Businesses frequently face a difficult decision as they work towards maintaining high standards: striving for excellence while also balancing expenses and productivity.
In such a dynamic environment, it becomes imperative to employ the best quality control management techniques to ensure that products and processes meet or exceed customer expectations.
The three techniques we will discuss have been proven to be effective in achieving this delicate balance, offering a blend of precision, reliability, and practicality.
So, what are these techniques, and how can they benefit your organization?
Key Takeaways
- Statistical Process Control (SPC) is a technique that utilizes statistical techniques to ensure consistent quality in processes and products, emphasizing early detection and prevention of issues.
- Failure Modes and Effects Analysis (FMEA) is a proactive technique that systematically analyzes potential failure modes, their causes, and effects, prioritizing them based on severity, occurrence, and detection to improve product reliability, safety, and performance.
- Root Cause Analysis (RCA) is a systematic technique that aims to identify underlying reasons for problems or incidents, addressing the fundamental cause rather than just the symptoms, enhancing customer satisfaction and enabling continuous process refinement.
- Implementing quality control management techniques such as SPC, FMEA, and RCA can help maintain high quality standards, improve overall process control methods, proactively identify and mitigate risks and failures, and ultimately enhance customer satisfaction and loyalty.
Statistical Process Control (SPC)
Utilizing statistical techniques, Statistical Process Control (SPC) aims to ensure consistent quality in processes and products, emphasizing early detection and prevention of issues. SPC plays a pivotal role in quality management by enabling organizations to monitor and control the production process effectively. This involves the selection of relevant Key Performance Indicators (KPIs) and critical quality characteristics to drive continuous improvement. SPC emphasizes the use of statistical tools and methods to monitor variation, identify trends, and make data-driven decisions for process improvement.
One of the key aspects of SPC is the establishment of control limits and the utilization of control charts to distinguish between common cause variation and special cause variation in processes. This allows management to take proactive measures in response to variations, ensuring that the quality of products and processes is consistently maintained. By integrating SPC into the Quality Management System (QMS), organizations can effectively reduce variability in production, leading to improved quality control and overall operational excellence.
SPC is instrumental in not only maintaining quality standards but also driving improvements in the overall process control methods.
Failure Modes and Effects Analysis (FMEA)
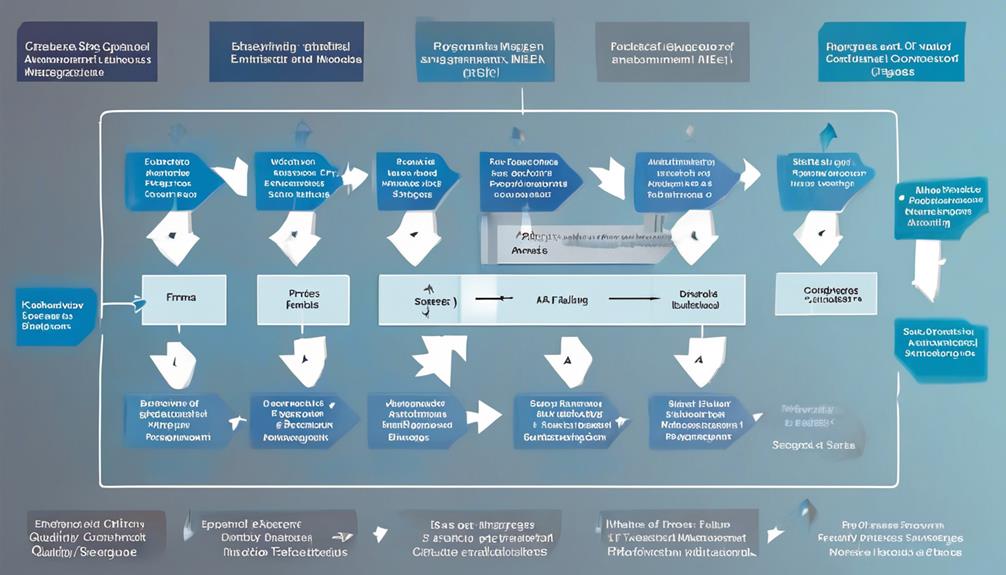
While Statistical Process Control (SPC) focuses on ensuring consistent quality in processes and products through the use of statistical techniques, Failure Modes and Effects Analysis (FMEA) proactively identifies and mitigates potential failure modes in a product or process before they occur. FMEA involves systematically analyzing potential failure modes, their causes, and the effects of these failures to prioritize and address potential risks. This technique utilizes FMEA ratings to prioritize failure modes based on severity, occurrence, and detection, helping to focus resources on the most critical areas. By applying FMEA across various industries, including manufacturing, healthcare, and automotive, organizations can improve product reliability, safety, and performance. FMEA is an essential tool in risk management, aiding in the development of effective preventive and corrective actions to minimize the impact of potential failures. Below is a table illustrating the FMEA ratings and their significance in identifying and addressing failure modes:
Rating | Significance |
---|---|
Severity | Measures the impact of a potential failure on the customer, production, or regulatory compliance. |
Occurrence | Evaluates the likelihood of a failure mode occurring in the process. |
Detection | Assesses the capability of current controls to detect a potential failure before it reaches the customer. |
Root Cause Analysis (RCA)
Root Cause Analysis (RCA) systematically identifies underlying reasons for problems or incidents, aiming to prevent their recurrence by addressing the fundamental cause rather than just the symptoms. In the realm of quality control management techniques, RCA is pivotal for continual improvement and ensuring the delivery of high-quality products.
By employing RCA, organizations can proactively identify and rectify the root causes of issues, thereby enhancing customer satisfaction and loyalty. This method plays a crucial role in quality management systems, as it enables processes to be continuously refined, ultimately improving overall efficiency and effectiveness.
RCA is also aligned with methodologies such as Lean Six Sigma, as it delves deep into the factors contributing to a particular problem, thus providing insights for targeted improvements. It's essential for organizations to utilize RCA in conjunction with other quality control methods to make sure that the root causes of issues are effectively addressed.
This systematic approach to problem-solving not only resolves immediate concerns but also helps in preventing similar issues in the future, thereby bolstering the organization's reputation and customer trust.
Frequently Asked Questions
What Are 4 Strategies to Improve Quality Management?
To improve quality management, we implement the following strategies:
- Continuous improvement: This strategy focuses on reducing wastage and minimizing costs. It encourages a culture of quality improvement and ensures that processes are constantly being enhanced and optimized.
- Effective leadership: Engaging in effective leadership is crucial for achieving quality management goals. Leaders play a pivotal role in motivating and empowering employees, setting clear expectations, and providing guidance and support.
- Process approach: Adopting a process approach emphasizes the importance of efficiency and effectiveness. This strategy involves analyzing and optimizing processes to ensure that they are streamlined and aligned with quality objectives.
- People engagement: Embracing a people engagement strategy involves actively involving employees in delivering value and clarifying goals and responsibilities. This strategy fosters a sense of unity of purpose and encourages employees to contribute their skills and expertise towards achieving quality management goals.
These strategies work together to create a comprehensive approach to quality management. Through continuous improvement, effective leadership, a process approach, and people engagement, organizations can foster a culture of quality improvement, unity of purpose, and efficient management.
What Are the 4 Methods of Quality Control?
The 4 methods of quality control include:
- Statistical process control (SPC): This method utilizes statistical techniques for consistent quality and issue prevention.
- Lean manufacturing: This method focuses on optimizing processes and combining efficiency with high-quality standards.
- Total quality management (TQM): TQM encourages every team member to improve processes and prioritize customer satisfaction.
- 100% inspection: This method involves thoroughly examining all product parts for defects.
These methods collectively ensure high-quality products and customer satisfaction.
What Are the Techniques of Quality Control?
We implement statistical quality control, lean manufacturing, and continuous improvement to ensure consistent quality, optimize processes, and reduce waste.
Effective leadership provides unity of purpose, engages employees, and teaches, trains, and coaches.
Customer focus is vital for satisfying customers, exceeding their needs, and building loyalty.
These techniques help us maintain high standards of quality control.
What Are the Three Quality Management Techniques?
We believe the three quality management techniques are:
- Continuous improvement: This involves ongoing efforts to enhance services, products, and processes.
- Customer focus: This technique emphasizes satisfying and exceeding customer needs, building loyalty, and learning from mistakes.
- Effective leadership: This provides unity of purpose, engages employees, and considers stakeholder wants.
These techniques promote a culture of quality improvement, encourage employee involvement, and are essential for business success.
Conclusion
In conclusion, these three quality control management techniques are essential for businesses to maintain high standards and minimize defects.
Did you know that Six Sigma has been credited with saving companies over $427 billion in the last 20 years?
By implementing these techniques, businesses can ensure consistent quality, minimize variations, and prevent defects, ultimately leading to improved customer satisfaction and cost savings.
It's crucial for businesses to prioritize quality control to stay competitive in the market.
Randy serves as our Software Quality Assurance Expert, bringing to the table a rich tapestry of industry experiences gathered over 15 years with various renowned tech companies. His deep understanding of the intricate aspects and the evolving challenges in SQA is unparalleled. At EarnQA, Randy’s contributions extend well beyond developing courses; he is a mentor to students and a leader of webinars, sharing valuable insights and hands-on experiences that greatly enhance our educational programs.