Our production facility has just implemented a new quality control method that resulted in a 15% reduction in defects and a 20% boost in overall efficiency in the first quarter.
Quality control management strategies are essential for ensuring that products and services meet the required standards and satisfy customer needs. However, understanding and implementing effective quality control measures can be a complex process.
In this discussion, we will explore the top quality control management strategies that organizations can employ to enhance their overall quality control processes and achieve better outcomes. From the importance of quality control systems to implementing effective strategies and ensuring compliance, we will delve into the key components and best practices that can significantly impact an organization's quality control efforts.
Key Takeaways
- Continuous improvement is a vital strategy in quality control management, focusing on consistently enhancing processes, products, and services.
- Implementing a process approach helps in analyzing and optimizing workflows, ensuring efficiency and effectiveness in quality control.
- Technology plays a significant role in quality control, enabling the implementation of best practices and streamlining processes.
- Quality control is essential for ensuring products or services meet quality standards, reducing costs, maintaining compliance, and building a strong brand reputation.
Quality Control Management Overview
In quality control management overview, we focus on implementing strategies that ensure the consistent delivery of high-quality products or services to meet customer expectations and organizational goals.
One of the key components of quality control management is the concept of Continuous Improvement. This involves ongoing efforts to enhance services, products, and processes. By continuously striving to improve, we can reduce time and effort wastage, minimize project costs, and prevent overages. Moreover, it establishes a culture of quality improvement within the organization and encourages employee involvement and rewards.
Another vital aspect is the Process Approach. This method manages the business as a system of interconnected processes. It emphasizes efficiency and effectiveness, ensuring that quality is maintained through effective management of inputs and outputs. By treating processes as interconnected, we can effectively manage the organization and guarantee quality.
These strategies are fundamental in Quality Management and are essential for any organization looking to maintain and improve the quality of their products and services.
Importance of Quality Control Systems
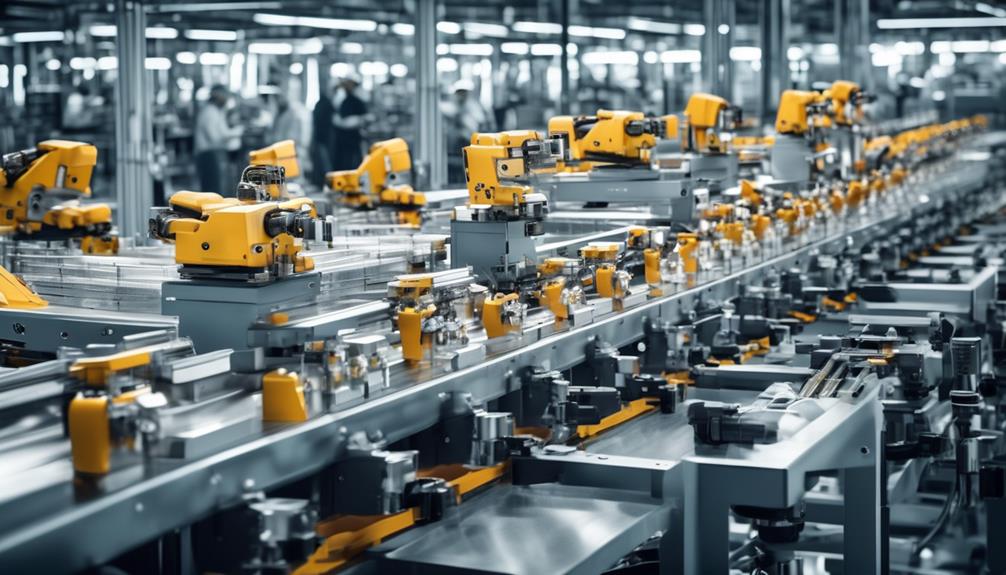
Understanding the crucial role of quality control systems is essential for achieving consistent product or service quality and meeting customer expectations effectively.
Quality control plays a vital role in ensuring that products or services meet established quality standards and customer requirements. It encompasses a systematic approach to quality improvement, focusing on the entire process approach from raw material sourcing to the delivery of the final product or service.
By implementing quality control systems, organizations can identify and rectify defects or issues in a timely manner, reducing costs and enhancing operational efficiency. Moreover, adhering to quality standards and regulations is critical for maintaining compliance and building a strong brand reputation.
Quality control not only involves the implementation of robust processes and procedures but also emphasizes the importance of continuous improvement. This approach fosters a culture of quality within the organization, ensuring that quality isn't just a goal but a fundamental aspect of the organizational mindset.
Ultimately, the importance of quality control systems lies in their ability to drive consistency, reliability, and customer satisfaction while contributing to the overall success of the organization.
Key Components of Quality Control
Emphasizing the significance of quality control systems, we now turn our focus to the key components that underpin its effectiveness in ensuring consistent product or service quality and meeting customer expectations.
- Identifying Defects and Issues: One of the fundamental components of quality control is the ability to identify defects and issues in the production process. This involves rigorous inspection, testing, and monitoring at various stages to catch any deviations from quality standards.
- Improving Processes: Quality control isn't just about catching defects; it also involves continuously improving processes to prevent future occurrences. This proactive approach requires a thorough understanding of the production methods and the willingness to implement changes for enhanced quality.
- Establishing Quality Metrics: Quality control relies on the establishment of clear quality metrics. These metrics serve as benchmarks for evaluating the performance of the product or service, ensuring that it meets predetermined standards.
- Ensuring High-Quality Products: Ultimately, the main goal of quality control is to guarantee the production of high-quality products that consistently meet customer expectations. This involves a comprehensive approach that encompasses the entire production cycle, from raw materials to finished goods.
Quality Control Best Practices
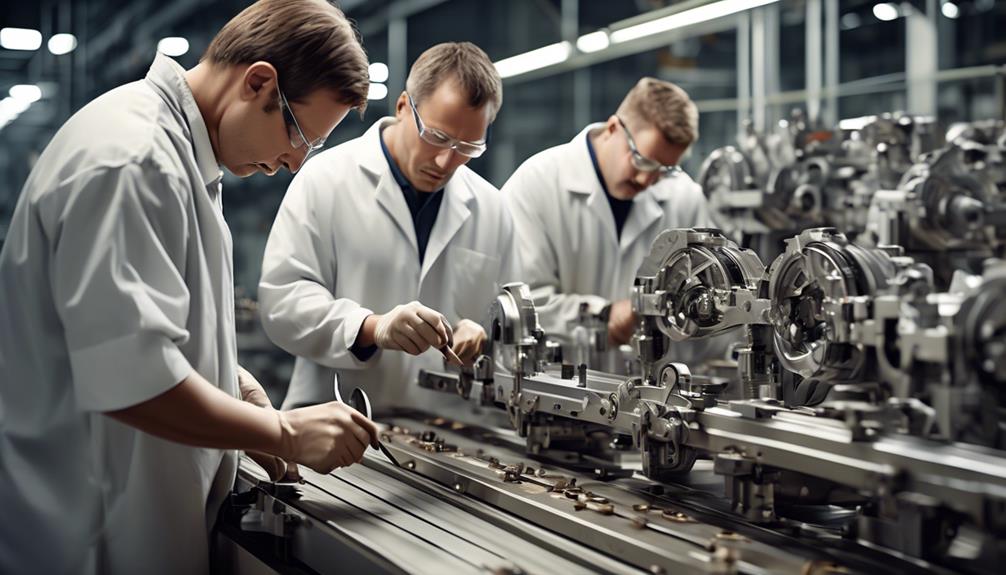
Implementing quality control best practices is essential for ensuring consistent product or service quality and meeting customer expectations.
Quality planning is crucial in establishing the processes and standards necessary to achieve total quality. It involves identifying quality requirements and standards relevant to the project and determining how to satisfy them.
Customer satisfaction is at the core of quality control best practices. Understanding customer needs and expectations, and continuously striving to exceed them, is paramount.
Data analysis plays a critical role, as it provides the necessary insights to make informed decisions and drive continuous improvement.
Total quality is achieved through a combination of quality register, continuous improvement, customer focus, effective leadership, and a process approach.
These best practices ensure that the organization maintains a clear focus on delivering high-quality products and services, while also fostering a culture of ongoing improvement and innovation.
Implementing Quality Control Processes
To establish effective quality control processes, a comprehensive analysis of the current production methods and identification of potential areas for improvement is essential. It's crucial for us to continuously assess and enhance our approach to quality to ensure the consistent high quality of products.
Here are four key steps to successfully implement quality control processes:
- Process Mapping: We'll meticulously map out our production processes to identify any inefficiencies or bottlenecks that may impact the quality of products. This will enable us to streamline operations and optimize quality control measures.
- Training and Education: Our team will receive comprehensive training to understand the importance of quality control and the specific processes involved. This will empower employees to actively contribute to improving processes and achieving quality.
- Utilizing Technology: We'll leverage advanced technologies such as automation and data analytics to monitor and enhance the quality of products in real time. This proactive approach enables us to address any issues swiftly and maintain high standards.
- Feedback Mechanisms: Implementing robust feedback mechanisms will allow us to gather insights from customers, employees, and stakeholders, facilitating continuous improvement in our quality control processes.
Role of Technology in Quality Control
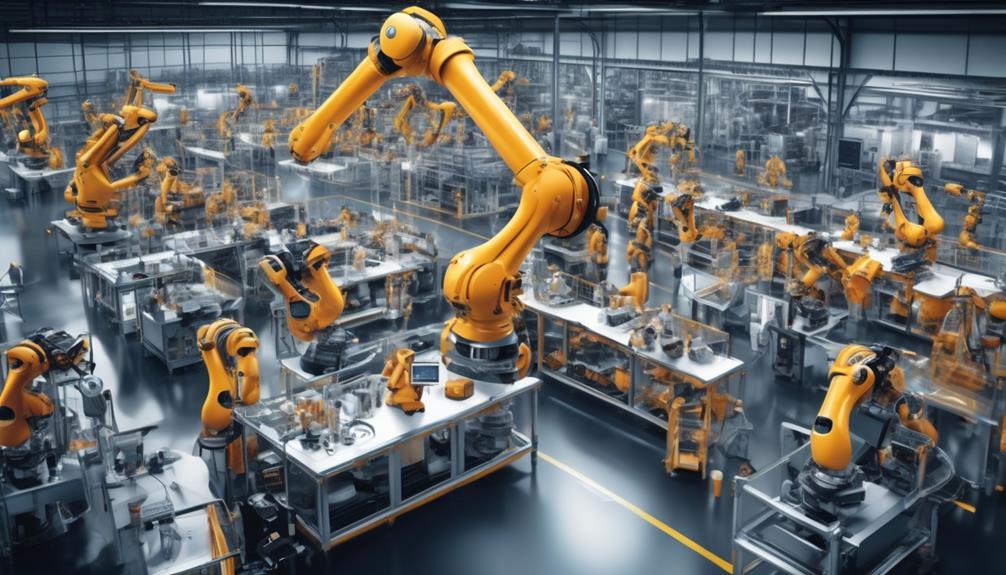
After meticulously mapping out our production processes and identifying areas for improvement, we can now explore the pivotal role of technology in enhancing quality control management.
Technology plays a critical role in improving the quality of services through enhanced visibility and process automation. By utilizing quality management software programs, organizations can analyze data to identify areas for improvement and achieve their quality goals. This enhanced visibility allows for a more thorough understanding of the production process, enabling us to make informed decisions for process improvement. Additionally, platforms like Quickbase provide the capability to automate quality processes, reducing effort and errors while streamlining operations.
Incorporating technology into quality control management also aligns with the principles of lean manufacturing, as it helps in identifying and eliminating waste within the production process. Furthermore, technology enables the implementation of regular audits to ensure that quality standards are consistently met.
Quality Control in Project Management
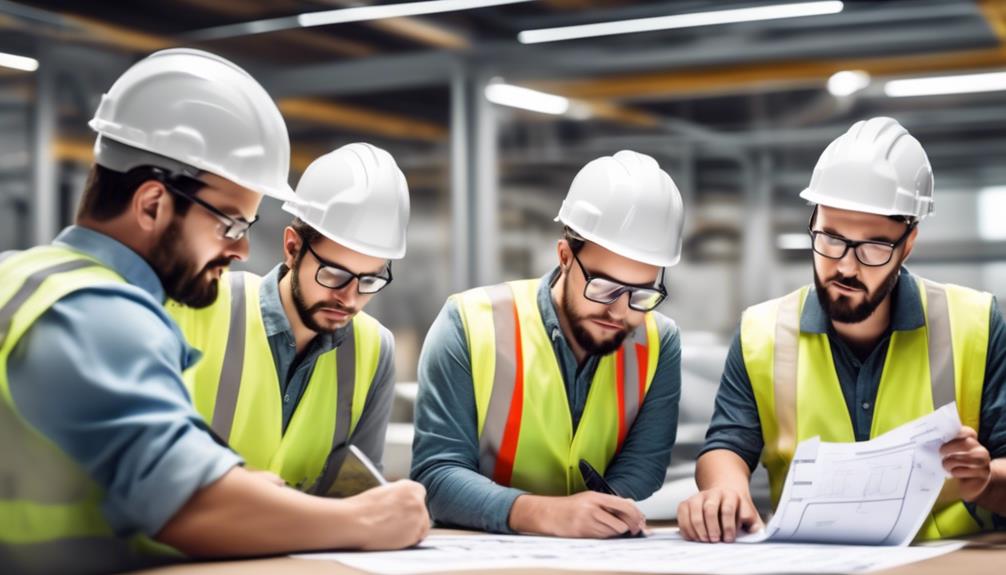
Quality control in project management involves ensuring that the deliverable or product meets end-user requirements, saving resources by reducing the need for do-overs. To achieve effective quality control in project management, it's essential to:
- Identify Areas for Improvement: Quality control management strategies in project management necessitate a thorough examination of the project's processes and outputs to identify areas that require improvement. This proactive approach ensures that issues are addressed before they impact the final deliverable.
- Align with Customer Expectations: Project management quality control should prioritize aligning the project's outcomes with the expectations of the end-users or customers. This involves continuous communication and feedback loops to ensure that the project meets or exceeds customer requirements.
- Implement quality control techniques: Utilize quality control techniques such as audits, benchmarking, cause and effect diagrams, checklists, and flowcharts to systematically monitor and improve the quality of project deliverables.
- Utilize Project Management Tools: Leveraging project management tools like Monday.com can facilitate efficient quality control by enabling real-time collaboration and providing dedicated interfaces for project quality management.
Effective Quality Control Strategies
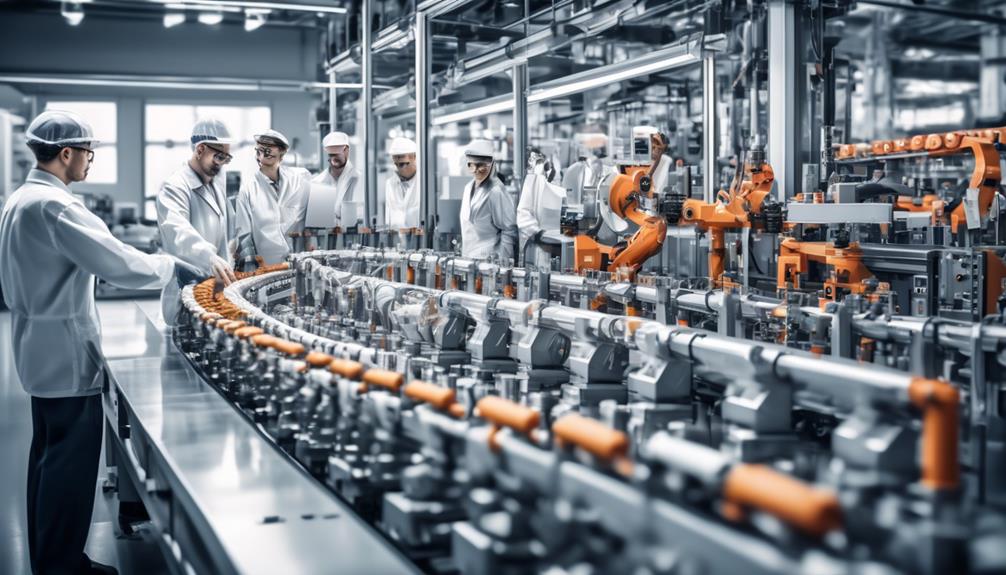
Focused on achieving continuous improvement and customer satisfaction, effective quality control strategies are essential for optimizing project outcomes and ensuring long-term success.
One key aspect of effective quality control strategies is the incorporation of customer feedback. By actively seeking and incorporating customer input, businesses can tailor their products and services to meet customer needs and exceed their expectations.
Additionally, implementing Six Sigma quality principles can significantly enhance quality control efforts. This data-driven approach focuses on minimizing defects and variations in processes, ultimately leading to improved quality and customer satisfaction.
Furthermore, adopting a process approach allows organizations to manage their business as a system of interconnected processes, emphasizing efficiency and effectiveness. This systematic method ensures that all processes are aligned with quality objectives and enables continuous improvement.
Effective leadership plays a crucial role in driving quality control strategies, providing direction, and fostering a culture of quality improvement.
Continuous Improvement in Quality Control
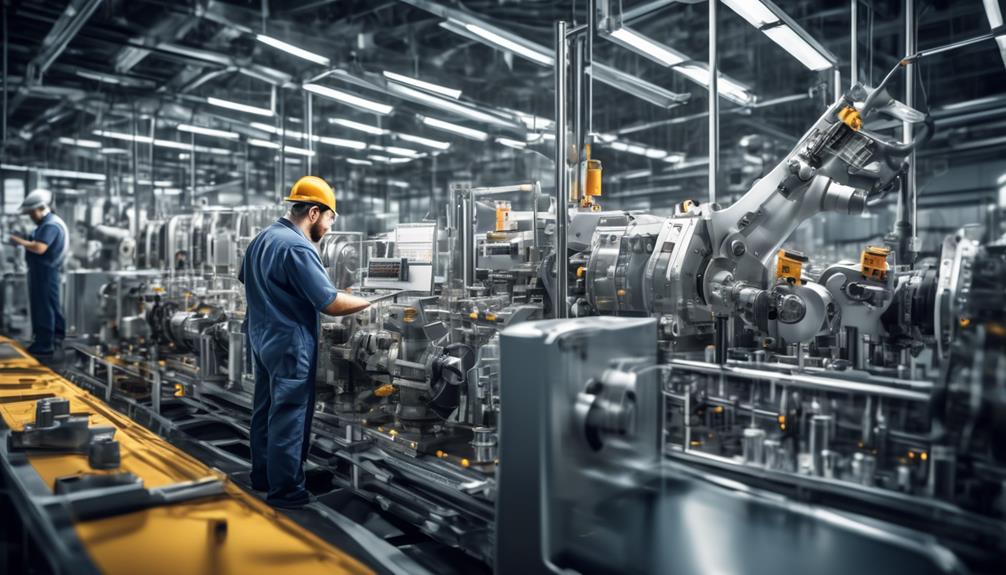
Incorporating customer feedback and implementing Six Sigma quality principles has laid the foundation for our continuous improvement in quality control, fostering a culture of excellence and efficiency within our organization.
To ensure consistent enhancement in quality control, we've embraced the following strategies:
- Ongoing Efforts: Continuous improvement in quality control involves the ongoing enhancement of services, products, and processes. This approach enables us to adapt to changing customer needs and market dynamics effectively.
- Employee Involvement: We encourage active participation from our employees, rewarding innovative ideas, and fostering a culture of learning from mistakes. This engagement strategy fosters a sense of ownership and responsibility for quality improvement at all levels.
- Process Approach: Embracing a holistic view, we adopt a process approach to quality control. This involves analyzing and optimizing workflows, identifying bottlenecks, and streamlining operations for maximum efficiency.
- Evidence-Based Decision-Making: Our continuous improvement in quality control is driven by evidence-based decision-making. We rely on data and analysis to identify areas for improvement, measure progress, and make informed decisions for quality enhancement.
Metrics for Assessing Quality Control
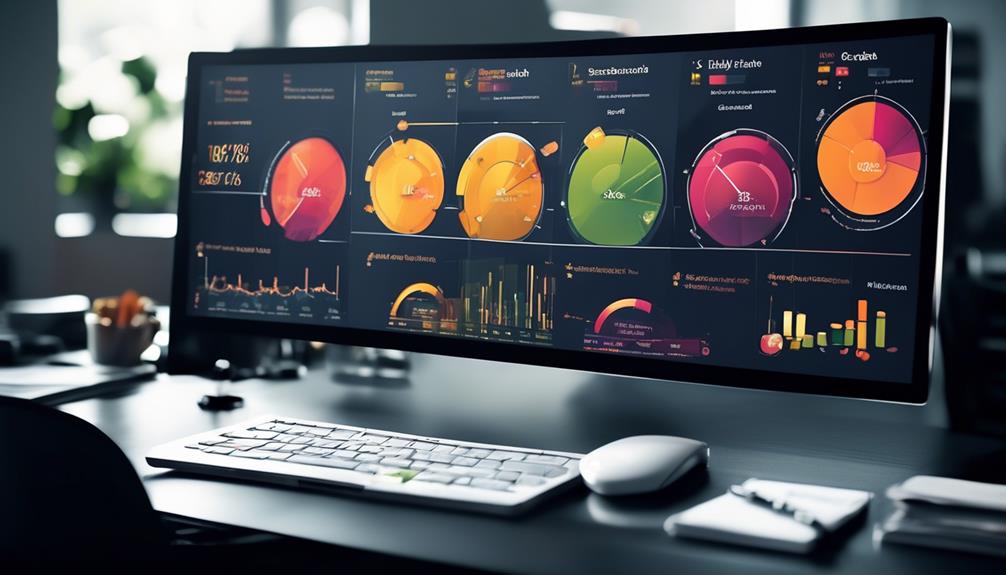
As we delve into the realm of assessing quality control, we are presented with a set of crucial metrics that serve as vital indicators of process efficiency and product excellence. These metrics play a pivotal role in identifying areas that require improvement and in optimizing strategies to boost the quality of products and processes. Below, we have outlined some key metrics for assessing quality control:
Metrics | Description | Importance |
---|---|---|
Defect Rate | Measures the number of defects in a product or process to identify areas for improvement. | Crucial for identifying quality issues early on. |
Customer Satisfaction Scores | Assess customer feedback and satisfaction to gauge the effectiveness of quality control efforts. | Essential for understanding customer perception and loyalty. |
On-Time Delivery | Tracks the percentage of products or services delivered on time to evaluate process efficiency. | Critical for meeting customer expectations and deadlines. |
These metrics are essential components of top quality control management strategies explained, and they provide valuable insights into the effectiveness of quality control processes, ultimately contributing to the enhancement of overall product and process quality.
Ensuring Compliance in Quality Control
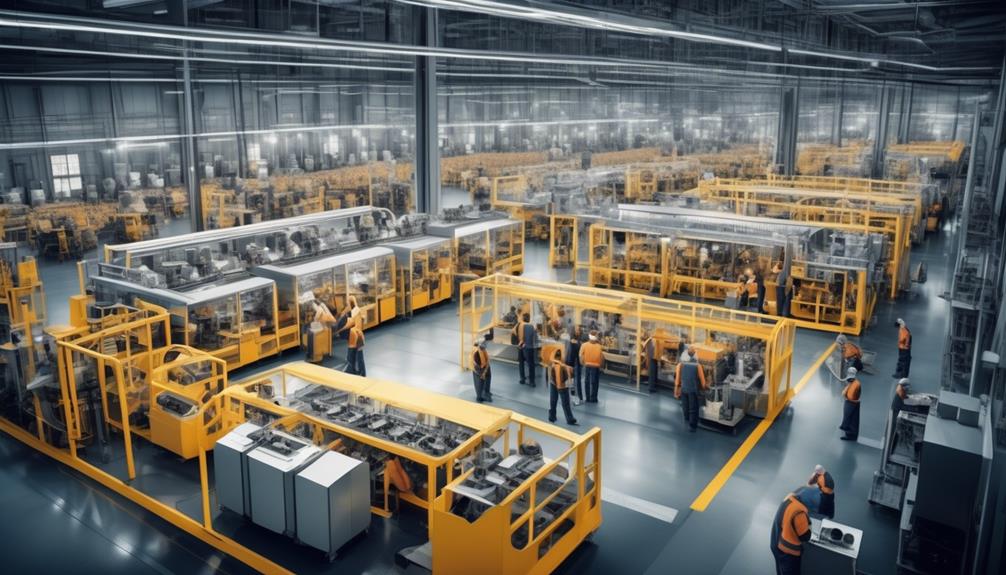
How does effective leadership play a crucial role in ensuring compliance in quality control efforts within an organization?
Effective leadership helps ensure compliance in quality control by setting the tone for ethical behavior and accountability throughout the organization, which is crucial for maintaining high standards and adhering to regulations. The following key aspects highlight the significance of effective leadership in ensuring compliance in quality control:
- Engaging Employees: Effective leadership fosters employee engagement, ensuring that everyone understands the importance of compliance and actively contributes to quality control efforts.
- Stakeholder Consideration: Strong leadership considers the needs and expectations of all stakeholders, aligning quality control efforts with the broader interests of the organization and its stakeholders.
- Ethical Conduct: Leadership sets an example of ethical conduct, which helps keep quality control efforts in compliance with industry regulations and standards.
- Continuous Improvement: Through effective leadership, a culture of continuous improvement is cultivated, helping to identify and address compliance issues proactively.
Effective leadership is the crucial first step in ensuring compliance in quality control, as it establishes the foundation for a robust quality management system.
Frequently Asked Questions
What Are the 4 Strategies to Improve Quality Management?
We improve quality management through four key strategies:
- The quality register tracks and summarizes quality activities.
- The continuous improvement strategy focuses on ongoing efforts.
- Customer focus emphasizes satisfying and exceeding customer needs.
- Effective leadership provides unity of purpose.
Each strategy plays a critical role in ensuring quality management.
These strategies, when implemented effectively, lead to improved products, services, and processes, reducing wastage and encouraging employee involvement.
What Is QC Strategy?
We define QC strategy as the systematic approach to ensuring product or service quality meets or exceeds customer expectations.
It involves setting quality standards, implementing processes to meet those standards, and continuously monitoring and improving quality.
This approach helps in identifying and addressing defects or errors in the production process, ultimately leading to higher customer satisfaction and loyalty.
What Are the 4 Types of Quality Control?
We can categorize quality control into four types:
- Planning: This involves setting quality standards and creating processes to meet them.
- Implementation: This focuses on executing the planned quality control activities.
- Taking action for improvements: This involves addressing any issues that arise and making necessary adjustments.
- Continuous reassessment: This ensures that the quality control processes remain effective and efficient.
What Is Quality Control in Strategic Management?
In strategic management, quality control involves:
- Setting clear objectives
- Implementing robust processes
- Conducting regular inspections
- Continuously improving practices
For example, our company employed quality control by:
- Establishing standards for product defects
- Conducting regular audits to ensure compliance
This approach:
- Minimizes costs
- Fosters a culture of improvement
- Enhances customer loyalty
Customer focus, effective leadership, and a process approach are essential components in achieving quality control in strategic management.
Conclusion
In conclusion, quality control management is the compass that steers our project towards success.
Like a skilled navigator, it guides us through the turbulent waters of project execution, ensuring that we stay on course and reach our destination of high-quality deliverables.
By implementing effective quality control strategies and continuously improving our processes, we can chart a path towards excellence and set sail for success in all our future projects.
Randy serves as our Software Quality Assurance Expert, bringing to the table a rich tapestry of industry experiences gathered over 15 years with various renowned tech companies. His deep understanding of the intricate aspects and the evolving challenges in SQA is unparalleled. At EarnQA, Randy’s contributions extend well beyond developing courses; he is a mentor to students and a leader of webinars, sharing valuable insights and hands-on experiences that greatly enhance our educational programs.