components of the compliance process, including documentation, implementation, internal audits, and external certification audits.
Key Steps for ISO Compliance | Description |
---|---|
Documentation | Meticulous recording of processes and procedures |
Implementation | Integration of ISO standards into daily operations |
Internal Audits | Regular self-assessment of adherence to ISO standards |
External Audits | Independent evaluation by ISO certification bodies |
Adhering to ISO standards not only fosters customer satisfaction and trust but also underscores our commitment to quality certification, continual improvement, and excellence.
Integrating Quality Control Systems
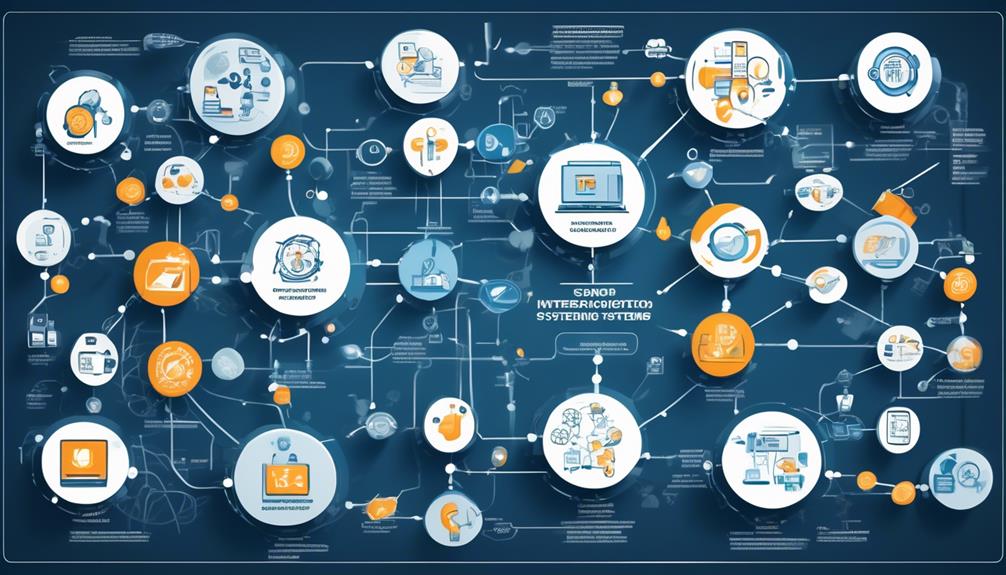
Throughout the integration process of Quality Control Systems, meticulous documentation and alignment of processes and procedures with ISO standards are essential. This ensures that the organization's quality management objectives and procedures are articulated clearly and consistently.
In order to integrate Quality Control Systems effectively, the following steps should be considered:
- Application of ISO Standards: Apply ISO standards to internal processes and workflows to ensure that they're in line with the requirements set forth by the quality certification body.
- Training and Communication: Implementing Quality Control Systems involves training staff at all levels and ensuring that upper management effectively disseminates information about the integration process and its importance.
- Establishing Repeatable Frameworks: It's essential to establish repeatable frameworks for all operations based on ISO principles. This involves creating standardized processes that align with the audit standards and frameworks set by ISO.
- Continuous Improvement: Integrate a culture of continuous improvement into the systems by regularly reviewing and updating processes to maintain alignment with ISO standards and to ensure the ongoing effectiveness of the Quality Control Systems.
Integrating Quality Control Systems is a meticulous and detail-oriented process that requires a thorough understanding of ISO standards and a commitment to aligning all processes and procedures with these standards.
Monitoring Quality Control Performance
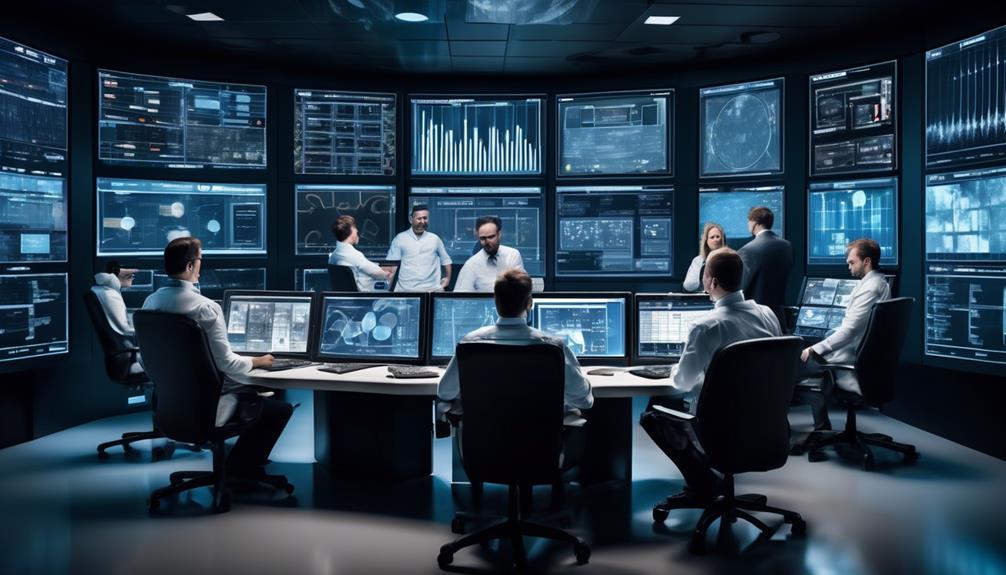
As we examine the topic of monitoring quality control performance, it's crucial to consider the specific metrics for evaluating QC performance. These metrics provide a clear understanding of the effectiveness of our quality control measures and highlight areas for improvement.
Additionally, continuous improvement strategies and employee training and development play a pivotal role in enhancing QC performance.
Metrics for QC Performance
We utilize metrics for Quality Control (QC) performance to effectively evaluate the consistency and accuracy of our QC activities, enabling us to monitor and improve our quality control processes.
- Key performance indicators (KPIs) are used to measure various aspects of quality control, such as defect rates and process efficiency.
- Establishing benchmarks and targets for QC metrics aids in setting and achieving quality improvement goals.
- Tracking metrics for QC performance enables identification of trends and areas for improvement.
- These metrics help in monitoring the consistency and accuracy of QC activities.
Implementing these metrics is crucial in our quest for ISO certification, as they provide the necessary data to make informed decisions and drive continuous improvement in our quality control processes.
Continuous Improvement Strategies
To effectively monitor and enhance quality control performance, we implement key performance indicators (KPIs) that measure and track various aspects of our quality control processes over time. Regular review and analysis of quality control data allow us to identify trends, patterns, and areas for improvement.
Additionally, periodic quality control audits are conducted to assess adherence to ISO standards and to identify opportunities for enhancement. We actively encourage feedback from stakeholders and employees to continuously identify areas for improvement in our quality control processes.
Furthermore, we utilize lean and Six Sigma methodologies to streamline our quality control processes, minimizing waste while maximizing efficiency. Through these continuous improvement strategies, we aim to maintain ISO certification standards and ensure the highest level of quality control in all our operations.
Employee Training and Development
Monitoring quality control performance involves not only assessing adherence to ISO standards and identifying areas for improvement but also ensuring that employee training and development initiatives effectively enhance product and service quality.
To effectively monitor quality control performance through employee training and development, we should:
- Conduct regular assessments of employees' understanding and implementation of quality control processes and procedures.
- Organize frequent training sessions and workshops to keep employees updated with the latest quality control standards and techniques.
- Evaluate the effectiveness of employee training programs in enhancing product and service quality.
- Focus on fostering a quality-oriented mindset and a commitment to continuous improvement through employee development initiatives.
Sustaining ISO Certification Achievements
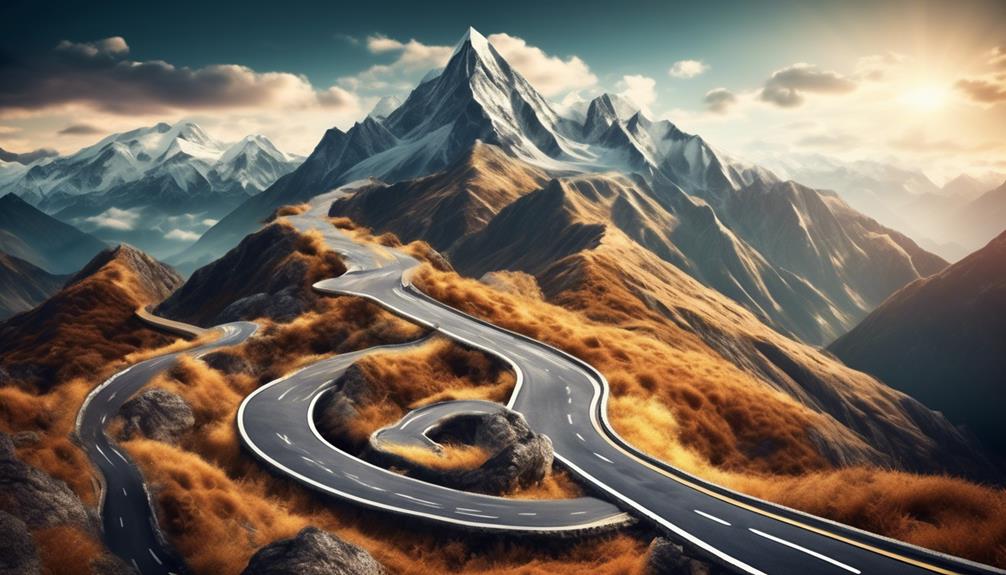
Sustaining ISO certification achievements necessitates a steadfast dedication to quality, compliance, and continuous improvement. To maintain successful completion of ISO standards, regular internal audits and nonconformity identification are imperative. Adhering to ISO 9001 and 27001 standards shouldn't be considered a one-time accomplishment, but rather an ongoing commitment embedded in the organization's culture.
Continuous training and retraining of employees on their roles and responsibilities within the Quality Management System (QMS) is essential for sustaining ISO certification. It's crucial to establish a dedicated Quality & Compliance Group function to oversee the implementation and adherence to the quality policy. This group can facilitate the continuous improvement process and ensure that customer satisfaction is at the forefront of all quality control efforts.
Frequently Asked Questions
What Are the 5 Steps to ISO Certification?
We initiate the ISO certification process by documenting processes, policies, and procedures.
Then, we implement and train our team on the Quality Management System (QMS) throughout the organization.
Next, we conduct internal audits to assess conformity and identify areas for improvement.
An external certification body conducts a thorough audit, and upon successful completion, issues an ISO 9001 certificate.
What Is the Path to ISO Certification?
The path to ISO certification involves a detailed process of documenting, implementing, and auditing quality management systems. It's a journey that demands dedication and precision.
Did you know that 1.1 million ISO 9001 certificates were issued worldwide in 2020? This highlights the global significance of ISO certification.
From meticulous documentation to training, the path to ISO certification requires a thorough understanding of quality control principles and a commitment to continuous improvement.
How Do I Approach ISO Certification?
We approach ISO certification by meticulously documenting processes, implementing a Quality Management System (QMS), conducting internal audits, and undergoing a certification audit.
Our commitment to quality, efficiency, and continuous improvement is demonstrated through a systematic and well-planned approach.
ISO certification significantly enhances our credibility, performance, and fosters customer satisfaction, providing a competitive advantage in the global market.
Our expertise in ISO standards, including having certified ISO Lead Auditors, guides us towards ISO certification and continuous improvement of QMS.
What Is ISO in Quality Control?
ISO in quality control is like a compass guiding us toward excellence. It's a set of international standards ensuring products and services meet regulatory requirements and customer satisfaction.
We implement ISO to improve processes, reduce errors, and enhance overall efficiency. ISO emphasizes a systematic approach to quality management, covering areas such as documentation, process control, and continuous improvement.
It's a crucial tool for ensuring consistent and reliable quality in our operations.
Conclusion
In conclusion, successfully navigating the ISO certification quality control journey requires:
- A thorough understanding of the standards
- Clear objectives
- Diligent documentation and compliance
Integrating quality control systems, monitoring performance, and sustaining achievements are essential for long-term success.
Just like a well-planned road trip:
- Attention to detail
- Careful navigation
These elements will ensure a smooth and successful journey towards ISO certification.
Randy serves as our Software Quality Assurance Expert, bringing to the table a rich tapestry of industry experiences gathered over 15 years with various renowned tech companies. His deep understanding of the intricate aspects and the evolving challenges in SQA is unparalleled. At EarnQA, Randy’s contributions extend well beyond developing courses; he is a mentor to students and a leader of webinars, sharing valuable insights and hands-on experiences that greatly enhance our educational programs.