Have you ever paused to consider if your current strategies for enhancing continuous quality assurance are truly effective, or if they are simply sustaining the current state?
It’s easy to fall into the trap of sticking with traditional methods, assuming they are the best option. But what if there are better, more innovative approaches out there that could significantly elevate your organization’s quality assurance processes?
In our ever-evolving landscape, it’s imperative to question, adapt, and enhance our strategies to stay ahead. This discussion aims to shed light on why rethinking QA continuous improvement tactics is more crucial now than ever before.
Key Takeaways
- Continuous improvement in QA drives innovation and ensures that processes are regularly assessed and refined.
- Implementing continuous improvement in QA enhances the quality of products and services, leading to higher customer satisfaction and loyalty.
- By staying ahead of market demands through continuous improvement, businesses can propel long-term growth and gain a competitive advantage.
- Creating a culture of operational excellence through continuous improvement increases operational efficiency, eliminates waste, and optimizes resources.
Importance of Continuous Improvement in QA
Implementing continuous improvement practices in quality assurance is essential for driving innovation, increasing operational efficiency, and fostering a culture of operational excellence. Continuous improvement drives innovation by encouraging regular assessment and refinement of processes, leading to the identification of new, more efficient methods and technologies. This proactive approach not only enhances product and service quality but also propels long-term growth by staying ahead of market demands.
Furthermore, creating a culture of continuous improvement is fundamental for operational excellence. By ingraining a mindset of constantly seeking better ways to do things, organizations can adapt swiftly to changes, optimize performance, and deliver exceptional customer experiences.
Implementing continuous improvement practices can lead to increased operational efficiency by identifying and eliminating waste in processes, leading to cost savings and resource optimization.
Key Benefits of Continuous Improvement
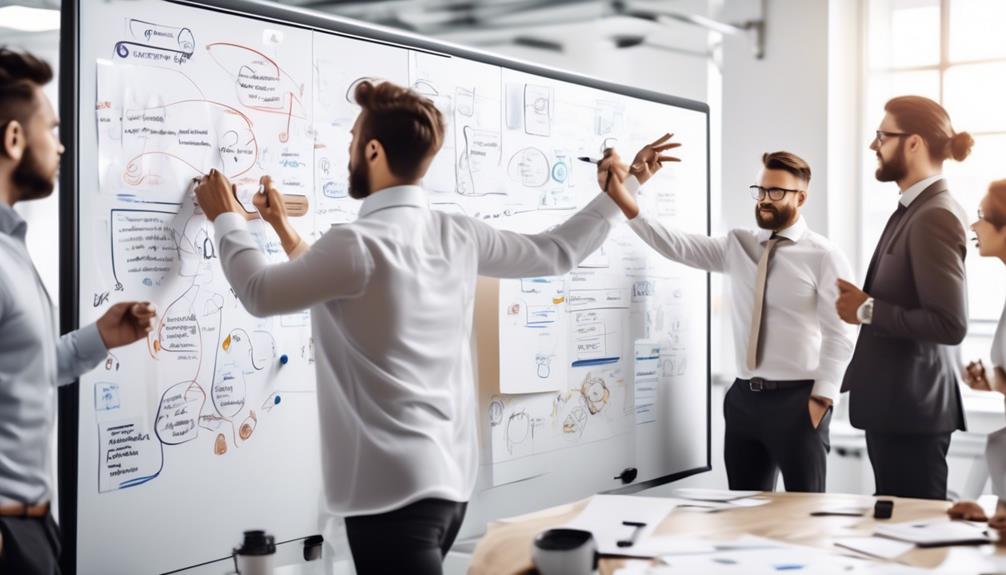
Continuous improvement in QA offers a multitude of benefits.
Improved processes lead to greater efficiency and productivity, while enhanced quality translates to higher customer satisfaction and loyalty.
Additionally, continuous improvement fosters team engagement, leading to a more motivated and innovative workforce.
Improved Processes
Enhanced operational efficiency and cost savings are key benefits of continuous improvement. This includes improved resource utilization and streamlined workflows. Process improvement plays a pivotal role in achieving these benefits.
By analyzing and refining existing processes, organizations can identify inefficiencies and implement changes to optimize workflows. This leads to reduced waste, quicker turnaround times, and improved overall productivity.
Furthermore, process improvement contributes to increased product quality and customer satisfaction. It ensures that operations are aligned with customer needs and market demands. It also fosters a culture of continuous learning and innovation, empowering employees to contribute to the refinement of processes.
Ultimately, these improvements provide a competitive advantage. They allow organizations to adapt to market changes, drive long-term growth, and sustain relevance in dynamic business environments.
Enhanced Quality
After optimizing workflows through process improvement, the focus shifts to the key benefits of continuous improvement, particularly the enhancement of quality. Continuous improvement allows us to systematically address the root causes of quality issues, leading to a more robust and reliable product or service.
By identifying and rectifying these root causes, we not only improve the current quality but also prevent similar issues from arising in the future. This proactive approach not only enhances the customer experience but also reduces the cost of poor quality, ultimately contributing to higher levels of customer satisfaction and loyalty.
Moreover, a focus on enhanced quality through continuous improvement aligns with the organization’s strategic objectives, positioning it as a leader in the industry and fostering a culture of excellence.
Team Engagement
To maximize the benefits of continuous improvement, our team engagement plays a pivotal role in driving the strategic objectives of our organization and fostering a culture of excellence. Active participation and collaboration within the team are essential for the success of any improvement initiative. Here is a table highlighting the key factors that contribute to effective team engagement in the context of continuous improvement:
Key Factors for Effective Team Engagement |
---|
Clear Communication |
Empowerment and Accountability |
Recognition and Rewards |
Training and Development |
Collaboration and Team Building |
These factors are vital in ensuring that the team is fully engaged and committed to the continuous improvement process. By prioritizing team engagement, organizations can harness the collective expertise and motivation of their employees to drive meaningful and sustainable improvements in quality and productivity.
Effective Continuous Improvement Methods
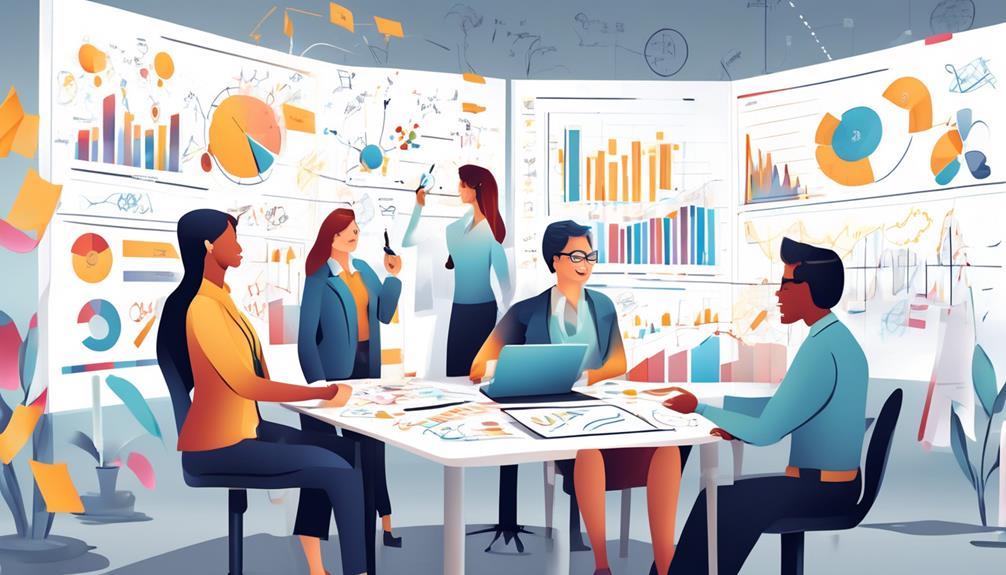
Customizing how and where continuous improvement is applied can significantly enhance its effectiveness in meeting the specific needs and objectives of an organization. To ensure the successful implementation of continuous improvement processes, it’s crucial to assess the impact on company culture.
This involves considering national, corporate, and personal cultures involved, as they play a pivotal role in shaping the receptiveness and effectiveness of these methods. Furthermore, training employees on continuous improvement tools and problem-solving skills is essential for fostering a culture of continuous improvement and leadership development.
Integrating data analytics and artificial intelligence can further enhance continuous improvement processes, enabling organizations to stay competitive in evolving business landscapes.
To foster a culture of continuous improvement, regular evaluation and monitoring of improvement initiatives are imperative for long-term success. This involves establishing mechanisms for feedback and review to identify areas for refinement and optimization.
Implementing a Continuous Improvement Approach
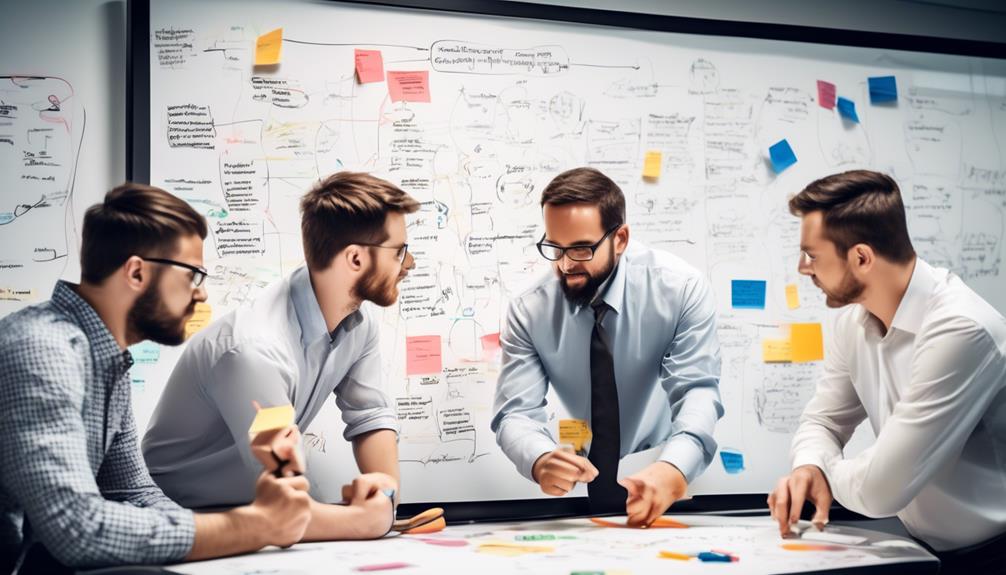
As we pivot to discuss implementing a continuous improvement approach in QA, it’s essential to address the key points of agile QA processes, metrics for improvement, and team collaboration.
By focusing on agile processes, we can adapt quickly to changes and deliver high-quality products consistently.
Metrics for improvement will allow us to measure our progress and make data-driven decisions.
Fostering team collaboration will ensure that everyone is aligned and contributing to the continuous improvement efforts.
Agile QA Processes
Agile QA processes, with their emphasis on flexibility and adaptability, are essential for implementing a continuous improvement approach in modern software development practices. By embracing Agile methodologies, organizations can respond to changes and deliver high-quality products efficiently. According to the Harvard Business Review, aligning continuous improvement with strategic goals and effective leadership is crucial for success. Continuous improvement is not a one-time project but an ongoing journey, requiring organizations to adapt to evolving business landscapes. To illustrate the significance of Agile QA processes in continuous improvement, we’ve outlined a comparison in the table below:
Traditional QA Processes | Agile QA Processes | Continuous Improvement |
---|---|---|
Sequential approach | Iterative approach | Ongoing adaptation |
Fixed requirements | Embraces change | Aligns with strategic goals |
Siloed teams | Cross-functional teams | Leadership support essential |
Long feedback loops | Continuous feedback | Flexibility and adaptability |
Waterfall methodology | Scrum/Kanban methodology | Embraces innovation and flexibility |
Metrics for Improvement
To measure the effectiveness of continuous improvement in QA processes, organizations can establish and analyze key performance metrics that align with strategic objectives and drive tangible progress. When selecting Key Performance Indicators (KPIs) for QA continuous improvement, it’s crucial to focus on metrics that directly impact quality, efficiency, and customer satisfaction.
Here are essential KPIs to consider:
- Defect Density: This metric measures the number of defects identified per deliverable, providing insights into the quality of the product and the effectiveness of the QA process.
- Test Case Effectiveness: Evaluating the percentage of test cases that identify defects helps gauge the thoroughness and accuracy of testing efforts.
- Mean Time to Detect (MTTD) and Mean Time to Resolve (MTTR): These metrics assess how quickly defects are identified and resolved, indicating the efficiency of the QA process.
- Customer Satisfaction Score: Feedback from end-users provides valuable insights into the overall quality and effectiveness of the product from a user perspective.
Team Collaboration
Transitioning from metrics for improvement to team collaboration in implementing a continuous improvement approach requires fostering a culture of curiosity and embracing smart risks to encourage effective collaboration within the QA process. Encouraging teams to challenge existing practices and think outside the box is essential for continuous improvement efforts.
It’s crucial to look for opportunities to introduce creativity and innovation into improvement processes through team collaboration. Effective leadership is vital to provide support and resources for team collaboration in continuous improvement initiatives.
Emphasizing the importance of ongoing collaboration and empowerment of employees in continuous improvement is key for long-term success. By fostering a collaborative environment that values curiosity, smart risk-taking, and innovation, teams can work together to drive meaningful and sustainable improvements in the QA process.
Tools for Continuous Improvement in QA
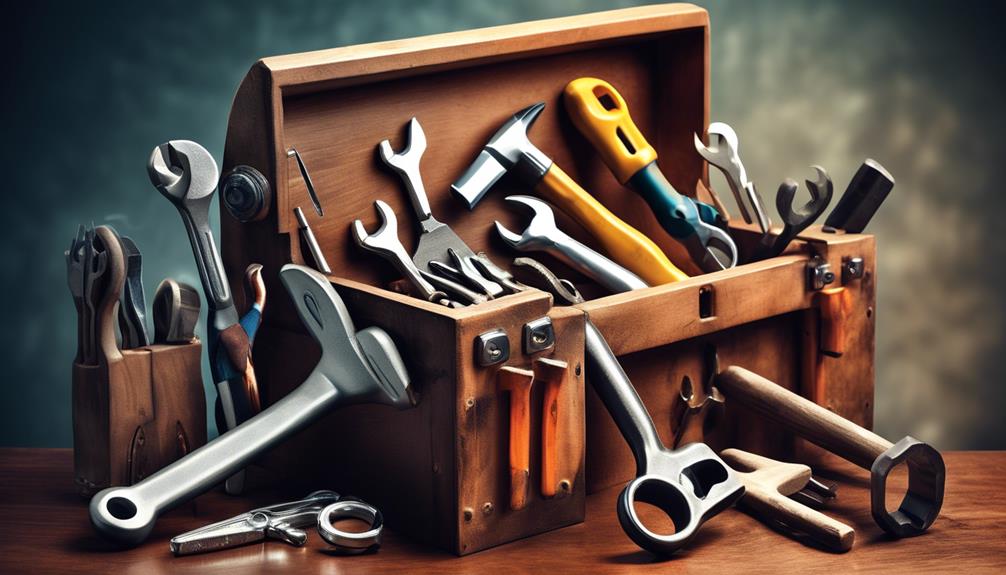
In our pursuit of continuous improvement in QA, it’s essential to explore and leverage a diverse array of tools and methodologies to enhance our quality assurance processes. Here are some key tools for continuous improvement in QA:
- Quality Management Systems (QMS): Implementing a robust QMS can streamline processes, track quality metrics, and provide insights for continuous improvement initiatives.
- Test Automation Tools: Leveraging advanced test automation tools can enhance efficiency, increase test coverage, and improve the accuracy and reliability of QA processes.
- Data Analytics and Business Intelligence Tools: Utilizing data analytics and business intelligence tools can provide valuable insights into QA performance, enabling data-driven decision-making for continuous improvement.
- Collaboration and Communication Platforms: Effective communication and collaboration platforms can facilitate knowledge sharing, problem-solving, and cross-functional collaboration, fostering a culture of continuous improvement within the QA team.
Tips for Successful Continuous Improvement
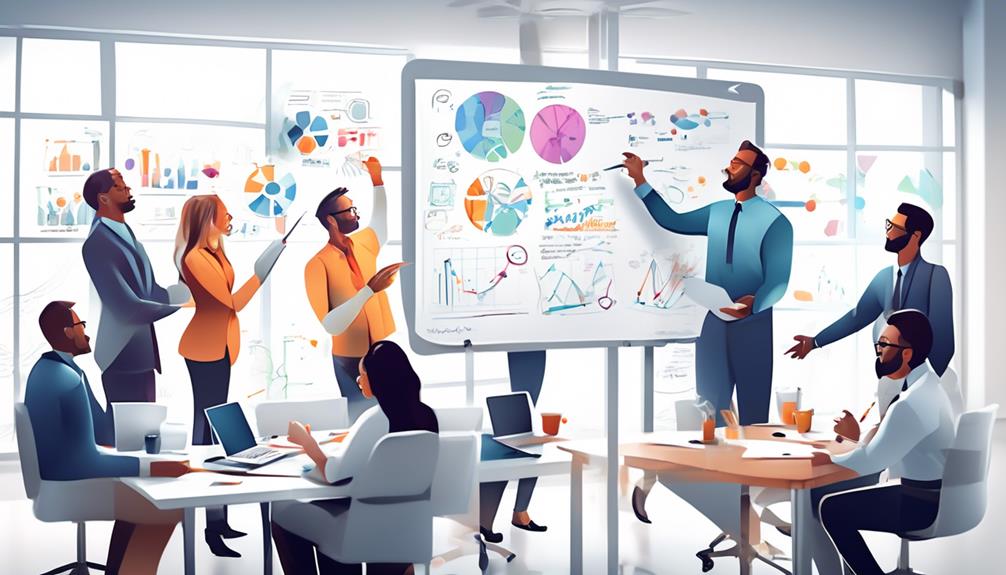
Embracing innovative approaches to continuous improvement can significantly enhance the effectiveness of quality assurance processes. To achieve successful continuous improvement, it’s crucial to regularly analyze the impact of these strategies on the organization. Effective leadership plays a pivotal role in driving continuous improvement initiatives, ensuring that they align with the organization’s goals and values. As continuous improvement evolves to adapt to changing business landscapes, customizing how and where these methods are applied can lead to more nuanced and effective outcomes. It’s essential to consider the specific needs and challenges of the organization in order to tailor continuous improvement efforts for maximum impact.
To ensure successful continuous improvement, organizations should foster a culture that encourages open communication, collaboration, and a willingness to embrace change. Additionally, leveraging technology and data-driven insights can provide valuable support for continuous improvement initiatives. This includes utilizing advanced analytics to identify areas for improvement and measure the impact of implemented changes. By continuously refining and optimizing these approaches, organizations can achieve sustained success through their continuous improvement efforts.
Frequently Asked Questions
Why Is Continuous Improvement Necessary in a Quality System?
Continuous improvement is necessary in a quality system because it allows us to adapt to changing needs, enhance efficiency, and maintain high standards. By continually evaluating and refining our processes, we can identify areas for improvement and implement proactive solutions.
This approach fosters a culture of excellence, aligning with our strategic goals and ensuring that we remain at the forefront of quality and innovation.
What Is Continuous Improvement in Qa?
Continuous improvement in QA involves constantly enhancing processes, tools, and methodologies to ensure optimal quality. It’s a mindset and approach that focuses on making small, incremental improvements over time.
The goal is to continually enhance efficiency, effectiveness, and overall quality. It requires ongoing evaluation, feedback, and adaptation to maintain high standards.
Continuous improvement in QA supports a culture of innovation, learning, and adaptability to deliver exceptional results.
What Are the 5 Key Principles of Continuous Improvement?
The 5 key principles of continuous improvement are:
- A progressive approach to positive changes, fostering commitment and best practices
- An organizational culture focused on learning and adapting
- Implementing the PDCA cycle for a continuous improvement loop
- Encouraging employee participation and commitment
- Regularly analyzing results and trends to adjust strategy
These principles align methods to company needs and objectives, remove barriers between different levels of the organization, and help overcome challenges.
What Is the End Goal of Quality Improvement and Continuous Improvement?
Our end goal is to drive innovation and long-term growth through quality and continuous improvement.
It involves creating a culture of learning and adaptation, aiming to improve operational efficiency, quality, and delivery.
This leads to a competitive advantage and operational excellence.
Conclusion
In conclusion, rethinking QA continuous improvement tactics is like planting a garden.
Just as we carefully select the right seeds, nurture the soil, and tend to the plants, we must also continuously evaluate and adapt our improvement methods.
By embracing innovation, fostering a culture of curiosity, and balancing risk-taking with strategic goals, we can cultivate a thriving and resilient quality assurance process that yields bountiful results.
Randy serves as our Software Quality Assurance Expert, bringing to the table a rich tapestry of industry experiences gathered over 15 years with various renowned tech companies. His deep understanding of the intricate aspects and the evolving challenges in SQA is unparalleled. At EarnQA, Randy’s contributions extend well beyond developing courses; he is a mentor to students and a leader of webinars, sharing valuable insights and hands-on experiences that greatly enhance our educational programs.