Understanding the importance of ISO Certification in Quality Management Systems is crucial for any business striving for operational excellence. Obtaining ISO certification is vital for meeting customer needs and enhancing overall efficiency, thus playing a crucial role in the success of the company.
But how exactly does this certification work, and what are the specific benefits it offers? Stick with us as we break down the fundamentals and dive into the intricate world of ISO certification, uncovering the key insights that can revolutionize your quality control systems.
Key Takeaways
- ISO certification (specifically ISO 9001:2015) sets criteria for a quality management system based on quality management principles.
- ISO certification helps organizations meet customer and regulatory requirements and improve their quality management systems.
- ISO certification enhances customer satisfaction through effective processes and conformity to requirements.
- ISO certification helps organizations identify and eliminate inefficiencies, improving operational performance and customer trust.
ISO Certification Overview
ISO certification, specifically ISO 9001:2015, sets out the criteria for a quality management system. It's based on a number of quality management principles, including a strong customer focus, the motivation and implication of top management, and continual improvement.
This certification helps organizations to meet customer and regulatory requirements and continuously improve their quality management systems. By adhering to ISO standards, organizations can enhance customer satisfaction through the effective application of processes for improvement and conformity to customer and regulatory requirements.
The certification also provides guidelines for addressing customer complaints efficiently, thereby enhancing customer satisfaction. Furthermore, it helps organizations identify and eliminate inefficiencies, leading to improved operational performance and increased customer trust.
Quality Control Systems Basics
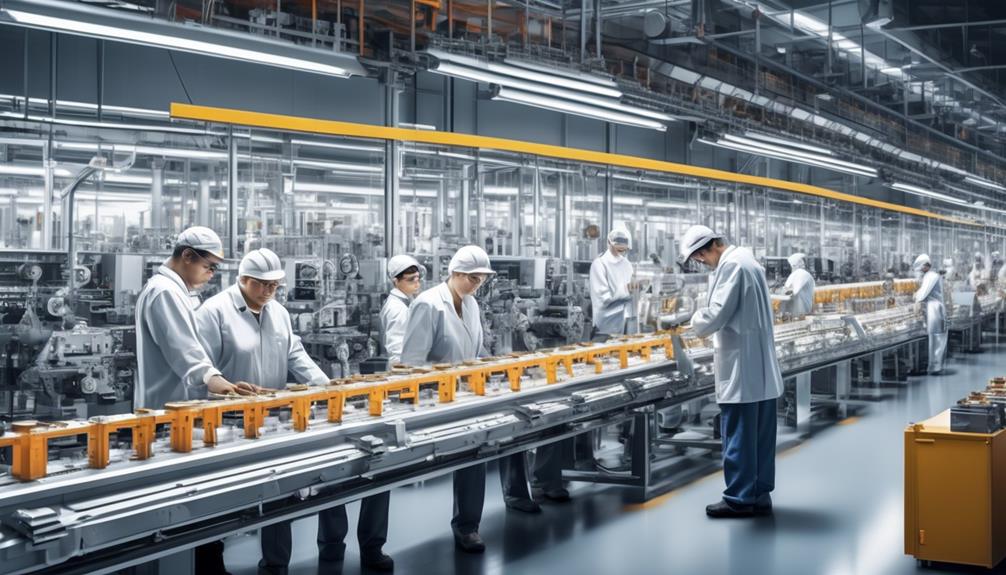
The implementation of quality control systems within an organization is essential for ensuring consistent product or service quality and meeting customer expectations. The ISO 9001:2015 standard, a widely recognized framework for quality management systems, provides a structured approach to achieving and maintaining high-quality products and services.
It applies to organizations of any size or industry, emphasizing the importance of continual improvement and customer satisfaction. The standard outlines requirements for a quality management system (QMS), encompassing aspects such as management responsibility and resource management. ISO 9001 certification signifies an organization's compliance with these standard requirements, demonstrating its commitment to fulfilling customer, statutory, and regulatory requirements while enhancing credibility.
The plan-do-check-act methodology forms the basis of ISO 9001, promoting a process-oriented approach to quality management. Organizations certified to previous versions, such as ISO 9001:2008, are encouraged to transition to ISO 9001:2015, with transition guidance available from the International Accreditation Forum (IAF).
Embracing the principles of ISO 9001 can significantly contribute to an organization's need for delivering and improving the quality of its products and services.
ISO 9001:2015 Requirements
Transitioning from the basics of quality control systems, the ISO 9001:2015 standard outlines comprehensive requirements for a quality management system (QMS) applicable to organizations of any size or industry.
The standard provides a structured framework aimed at helping organizations meet customer requirements, enhance the quality of their products and services, and improve customer satisfaction.
The ISO 9001:2015 requirements encompass various crucial aspects, including the responsibilities of management, resource management, product realization, and the measurement, analysis, and continual improvement of the QMS.
Organizations seeking to achieve ISO 9001 certification should thoroughly understand and implement these requirements to ensure compliance with the quality management system standard.
By adhering to ISO 9001:2015, organizations can demonstrate their commitment to fulfilling applicable statutory and regulatory requirements, while also enhancing their credibility and competitiveness in the global market.
Understanding and effectively incorporating these requirements can lead to significant improvements in an organization's operations and overall performance.
Implementing ISO Quality Control

Upon integrating ISO 9001:2015 into our organization's operations, we can begin implementing a robust system for quality control that emphasizes continual improvement and customer satisfaction. This involves adhering to the ISO 9001 standard requirements and adopting a process approach. It is essential to establish and maintain documented information that supports the operation of our quality management system. By doing so, we can effectively address risks and opportunities, and evaluate our performance to drive improvement.
Quality Management System | ISO 9001:2015 Implementation | Benefits |
---|---|---|
Process-Oriented Approach | Adhering to the standard requirements and focusing on a process approach ensures a systematic and efficient way of managing our processes. | Increases operational efficiency and customer satisfaction. |
Documented Information | Establishing and maintaining documented information supports the operation of our quality management system and demonstrates compliance with the standard. | Enhances transparency and clarity in our processes. |
Performance Evaluation | Through ongoing performance evaluation, we can identify areas for improvement and make data-driven decisions to enhance our quality management system. | Drives continual improvement and ensures the effectiveness of our processes. |
Implementing ISO 9001:2015 is a strategic decision that will benefit our organization by enhancing our credibility, increasing customer trust and satisfaction, and fostering a culture of continuous improvement.
Benefits of ISO Certification
ISO 9001 Certification enhances customer trust and satisfaction while promoting a culture of continuous improvement within organizations. The benefits of ISO 9001 certification are substantial and can significantly impact an organization's success.
Here are three key benefits:
- Enhanced Customer Satisfaction: ISO 9001 certification ensures that an organization's quality management system is robust and effective. This, in turn, allows the organization to consistently provide products and services that meet customer and regulatory requirements. By adhering to ISO standards, organizations can build a reputation for reliability and quality, leading to increased customer satisfaction and loyalty.
- Operational Efficiency and Cost Savings: Implementing ISO 9001 often leads to streamlined processes, reduced waste, and improved resource management. This results in cost savings and productivity gains for the organization. By adhering to the principles of ISO 9001, organizations can identify and eliminate inefficiencies, ultimately leading to improved operational performance.
- Competitive Advantage: ISO 9001 certification is globally recognized and demonstrates an organization's commitment to quality and continuous improvement. This can provide a competitive edge in the market, as many potential customers and partners prefer to work with certified organizations. Achieving ISO 9001 certification can open doors to new business opportunities and enhance an organization's reputation within its industry.
ISO Certification Process

As we shift our focus to the ISO Certification Process, it's essential to understand the ISO application process and the specific audit requirements.
These two pivotal points provide a detailed framework for organizations seeking ISO certification and are crucial in ensuring compliance with ISO standards.
ISO Application Process
When seeking ISO certification, organizations must first purchase a copy of the ISO standard and assess conformance before committing the necessary resources for implementation.
Transitioning from previous ISO versions to the latest standard is encouraged, with guidance available from the International Accreditation Forum (IAF).
Implementing the ISO standard and passing a registrar's audit to demonstrate compliance with ISO requirements are essential steps in the ISO application process.
It's crucial to consider the costs of registration, surveillance, and recertification audits during this process.
ISO 9001 certification signifies an organization's commitment to fulfilling customer, statutory, and regulatory requirements, thereby enhancing its credibility.
- Transitioning to the latest ISO standard is encouraged with guidance available from the International Accreditation Forum (IAF).
- Passing a registrar's audit to demonstrate compliance with ISO requirements is a crucial step in the ISO application process.
- Consideration of the costs of registration, surveillance, and recertification audits is essential during the ISO application process.
ISO Audit Requirements
After ensuring conformance with the ISO standard and passing a registrar's audit, organizations must focus on meeting the ISO audit requirements for certification. This involves implementing ISO 9001:2015 and demonstrating compliance with ISO 9001 requirements, including the quality management system (QMS) and fulfilling customer, statutory, and regulatory requirements. The process also encompasses transitioning from ISO 9001:2008 to ISO 9001:2015 and assessing conformance with ISO 9001 requirements. Additionally, organizations should consider the costs of registration, surveillance, and recertification audits. Guidance for the transition process can be downloaded from the International Accreditation Forum (IAF). Below is an overview of the ISO audit requirements:
Internal Audit | External Audit |
---|---|
Self-assessment of QMS | Conducted by a certification body |
Ensures compliance with ISO 9001 requirements | Validates conformity with ISO standards |
Identifies areas for improvement | Provides an independent evaluation |
Integral part of maintaining QMS effectiveness | Essential for achieving certification |
Helps prepare for certification audits | Demonstrates commitment to quality |
Quality Control Audits
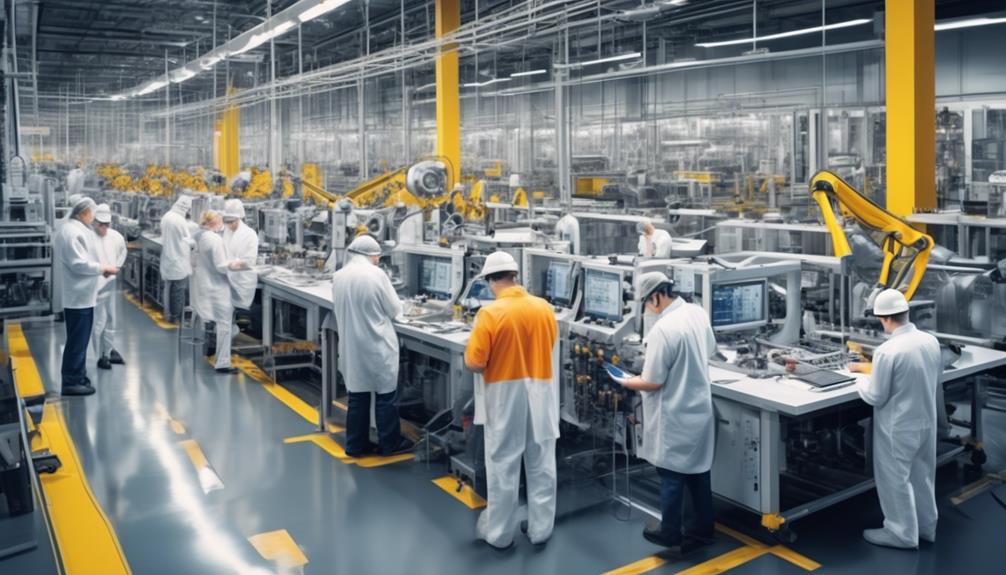
Quality Control Audits are essential processes that systematically examine an organization's quality management system to ensure compliance with ISO 9001 requirements. These audits assess the effectiveness of an organization's quality processes, identifying areas for improvement and ensuring adherence to standards. They involve evaluating documentation, procedures, and records, and may include on-site inspections and interviews with personnel. The goal of Quality Control Audits is to verify that the organization's quality management system is functioning as intended and delivering on its objectives. Through these audits, organizations can demonstrate their commitment to quality and continuous improvement, ultimately enhancing customer satisfaction.
- Systematic Examination: Quality Control Audits involve a methodical and thorough examination of an organization's quality management system to ensure it meets customer and applicable regulatory requirements.
- Identifying Improvement Areas: These audits provide guidance on areas where organizations can improve their quality management processes to consistently meet ISO 9001 standards, including a strong customer focus.
- Enhancing Customer Satisfaction: By conducting Quality Control Audits, organizations can show their dedication to providing high-quality products and services, ultimately enhancing customer satisfaction.
Maintaining ISO Certification

To maintain ISO certification, organizations must regularly review and update documented information, such as procedures, work instructions, and policies, to ensure ongoing compliance with ISO standards. Additionally, conducting internal audits is essential for assessing conformity with ISO 9001 requirements and identifying areas for improvement within the quality management system. It is crucial to provide ongoing training and support to ensure that staff are knowledgeable and competent in implementing the quality management system effectively. Staying informed about any revisions or updates to the ISO 9001 standard is imperative, and organizations should take necessary steps to transition to the latest version. Engaging in continuous improvement activities is also vital to enhance the effectiveness of the quality management system and meet customer expectations.
Key Activities for Maintaining ISO Certification | Description |
---|---|
Regular Review and Update of Documented Information | Ensuring ongoing compliance with ISO standards by updating procedures, work instructions, and policies. |
Conducting Internal Audits | Assessing conformity with ISO 9001 requirements and identifying areas for improvement within the quality management system. |
Providing Ongoing Training and Support | Ensuring staff are knowledgeable and competent in implementing the quality management system effectively. |
Staying Informed about ISO 9001 Revisions | Taking necessary steps to transition to the latest version of the ISO 9001 standard. |
ISO Certification Resources

As we explore the topic of 'ISO Certification Resources', it's important to consider the valuable tools and materials available to support organizations in maintaining their ISO certification and continuously improving their quality management systems. These resources play a crucial role in helping organizations adhere to ISO 9001 QMS and the quality management principles of the ISO 9000 family.
Here are some essential resources:
- ISO 9001:2015 Standard**: The standard helps organizations organize and improve their processes. It provides a framework for a robust quality management system, enabling organizations to meet customer and regulatory requirements effectively.
- International Accreditation Forum (IAF) Guidance: Organizations can download guidance on transitioning from the IAF. This resource assists organizations in understanding the requirements and processes for transitioning to the updated ISO 9001:2015 standard, ensuring a smooth and successful transition.
- ISO 9001 Training Materials**: Access to ISO 9001 training materials is vital for educating employees on the standard's requirements and principles. These materials facilitate the implementation and maintenance of a quality management system, fostering a culture of continuous improvement within the organization.
Best Practices for Quality Control Systems

Implementing best practices for quality control systems is essential for organizations aiming to maintain ISO certification and achieve continuous improvement in their quality management processes.
To meet ISO 9001 standards, organizations should adopt a process-oriented approach to quality management, ensuring that their quality management system (QMS) addresses all the requirements outlined in the standard.
Best practices involve a commitment to understanding and meeting customer requirements, as well as striving to continually improve the quality of products and services. This can be achieved by establishing robust processes for identifying inefficiencies, reducing waste, and making informed decisions based on data analysis.
Additionally, organizations should embrace the plan-do-check-act methodology, which encourages a systematic and proactive approach to quality control.
By adhering to these best practices, organizations can enhance their QMS, leading to improved customer satisfaction, greater operational efficiency, and a stronger competitive position in the market.
Frequently Asked Questions
What ISO Standards Are Used for Quality Control?
We use ISO 9000 standards for quality control. They provide a framework for managing and improving our processes.
ISO 9001:2015 is particularly relevant, as it's applicable to organizations of any size or industry. Over a million organizations from 160+ countries have implemented this standard.
It helps us ensure that our products and services consistently meet customer requirements and regulatory standards.
Transitioning to ISO 9001:2015 is encouraged, and guidance is available from the International Accreditation Forum (IAF).
What Do You Understand by ISO Quality Certification?
We understand ISO quality certification as a validation of an organization's adherence to ISO 9001 requirements for quality management.
It signifies our commitment to fulfilling customer needs, statutory and regulatory requirements, and maintaining a culture of continuous improvement.
This certification enhances our organization's credibility and demonstrates our dedication to providing high-quality products and services.
It also helps us to increase customer trust and satisfaction, achieve cost savings, and ensure long-term success.
What Is the ISO for Qms?
ISO for QMS refers to ISO 9001:2015, an internationally recognized standard for Quality Management Systems. It provides a framework for organizations to establish, implement, maintain, and continually improve their quality management processes.
Our team ensures that QMS aligns with ISO 9001:2015 requirements, enhancing our organization's credibility and demonstrating our commitment to quality.
What Is ISO 9001 Easy Way to Understand?
ISO 9001 is a globally recognized standard that sets out the criteria for a quality management system. It provides a systematic approach to managing processes and ensuring that customer needs are met. By following its principles, organizations can improve efficiency, reduce risks, and enhance customer satisfaction.
Achieving ISO 9001 certification signals an organization's commitment to quality and can boost its reputation. It's a valuable tool for demonstrating compliance and driving continual improvement.
Conclusion
In conclusion, achieving ISO certification for our quality control systems has been a game-changer for our organization. It has allowed us to streamline our processes, improve customer satisfaction, and foster a culture of continuous improvement.
We're now able to 'hit the bullseye' when it comes to meeting customer expectations and delivering high-quality products and services. ISO certification has truly helped us 'aim for the stars' and elevate our organization to new heights.
Randy serves as our Software Quality Assurance Expert, bringing to the table a rich tapestry of industry experiences gathered over 15 years with various renowned tech companies. His deep understanding of the intricate aspects and the evolving challenges in SQA is unparalleled. At EarnQA, Randy’s contributions extend well beyond developing courses; he is a mentor to students and a leader of webinars, sharing valuable insights and hands-on experiences that greatly enhance our educational programs.