Embarking on the path of statistical quality control is comparable to setting off on an expedition with a reliable compass, guiding us through the complexities of enhancing and sustaining product quality.
These 5 key tips serve as our compass, directing us towards the path of effective quality control. But what are these tips? How can they be implemented to ensure that quality goals are not just met, but consistently exceeded?
Join us as we explore these essential strategies and unlock the potential for significant improvements in quality control within organizations.
Key Takeaways
- Define specific, measurable, achievable, relevant, and time-bound quality goals.
- Choose the right SQC tools such as control charts, histograms, Pareto charts, and scatter plots to monitor and improve quality.
- Calculate quality costs and identify areas for improvement to reduce defects.
- Communicate the results of SQC efforts effectively, highlighting the benefits and improvements achieved.
Define Quality Goals
To establish effective quality goals, we must ensure they're specific, measurable, achievable, relevant, and time-bound (SMART) in order to drive successful achievement.
In defining quality goals, it's crucial to identify the key quality characteristics or attributes that directly impact the defined quality goals. This involves a meticulous approach to understanding the statistical process and using it to set precise and achievable targets.
For instance, quality goals could involve reducing defective units by a certain percentage within a specified time frame or improving specific customer satisfaction metrics. These goals should encompass various aspects such as dimensions, weight, color, functionality, and reliability.
It's essential to ensure that the defined quality goals align with industry regulations and internal criteria for effective quality control and quality assurance. By establishing clear quality standards, an organization can effectively measure results and continuously improve its processes.
This methodical approach to defining quality goals is the cornerstone of statistical quality control, ensuring that the entire quality management process is well-directed and optimized for success.
Choose the Right SQC Tools
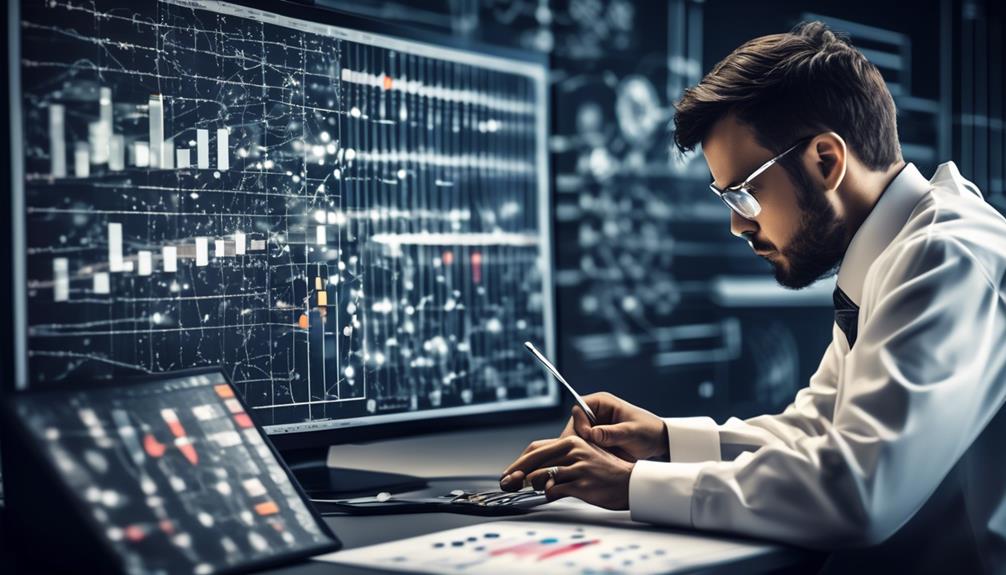
Selecting the appropriate SQC tools is critical for effectively monitoring and improving quality through data collection, analysis, and display. Control charts are essential statistical tools to monitor variation over time and assess if quality meets acceptable limits. They provide a visual representation of data, enabling quick identification of trends or patterns that may signify process instability.
Histograms are valuable for understanding data distribution and variation, aiding in pinpointing potential areas for quality improvement within the production process. Pareto charts prioritize critical issues, facilitating a focused approach to addressing key improvement areas. By identifying and addressing the most significant problems first, resources can be efficiently allocated for maximum impact.
Additionally, scatter plots are instrumental in exploring potential correlations or causes between variables, aiding in identifying relationships impacting quality. The use of statistical process control tools such as these is essential for organizations seeking to measure the quality of their production process accurately and make informed decisions to drive continuous improvement.
Calculate Quality Costs
Analyzing quality costs provides valuable insights into the financial implications of maintaining and improving product quality. To calculate quality costs effectively, we must consider the following:
- Understanding the Components: Quality costs consist of prevention, appraisal, internal failure, and external failure costs. It's crucial to comprehend the specific activities and expenses associated with each category to accurately assess the overall quality costs.
- Prevention and Appraisal Costs: These are proactive measures aimed at avoiding and identifying defects early in the production process, including activities like training, planning, testing, and audits. Understanding these costs enables businesses to allocate resources effectively to minimize potential defects.
- Internal and External Failure Costs: These costs are incurred when defects are found within the organization or by customers, leading to rework, scrap, complaints, or warranty claims. By quantifying these costs, organizations can identify areas for improvement and prioritize efforts to reduce defects.
Communicate the Results
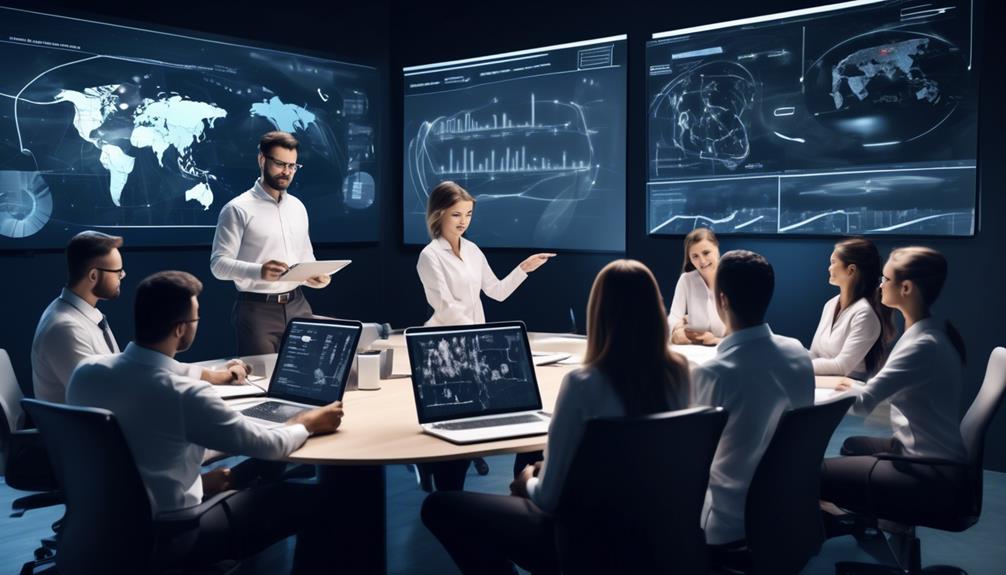
When presenting the results of Statistical Quality Control (SQC) efforts, we use clear and concise language to effectively communicate the achievements and benefits of improved quality performance and consistency. It is crucial to highlight the positive impact of SQC implementation on various aspects of quality control, such as reduced waste and rework, increased customer satisfaction and loyalty, enhanced reputation, competitiveness, productivity, and profitability. By effectively communicating the results of the analysis, stakeholders, customers, and managers can gain valuable insights into the improvements in the production line and the overall quality of products. This visibility helps in building trust and confidence in the effectiveness of SQC processes.
Results of Statistical Quality Control (SQC) | Benefits |
---|---|
Improved quality performance and consistency | Reduced waste and rework |
Increased customer satisfaction and loyalty | Enhanced reputation and competitiveness |
Higher productivity and profitability |
Additional Considerations
To ensure a comprehensive understanding of statistical quality control, it's important to consider additional factors and perspectives that contribute to its successful implementation and impact on quality management. When exploring statistical quality control, it's essential to delve into the processes used in handling raw materials. Understanding safety and compliance measures is crucial to maintain a high standard of quality control. Additionally, evaluating the number of defective units is imperative to make data-driven decisions that uphold quality standards.
Furthermore, it's imperative to comprehend the implications of continuing to operate under specific conditions. This includes considering the potential risks associated with production and the acceptance of certain levels of deviation. Delving into the practical implementation of statistical process control aids in maintaining consistent quality in processes. This involves building proper processes, maintaining a clean workspace, conducting unscheduled equipment use tests, managing essential spare parts, and ensuring managers are properly trained for effective quality control.
These additional considerations are instrumental in reinforcing the overall quality control framework, ensuring that products and processes meet the highest standards.
Frequently Asked Questions
What Are the 3 Basics of Statistical Process Control?
The three basics of statistical process control are sampling, statistical methods, and control charts.
Sampling and statistical methods are used to monitor ongoing processes, while control charts help identify causes of variation.
Different types of control charts, such as x̄-charts and p-charts, are utilized based on the type of data being monitored.
Implementing control charts involves plotting sample mean values and taking corrective action when values fall outside control limits, ensuring consistent quality by addressing variations.
What Are the Main Techniques of Statistical Quality Control?
We use various techniques for statistical quality control. These include control charts, histograms, Pareto charts, and scatter plots. These tools help us monitor ongoing process quality and identify causes of variation.
Additionally, we calculate quality costs, consider acceptance sampling and producers/consumers risk, and communicate results effectively. This multifaceted approach ensures we maintain high standards, minimize waste, and continuously improve our processes.
What Is the Most Important Element in Statistical Quality Control?
The most important element in statistical quality control is continuous monitoring and adjustment of ongoing processes. This ensures that quality standards are consistently met and any deviations are promptly addressed.
By using statistical methods and sampling, we can detect variations and make necessary improvements, ultimately enhancing the overall quality of our processes and products.
This proactive approach is crucial for maintaining high quality and meeting customer expectations.
What Is the Major Goal of Statistical Quality Control?
Our goal in Statistical Quality Control is to monitor and maintain product or process quality using statistical tools.
We aim to identify and minimize variations, ensuring consistency and meeting customer requirements.
This involves using statistical methods to detect and address deviations from quality standards.
By implementing Statistical Quality Control, organizations can make data-driven decisions, reduce waste, and optimize processes.
Ultimately, this enhances product quality, reliability, and performance while minimizing costs.
Conclusion
In conclusion, by defining quality goals, choosing the right SQC tools, calculating quality costs, communicating results, and considering additional factors, organizations can effectively monitor and improve product quality.
These tips provide a methodical approach to quality control, ensuring that specific and measurable goals are met while also taking into account other perspectives and factors.
It's a precise and analytical way to drive continuous improvement and compliance with regulatory requirements.
Randy serves as our Software Quality Assurance Expert, bringing to the table a rich tapestry of industry experiences gathered over 15 years with various renowned tech companies. His deep understanding of the intricate aspects and the evolving challenges in SQA is unparalleled. At EarnQA, Randy’s contributions extend well beyond developing courses; he is a mentor to students and a leader of webinars, sharing valuable insights and hands-on experiences that greatly enhance our educational programs.