Predictive quality analytics uses real-time sensor data to spot potential defects early in the manufacturing process. By monitoring variables like temperature, pressure, and humidity, you can identify patterns and anomalies before problems escalate. Advanced models analyze both current and historical data to forecast issues, allowing you to take preventive actions. This proactive approach helps improve product quality and reduce costs. Keep exploring to discover how these techniques can transform your quality management strategy.
Key Takeaways
- Sensor data integration enables real-time monitoring to detect potential defects early in the manufacturing process.
- Data visualization tools quickly identify patterns and anomalies indicating possible quality issues before defects occur.
- Continuous feedback and predictive models forecast future defects, allowing proactive interventions.
- Predictive analytics reduce rework, scrap, and operational costs by addressing issues before they manifest as defects.
- Shifting from reactive to preventive quality management enhances product consistency and customer satisfaction.
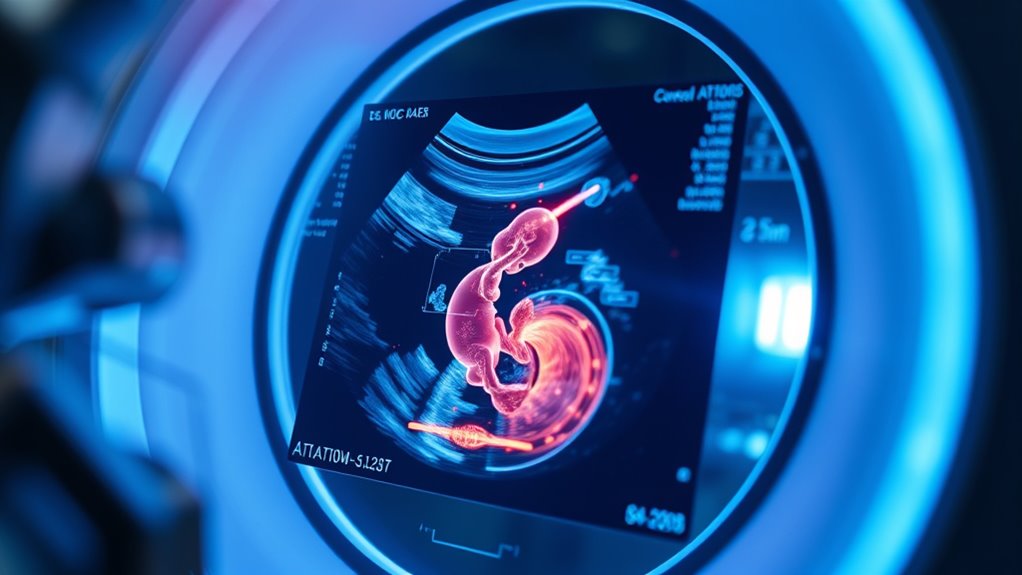
Predictive Quality Analytics is transforming how industries guarantee product excellence by leveraging data-driven insights. When you implement predictive quality strategies, you tap into the power of sensor integration, which allows real-time collection of critical data throughout your manufacturing process. These sensors continuously monitor variables like temperature, pressure, humidity, and other environmental factors that directly influence product quality. As data flows from these sensors, you gain immediate visibility into potential issues before they manifest as defects, giving you a proactive approach rather than reactive troubleshooting.
Once this data is collected, data visualization becomes your most valuable tool. Instead of sifting through endless spreadsheets, you can see complex information displayed in intuitive dashboards, charts, and heat maps. These visual insights help you quickly identify patterns, anomalies, or deviations from quality standards. For example, if a certain temperature fluctuation correlates with increased defect rates, data visualization makes that connection immediately apparent. This clarity enables you to make informed decisions faster, adjusting processes or stopping production if necessary, to prevent defective products from reaching customers.
Data visualization reveals patterns and anomalies, enabling quick, informed decisions to prevent defects and maintain quality standards.
By integrating sensors into your manufacturing environment, you create a continuous feedback loop that feeds into your predictive models. These models analyze historical and real-time data, forecasting potential defects with remarkable accuracy. Predictive analytics doesn’t just tell you what’s wrong; it anticipates problems before they happen. This foresight allows you to implement corrective measures in advance, reducing waste, saving costs, and maintaining high product standards. Over time, the system learns and improves its predictions, becoming more precise as more data accumulates.
In addition, understanding the role of personal growth concepts such as mental clarity and health can help teams stay focused and engaged with quality initiatives, fostering a culture of continuous improvement. Your ability to read defects before they occur substantially enhances quality control and operational efficiency. Instead of waiting for a defect to surface after production, you’re identifying trouble spots early in the process. This shift minimizes rework and scrap, ensuring your products meet stringent quality benchmarks. It also shortens your response times, as you’re not reacting to issues only after they’ve been detected visually or through customer feedback. Instead, you’re preventing defects from forming in the first place.
Frequently Asked Questions
How Accurate Are Predictive Analytics in Detecting Defects Early?
You might wonder how accurate predictive analytics are at detecting defects early. They rely on sensor accuracy, which has improved but isn’t perfect, so some false positives can occur. While these tools can identify potential issues with high sensitivity, no system is flawless. You should expect a good detection rate but remain cautious of occasional false alarms, emphasizing the importance of combining analytics with expert review for better reliability.
What Industries Benefit Most From Predictive Quality Analytics?
You’ll find that industries like manufacturing, healthcare, and aerospace benefit most from predictive quality analytics. They rely on real-time monitoring and advanced machine learning models to detect issues early, preventing costly errors. By analyzing data continuously, you can improve product quality and safety. These industries gain a competitive edge by reducing downtime and enhancing customer satisfaction through proactive defect detection and maintenance, making predictive analytics essential for their success.
Are There Privacy Concerns With Data Used in Predictive Analytics?
Think of data privacy as a delicate garden; you must protect its blooms. With predictive analytics, you handle sensitive info, raising ethical considerations about who accesses it and for what purpose. You need to guard against misuse, ensuring data privacy isn’t compromised. By respecting these boundaries, you maintain trust and integrity in your analytics efforts, acknowledging that ethical considerations are essential to safeguarding individuals’ rights and privacy.
How Cost-Effective Is Implementing Predictive Quality Systems?
Implementing predictive quality systems can be cost-effective if you conduct a thorough cost analysis upfront. While there are implementation challenges like integrating new technology and training staff, these costs often outweigh the long-term savings from early defect detection. You’ll reduce waste, improve product quality, and minimize costly recalls. Overall, with proper planning, the investment in predictive systems pays off by enhancing efficiency and lowering operational expenses.
What Are Future Trends in Predictive Quality Analytics Technology?
You’ll see future trends in predictive quality analytics involve more advanced machine learning algorithms that improve accuracy and speed. Sensor integration will become seamless, enabling real-time data collection from diverse sources. These innovations will allow you to identify potential issues early, reduce costs, and enhance product quality. As technology evolves, expect more intuitive systems that adapt to your needs, making predictive analytics more accessible and powerful across industries.
Conclusion
You might think predictive quality analytics is too complex or futuristic to apply now, but it’s already transforming manufacturing. By catching reading defects early, you prevent costly errors and improve product quality before birth. Don’t let skepticism hold you back—embrace these tools to stay ahead of potential issues. With the right technology, you’ll conserve time, reduce waste, and guarantee top-tier quality. The future of manufacturing is here; all it takes is your willingness to adapt.
Randy serves as our Software Quality Assurance Expert, bringing to the table a rich tapestry of industry experiences gathered over 15 years with various renowned tech companies. His deep understanding of the intricate aspects and the evolving challenges in SQA is unparalleled. At EarnQA, Randy’s contributions extend well beyond developing courses; he is a mentor to students and a leader of webinars, sharing valuable insights and hands-on experiences that greatly enhance our educational programs.