We have all experienced the disappointment of receiving a product that does not meet our expectations, such as a smartphone with technical problems or a car that constantly needs repairs. These situations underscore the significance of improving quality.
Six Sigma, with its focus on reducing defects and enhancing customer satisfaction, serves as a powerful tool in this pursuit. But what exactly is Six Sigma and how does it work?
Let’s explore its role in driving quality improvement and why it’s become a staple in the arsenal of successful organizations.
Key Takeaways
- Six Sigma is a quality improvement methodology focused on reducing defects and variations in processes.
- The DMAIC roadmap guides the team through the Define, Measure, Analyze, Improve, and Control stages of the process.
- Data and statistical methods are used to make informed decisions and improve efficiency.
- Successful implementation of Six Sigma in healthcare can lead to improvements in patient care, operational efficiency, and financial benefits.
Understanding Six Sigma’s Principles
Using the DMAIC roadmap, a team of experts employs specific methodologies to improve processes as part of the project-based model of Six Sigma. Six Sigma is a quality improvement methodology that focuses on reducing defects and variations in processes. It provides a structured approach to problem-solving and process improvement, with the goal of enhancing customer satisfaction and eliminating waste.
The DMAIC roadmap—Define, Measure, Analyze, Improve, and Control—guides the team through the process, emphasizing the use of data and statistical methods to make informed decisions.
One of the core principles of Six Sigma is its emphasis on data-driven decision making. By analyzing and understanding the variation in work processes, organizations can identify areas for improvement and implement targeted solutions. This approach enables organizations to make informed decisions based on evidence rather than intuition, leading to more effective and sustainable improvements.
Key Methodologies of Six Sigma
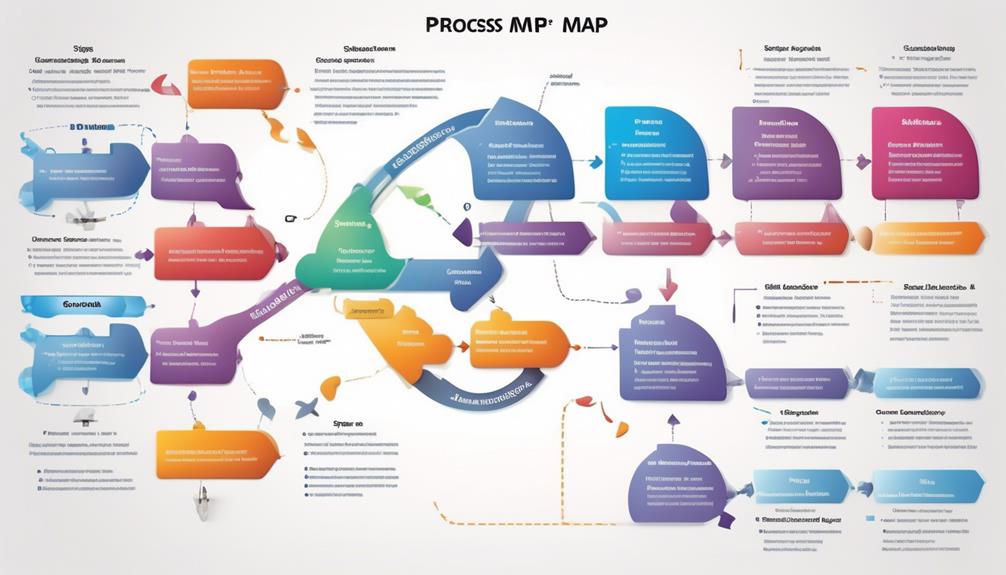
Let’s start by discussing the key methodologies of Six Sigma.
These include Six Sigma Basics, the DMAIC process, and quality measurement.
Understanding these methodologies is crucial for implementing Six Sigma effectively and achieving quality improvement.
Six Sigma Basics
Six Sigma, as a methodology for quality improvement, encompasses key methodologies such as the DMAIC roadmap, which guides teams through the process of identifying and addressing issues using data and statistical methods. Six Sigma provides protocols and tools for problem-solving and process improvement. It is a project-based model used to improve discrete processes. The approach focuses on understanding and controlling variation in work processes and is resource-intensive, requiring trained improvement team members. Healthcare organizations have successfully utilized Six Sigma to enhance patient care, reduce medical errors, and improve operational efficiency. Additionally, Lean Six Sigma, an extension of Six Sigma principles, integrates lean manufacturing techniques with Six Sigma to eliminate waste and improve processes. The table below summarizes the key methodologies of Six Sigma.
Methodology | Description |
---|---|
DMAIC | A roadmap for defining, measuring, analyzing, improving, and controlling processes to resolve problems. |
Lean Six Sigma | Integrates lean manufacturing techniques with Six Sigma to eliminate waste and improve processes. |
DMADV | A roadmap for defining, measuring, analyzing, designing, and verifying new processes and products. |
IDOV | A roadmap for identifying, designing, optimizing, and verifying new processes for quality improvement projects. |
DMAIC Process
The DMAIC process, a fundamental methodology of Six Sigma, encompasses a structured approach to process improvement, involving distinct stages from defining project goals to establishing baseline performance and identifying areas for enhancement.
The acronym DMAIC represents the stages of Define, Measure, Analyze, Improve, and Control.
In the Define stage, project goals and deliverables are clearly outlined.
The Measure stage focuses on collecting relevant data to establish baseline performance.
Analysis in the DMAIC process involves identifying root causes and areas for improvement.
The Improve stage aims to develop and implement solutions to address the identified areas for enhancement.
Lastly, the Control stage ensures that the improvements are sustained over time.
The DMAIC approach is pivotal in guiding improvement projects within the Six Sigma framework, providing a systematic and data-driven method for achieving quality enhancement.
Quality Measurement
Utilizing statistical tools and a data-driven framework, Six Sigma’s quality measurement methodologies aim to reduce defects, enhance process efficiency, and improve customer satisfaction.
By employing methodologies such as control charts, Pareto charts, and regression analysis, Six Sigma enables organizations to measure and analyze process improvements effectively.
In healthcare organizations, Six Sigma methodology plays a crucial role in improving patient care and reducing costs. It emphasizes the identification and control of variations in work processes, ultimately leading to waste reduction and enhanced overall process efficiency.
Successful implementation of Six Sigma quality measurement methodologies can result in significant improvements in quality, customer satisfaction, and financial benefits for organizations across various industries, including healthcare.
Project Selection in Six Sigma
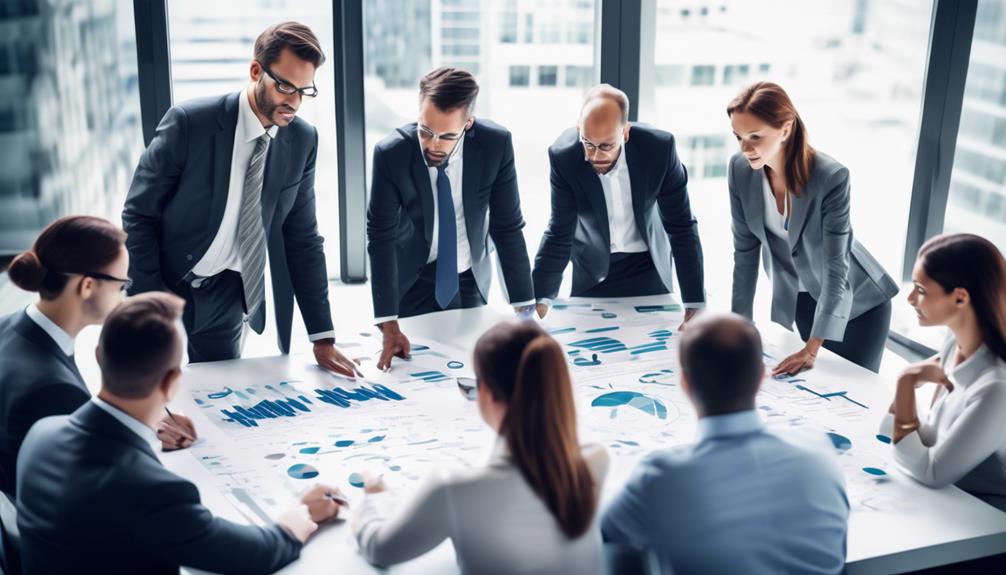
When selecting projects in Six Sigma, we must carefully consider the project prioritization methods and criteria for selection.
This involves analyzing the potential impact on process improvement, customer satisfaction, cost reduction, and overall efficiency.
The chosen projects should align with organizational goals and have the potential to yield significant results.
Project Prioritization Methods
In Six Sigma, selecting projects for improvement involves employing prioritization methods that assess potential impact, resource requirements, and alignment with organizational goals. When considering project prioritization methods, healthcare organizations often use:
- Cost-benefit analysis: This method evaluates the potential return on investment of each project, helping to prioritize those with the highest potential impact on quality improvement.
- Impact effort matrix: By categorizing projects based on their potential impact and the effort required, this method aids in identifying projects that align with strategic objectives and have a high probability of success.
- Resource availability assessment: Considering the availability of resources, such as personnel, time, and budget, ensures that selected projects are feasible and can be executed effectively within the organization.
These methods are crucial for healthcare organizations in prioritizing projects that will yield the greatest impact on quality improvement within a Six Sigma framework.
Criteria for Project Selection
Selecting projects in Six Sigma involves a rigorous evaluation process to ensure alignment with organizational goals and the potential to drive significant improvements in key performance indicators. In the context of quality improvement, project selection is crucial for healthcare organizations aiming to enhance patient care and operational efficiency.
Projects should be data-driven, with a focus on clear metrics for success and measurable improvements. Furthermore, prioritizing projects that address critical customer needs can significantly enhance customer satisfaction. Cross-functional involvement is essential, as it can demonstrate the effectiveness of Six Sigma methodologies and ensure comprehensive problem-solving.
Additionally, emphasis should be placed on selecting projects with the potential for sustainable, long-term impact on process efficiency and operational excellence. By adhering to these criteria, healthcare organizations can maximize the benefits of implementing Six Sigma and drive continuous quality improvement.
Impact on Process Improvement
Project selection in Six Sigma plays a pivotal role in driving process improvement by strategically aligning initiatives with organizational goals and prioritizing areas with the highest potential for quality and efficiency enhancements.
Utilizing a data-driven approach, Six Sigma identifies key performance indicators to pinpoint areas for improvement.
Analyzing data aids in prioritizing projects based on their potential impact on quality and efficiency.
Effective project selection ensures that resources are allocated to initiatives that will yield the most significant benefits, contributing to overall process improvement.
Roles in Six Sigma Implementation
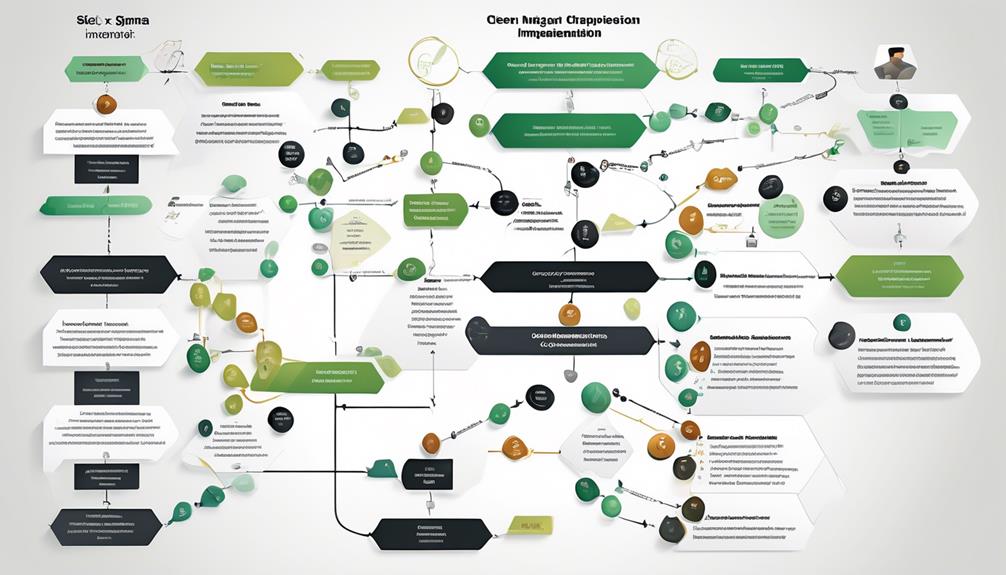
When implementing Six Sigma, executive leadership provides overall strategic direction and support for Six Sigma initiatives within the organization. Champions play a crucial role in ensuring that projects align with the organization’s goals and provide the necessary resources and support to the project teams. They act as advocates for Six Sigma, promoting its benefits and driving cultural change within the organization.
Additionally, Master Black Belts, as experts in Six Sigma methodologies, provide guidance, training, and mentorship to Black Belts and Green Belts, ensuring the effective application of Six Sigma tools and techniques. Black Belts are instrumental in leading and managing Six Sigma projects full-time, utilizing statistical analysis and process improvement tools to achieve project goals.
Similarly, Green Belts, while working on Six Sigma projects part-time, apply process improvement tools within their functional areas and provide valuable support to Black Belt-led projects. In healthcare organizations, the roles within Six Sigma implementation are essential for driving quality improvement initiatives and ensuring effective management of process improvement projects.
Importance of Six Sigma in Healthcare

Six Sigma’s pivotal role in driving quality improvement initiatives in healthcare becomes evident when considering its ability to increase process capability, reduce errors, and improve patient care and satisfaction.
In healthcare, Six Sigma is crucial for increasing process capability and efficiency while focusing on patient safety, satisfaction, waste reduction, and cost savings. The implementation of Six Sigma in healthcare can streamline processes, reduce errors, and enhance patient care and satisfaction.
Additionally, Lean Six Sigma, which combines Lean and Six Sigma methodologies, is essential in healthcare to improve efficiency, reduce variability, and integrate quality improvement.
The DMAIC approach plays a crucial role in problem-solving and quality improvement in healthcare, ensuring safer patient care, faster service delivery, and improved coordination.
Furthermore, Six Sigma’s data-driven approach can result in measurable improvement in healthcare, reducing errors, improving patient outcomes, and increasing efficiency.
This comprehensive approach to improvement in healthcare underscores the significance of Six Sigma in enhancing patient care and satisfaction.
Application of Six Sigma in Healthcare

Applying Six Sigma in healthcare settings involves a comprehensive approach to increasing process capability, improving patient safety, and enhancing overall satisfaction. Healthcare organizations can benefit from the application of Six Sigma by reducing defects and medical errors, ultimately leading to improved quality of care. The table below outlines the key benefits and applications of Six Sigma in healthcare:
Benefits of Six Sigma in Healthcare | Applications of Six Sigma in Healthcare |
---|---|
– Reducing medical errors | – Streamlining patient discharge processes |
– Improving patient satisfaction | – Enhancing medication administration processes |
– Lowering healthcare costs | – Optimizing inventory management for medical supplies |
These applications demonstrate how Six Sigma methodologies can be utilized to address specific challenges within healthcare organizations, ultimately leading to improved patient outcomes and operational efficiency. By leveraging data-driven decision-making and process improvement techniques, healthcare providers can effectively enhance the quality of care while simultaneously reducing costs and increasing patient satisfaction.
Quality Improvement Steps in Six Sigma

As we examine the quality improvement steps in Six Sigma, it’s important to highlight the DMAIC methodology, which serves as a structured approach for problem-solving and process improvement.
Understanding and controlling process variation is a key focus, as this allows for the identification and elimination of waste while improving customer satisfaction.
The data-driven decisions made throughout the DMAIC roadmap guide teams in developing effective protocols and tools for addressing issues.
DMAIC Methodology
Utilizing the DMAIC methodology in Six Sigma enables organizations to systematically define, measure, analyze, improve, and control their processes to achieve significant quality improvements.
The Define stage involves identifying the problem, its scope, and setting clear project objectives for improvement.
In the Measure stage, data is collected and analyzed to quantify the problem and its impact on processes.
The Analyze stage utilizes statistical methods to identify the root causes of the problem and understand process variations.
Subsequently, in the Improve stage, solutions are developed and implemented to address the root causes and improve the process.
Finally, the Control stage establishes monitoring systems to ensure that the improvements are sustained and continue to meet desired goals.
This systematic approach is especially beneficial for healthcare organizations seeking to enhance their quality improvement efforts.
Process Variation
Process variation, a central focus in Six Sigma methodology, involves identifying and controlling sources of inconsistency to enhance quality and reduce defects. This encompasses addressing variations in materials, methods, machines, manpower, measurement, and environmental factors.
In healthcare organizations, process variation can lead to inefficiencies, medical errors, and compromised patient safety. By implementing Six Sigma strategies, such as the DMAIC roadmap, organizations can systematically analyze and mitigate process variations.
The define, measure, and analyze phases allow for the identification of sources of variation and the development of effective solutions. Knowledge transfer is essential for successful implementation, ensuring that responsible workers understand and sustain the improvements.
Ultimately, addressing process variation in healthcare organizations through Six Sigma methodologies contributes to enhanced quality, reduced costs, and improved patient outcomes.
Data-Driven Decisions
Quality improvement steps in Six Sigma are driven by the use of statistical analysis and relevant data to guide decision-making.
- Data-driven decisions ensure that improvements are based on measurable and quantifiable data, enhancing quality effectively.
- The use of statistical methods and tools in Six Sigma leads to a data-driven approach, identifying and addressing issues using relevant data.
- The DMAIC roadmap, a central tool in Six Sigma, guides teams through data-driven decision-making and statistical methods to improve quality.
Data-Driven Decision Making in Six Sigma
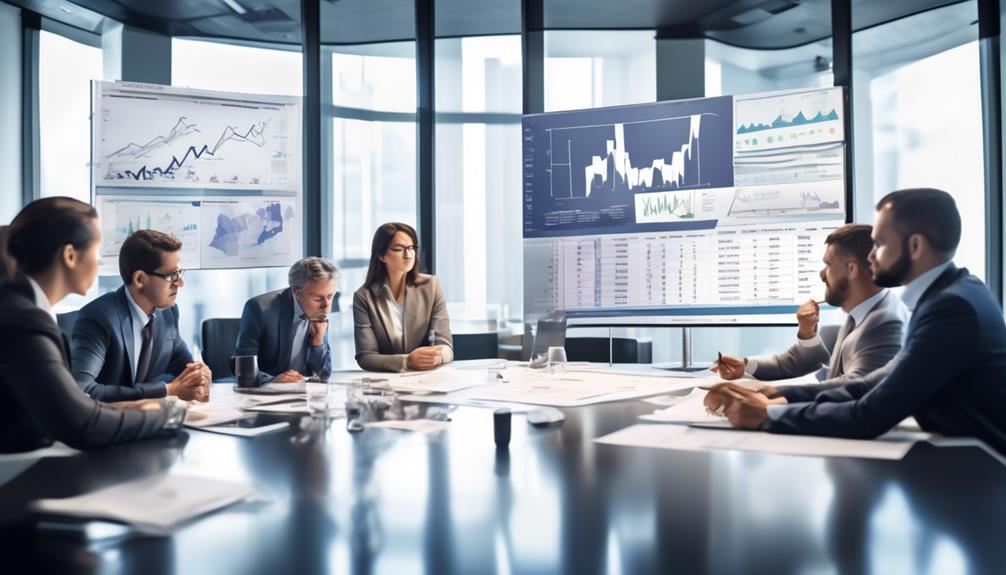
Emphasizing the use of statistical methods and data analysis, Six Sigma’s approach to decision making significantly contributes to process improvement. In the healthcare sector, this data-driven decision making is crucial for achieving and maintaining high-quality patient care and operational efficiency. The DMAIC roadmap guides teams through the process of identifying and addressing issues using data and statistical methods. It focuses on understanding and controlling variation in work processes through the six Ms: materials, method, machines, manpower, measurement, and mother nature. Solutions are developed during the define, measure, and analyze phases of the DMAIC roadmap, and are rigorously tested under various conditions. Successful strategies implemented in one project become the basis for future improvement work, relying on the expertise of individuals trained in Six Sigma. The following table demonstrates the key stages of the DMAIC roadmap and their role in data-driven decision making.
DMAIC Stage | Description | Data-Driven Decision Making |
---|---|---|
Define | Clearly outline the problem, goals, and deliverables of the project. | Use data to prioritize improvement opportunities and set specific, measurable, achievable, relevant, and time-bound (SMART) goals. |
Measure | Quantify the current state of the process, collect relevant data, and establish process capability. | Use statistical tools to analyze data and establish baseline performance metrics. |
Analyze | Identify the root causes of process issues and develop solutions. | Leverage data analysis to identify patterns, trends, and root causes of variation within the process. |
Improve | Implement and verify solutions that address the root causes of process issues. | Validate the effectiveness of solutions through data analysis and pilot testing before full implementation. |
Successful Six Sigma Examples in Healthcare
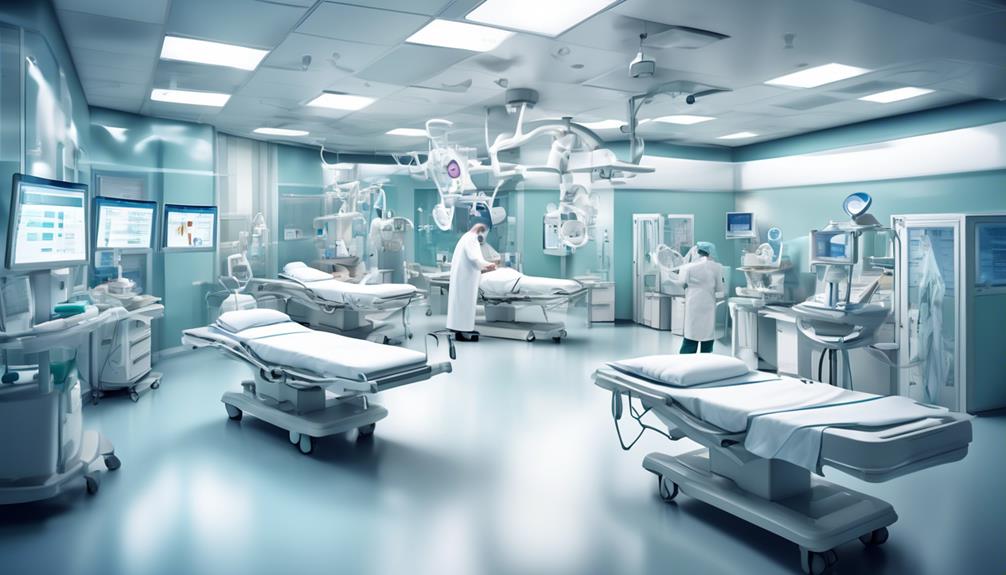
In Izmir, Turkey, a private hospital effectively doubled its patient treating capacity to 64 patients per day by implementing the Six Sigma methodology. This success was achieved through streamlining patient flow. By optimizing processes, the hospital was able to efficiently manage patient intake, treatment, and discharge, resulting in a significant increase in daily patient capacity.
Another factor in the hospital’s success was enhancing resource utilization. Six Sigma tools allowed the hospital to identify and eliminate waste, leading to better utilization of resources such as staff, equipment, and facilities, without compromising on patient care.
Additionally, improving staff productivity played a crucial role. Through the implementation of Six Sigma, the hospital was able to enhance staff productivity, ensuring that all resources were effectively utilized to cater to the increased patient load.
These examples underline the potential of Six Sigma in healthcare organizations to reduce costs, improve patient outcomes, and enhance overall operational efficiency. These successes demonstrate the adaptability of Six Sigma in addressing diverse challenges within the healthcare sector, from enhancing patient experience to optimizing resource management.
Impact of Six Sigma in Healthcare
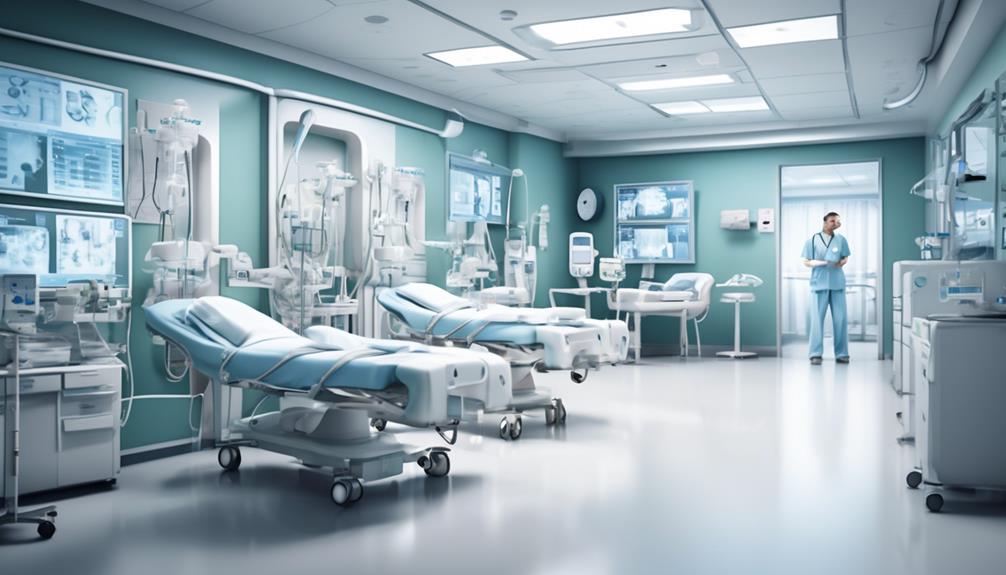
After successfully doubling its patient treating capacity through the implementation of Six Sigma, a private hospital in Izmir, Turkey exemplified the substantial impact of this methodology in healthcare.
Six Sigma has been instrumental in driving significant improvements in healthcare organizations. By reducing waste, eliminating defects, and streamlining processes, Six Sigma helps healthcare organizations to reduce costs while delivering effective and efficient services.
The combination of Lean and Six Sigma methodologies, known as Lean Six Sigma, has proven to be particularly effective in healthcare, as it can significantly reduce medical errors, improve efficiency, and enhance patient satisfaction.
The DMAIC approach of Six Sigma plays a crucial role in problem-solving and quality improvement in healthcare, ensuring safer patient care and faster service delivery.
Successful examples of Six Sigma implementation in healthcare include not only doubling patient treating capacity but also reducing patient waiting time and achieving significant cost savings.
Benefits of Six Sigma in Healthcare
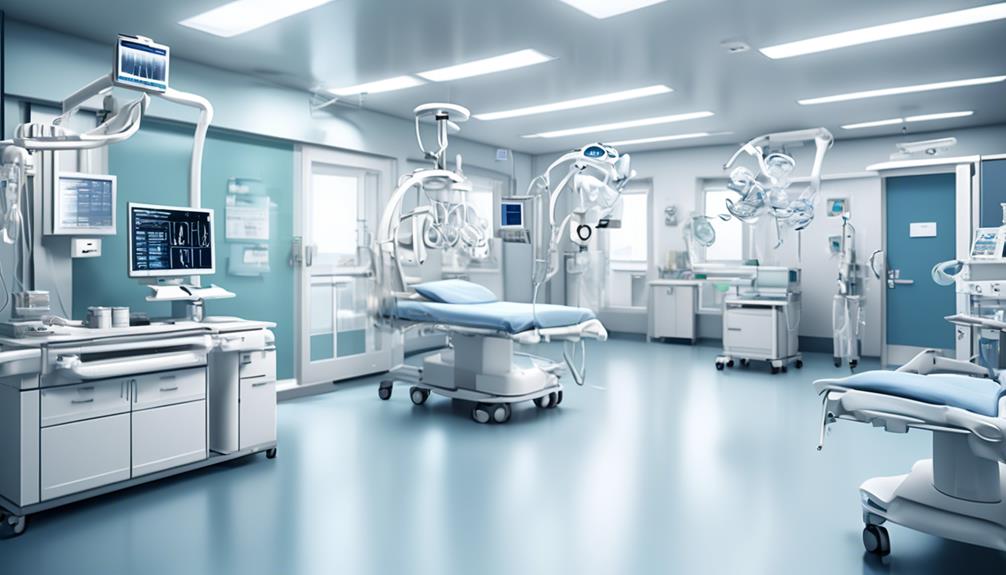
How does Six Sigma contribute to reducing waste and eliminating defects in healthcare processes, ultimately leading to improved patient safety and satisfaction?
Six Sigma in healthcare offers various benefits, including:
- Streamlined Processes: Implementing Six Sigma in healthcare organizations can streamline processes and reduce costs, resulting in more effective and efficient healthcare services. This leads to improved patient care and satisfaction as resources are utilized more efficiently.
- Enhanced Productivity: Integrating Lean with Six Sigma in healthcare boosts productivity, reduces variability, and significantly improves patient satisfaction. This ensures that healthcare providers can deliver high-quality care in a timely manner.
- Cost Savings: Six Sigma in healthcare has been shown to significantly impact healthcare management, operations, and direct patient care, leading to reduced errors, improved patient outcomes, and substantial cost savings. This allows healthcare organizations to allocate resources strategically and focus on delivering value-driven care.
The application of Six Sigma methodologies in healthcare not only enhances quality improvement efforts but also contributes to reducing costs, improving patient safety, and ultimately enhancing the overall healthcare experience.
Lean Six Sigma Certification and Training
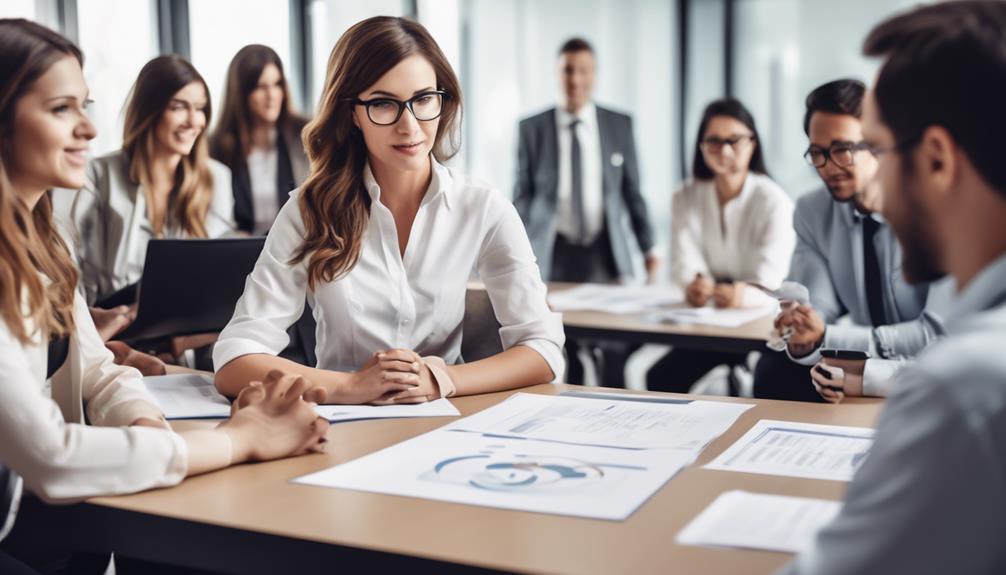
Lean Six Sigma Certification and Training equips professionals with the essential tools and methodologies to drive process improvement and organizational efficiency. Combining the principles of Six Sigma and Lean methodology, this training focuses on reducing waste, defects, and variance, while enhancing overall efficiency.
Certification in Lean Six Sigma typically involves different levels, such as green belts, black belts, and master black belts, each with varying degrees of expertise in implementing quality improvement projects. These certifications are offered by reputable organizations and demonstrate a deep understanding of the methodologies and tools essential for successful quality improvement initiatives.
Training in Lean Six Sigma encompasses a comprehensive curriculum, including modules on the DMAIC and DMADV methodologies, statistical analysis, process mapping, root cause analysis, and design of experiments. This equips professionals with the knowledge and skills required to lead and contribute to quality improvement projects within their organizations.
The application of Lean Six Sigma principles has led to significant improvements in quality, customer satisfaction, productivity, and cost savings across diverse industries, making this certification an invaluable asset for professionals seeking to drive impactful change and achieve operational excellence.
Advancing Career With Lean Six Sigma
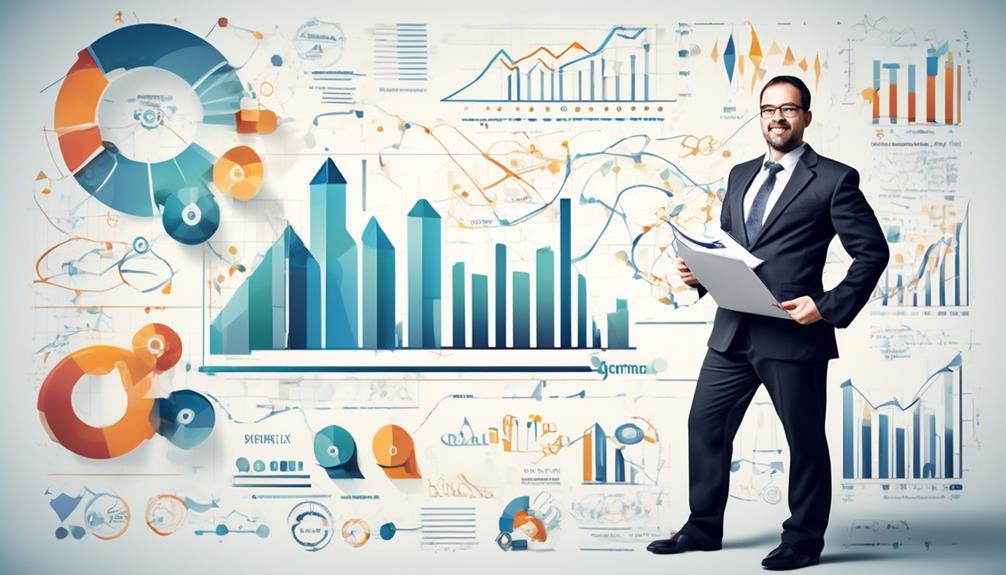
To further our professional development, we can leverage Lean Six Sigma to advance our careers and drive impactful change within our organizations.
By obtaining Lean Six Sigma certification, we open doors to a wide array of career opportunities and demonstrate our commitment to quality improvement and data-driven decision-making. This certification equips us with the knowledge and skills to lead process improvement initiatives, reduce defects, and enhance overall efficiency.
As Lean Six Sigma practitioners, we can become instrumental in driving organizational change and delivering substantial bottom-line results. Additionally, we can pursue roles such as Lean Six Sigma project manager, process improvement specialist, or quality assurance manager, where we can apply our expertise to streamline operations and elevate performance.
Furthermore, with Lean Six Sigma proficiency, we can stand out in the job market, command higher salaries, and be sought after by employers who prioritize continuous improvement and operational excellence.
Embracing Lean Six Sigma isn’t just a career move; it’s a strategic decision to become a catalyst for positive transformation in our professional journey.
Frequently Asked Questions
What Is the Six Sigma Rule in Quality Management?
We believe that the Six Sigma rule in quality management is crucial for achieving excellence.
By integrating data and statistics, it enables us to identify and eliminate variations in processes, leading to improved quality, higher customer satisfaction, and reduced defects and waste.
This approach, through methodologies like DMAIC and DMADV, helps us in continuously enhancing efficiency, productivity, and decision-making based on thorough data analysis.
How Is the Six Sigma Process Used in Addressing Quality Improvement Challenges in Healthcare?
In healthcare, the Six Sigma process addresses quality improvement challenges by providing a structured approach for problem-solving. We use data-driven methods to enhance patient safety, satisfaction, and operational efficiency.
What Is the Role of the Six Sigma Concept?
Six Sigma concept plays a pivotal role in quality improvement. It enables us to identify and eliminate defects, streamline processes, and reduce variation. By integrating data and statistics, we can make informed decisions to enhance quality.
Lean Six Sigma further focuses on minimizing waste and defects. The methodologies like DMAIC and DMADV provide structured frameworks for continuous improvement.
How Does Six Sigma 6 Improve the Quality of Output?
Improving the quality of output is central to Six Sigma. We use data-driven methods to identify and address issues, reducing defects and waste. By understanding and controlling variation in work processes, we enhance customer satisfaction and efficiency.
Our approach emphasizes the define, measure, and analyze phases to implement effective solutions. Successful implementation leads to improved quality, customer satisfaction, and cost savings.
Conclusion
In conclusion, Six Sigma’s strong principles and key methodologies play a pivotal role in quality improvement. Its impact and importance in healthcare are undeniable, bringing about benefits such as improved efficiency, cost savings, and enhanced patient satisfaction.
With Lean Six Sigma certification and training, professionals can advance their careers and contribute to the systematic success of organizations. Embracing Six Sigma is an effective and efficient way to elevate excellence in any industry.
Randy serves as our Software Quality Assurance Expert, bringing to the table a rich tapestry of industry experiences gathered over 15 years with various renowned tech companies. His deep understanding of the intricate aspects and the evolving challenges in SQA is unparalleled. At EarnQA, Randy’s contributions extend well beyond developing courses; he is a mentor to students and a leader of webinars, sharing valuable insights and hands-on experiences that greatly enhance our educational programs.